- お役立ち記事
- Remote Monitoring Systems Explore the Potential of Remote Control in Manufacturing
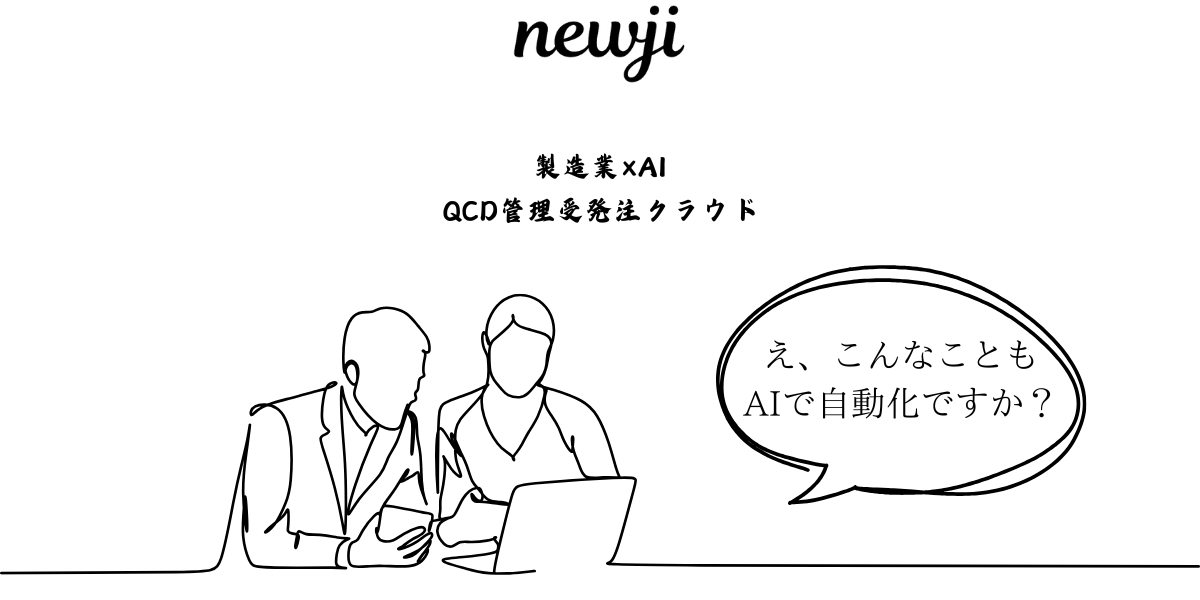
Remote Monitoring Systems Explore the Potential of Remote Control in Manufacturing
In today’s rapidly evolving manufacturing landscape, remote monitoring systems are emerging as a powerful tool for optimizing efficiency and productivity. With the advent of advanced technologies such as the Internet of Things (IoT) and cloud computing, manufacturers can now remotely monitor and control their operations from anywhere in the world. This article explores the potential of remote control in manufacturing and how it can revolutionize the industry.
What is Remote Monitoring?
Remote monitoring, also known as remote control or remote operation, refers to the ability to monitor and control manufacturing operations from a distance. This is made possible by connecting industrial equipment and machines to a centralized system that can be accessed remotely. By leveraging real-time data and advanced analytics, manufacturers can make informed decisions, identify issues, and optimize their processes without being physically present on the shop floor.
Benefits of Remote Monitoring in Manufacturing
1. Increased Efficiency
Remote monitoring systems enable manufacturers to streamline their operations and identify bottlenecks or inefficiencies in real-time. By continuously monitoring key performance indicators (KPIs), manufacturers can make data-driven decisions to improve productivity, reduce downtime, and optimize resource allocation.
2. Cost Savings
By remotely monitoring equipment and processes, manufacturers can detect potential issues before they become costly problems. This proactive approach allows for timely maintenance and reduces the need for expensive emergency repairs. Additionally, remote monitoring systems can help optimize energy usage, further reducing costs.
3. Improved Safety
Remote monitoring systems provide a safer working environment for employees by reducing the need for manual inspections and exposing workers to potential hazards. Real-time alerts and notifications can be sent to operators or maintenance teams in case of abnormal conditions, ensuring timely response and minimizing risks.
4. Enhanced Quality Control
With remote monitoring, manufacturers can closely monitor production parameters and detect deviations or defects in real-time. By catching quality issues early on, manufacturers can take immediate corrective actions, preventing wastage and ensuring consistent product quality.
5. Global Collaboration
Remote monitoring systems enable global collaboration by facilitating real-time communication and sharing of data and insights. This is especially beneficial for manufacturers with multiple factories or international operations, as it allows for the exchange of best practices, troubleshooting, and remote assistance.
Implementation Challenges and Solutions
While the potential benefits of remote monitoring in manufacturing are undeniable, there are some challenges that need to be addressed during implementation. These include data security, connectivity issues, interoperability, and workforce training.
To mitigate data security risks, manufacturers must ensure robust cybersecurity measures, such as encryption and authentication protocols, to protect sensitive data from unauthorized access. Additionally, implementing a reliable network infrastructure and establishing redundancy mechanisms can help address connectivity issues and ensure uninterrupted remote access.
Interoperability can be achieved by using standardized communication protocols, such as OPC Unified Architecture (OPC UA) or MQTT, to enable seamless integration of various manufacturing systems and devices. Additionally, investing in comprehensive training programs for employees can help them adapt to remote monitoring systems and maximize the benefits they offer.
Remote monitoring systems have the potential to revolutionize the manufacturing industry by enabling real-time monitoring and control of operations from anywhere in the world. By leveraging advanced technologies and data analytics, manufacturers can optimize efficiency, reduce costs, enhance safety, improve quality control, and foster global collaboration. However, it is important to address implementation challenges and invest in robust cybersecurity measures, reliable connectivity, interoperability, and workforce training to fully harness the benefits of remote control in manufacturing.
資料ダウンロード
QCD調達購買管理クラウド「newji」は、調達購買部門で必要なQCD管理全てを備えた、現場特化型兼クラウド型の今世紀最高の購買管理システムとなります。
ユーザー登録
調達購買業務の効率化だけでなく、システムを導入することで、コスト削減や製品・資材のステータス可視化のほか、属人化していた購買情報の共有化による内部不正防止や統制にも役立ちます。
NEWJI DX
製造業に特化したデジタルトランスフォーメーション(DX)の実現を目指す請負開発型のコンサルティングサービスです。AI、iPaaS、および先端の技術を駆使して、製造プロセスの効率化、業務効率化、チームワーク強化、コスト削減、品質向上を実現します。このサービスは、製造業の課題を深く理解し、それに対する最適なデジタルソリューションを提供することで、企業が持続的な成長とイノベーションを達成できるようサポートします。
オンライン講座
製造業、主に購買・調達部門にお勤めの方々に向けた情報を配信しております。
新任の方やベテランの方、管理職を対象とした幅広いコンテンツをご用意しております。
お問い合わせ
コストダウンが利益に直結する術だと理解していても、なかなか前に進めることができない状況。そんな時は、newjiのコストダウン自動化機能で大きく利益貢献しよう!
(Β版非公開)