- お役立ち記事
- ベンダー評価システムで高品質なサプライヤーを選定
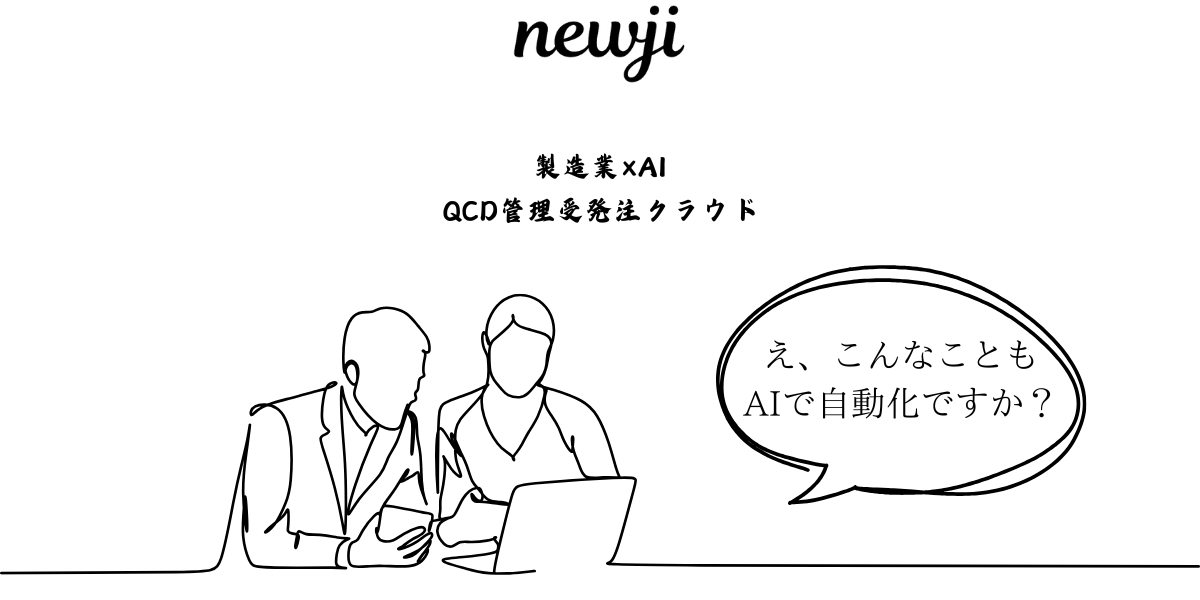
ベンダー評価システムで高品質なサプライヤーを選定
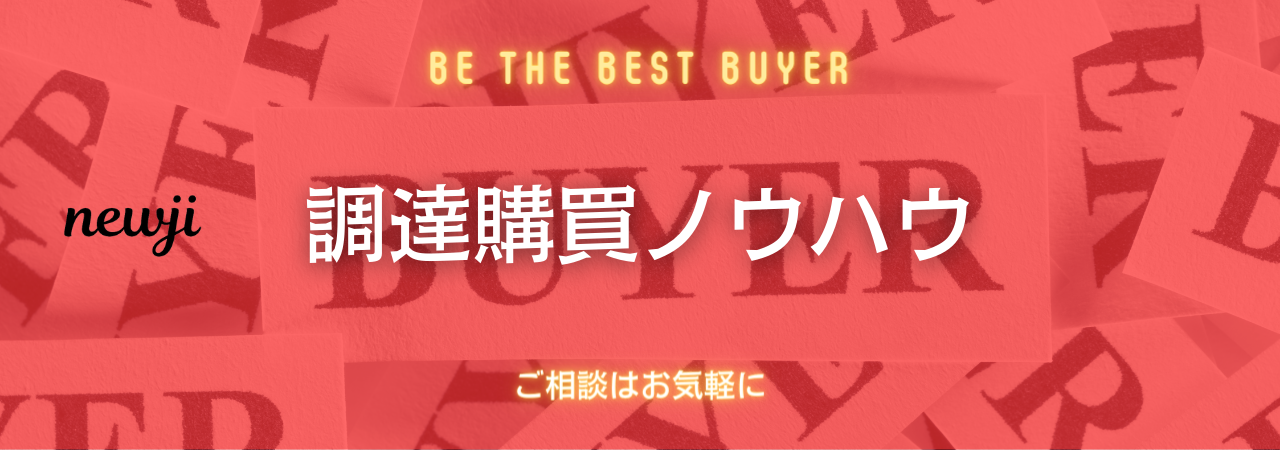
目次
はじめに
製造業において、サプライヤーの選定は製品の品質や生産効率に直接影響を与える重要なプロセスです。
サプライヤーが提供する部品や原材料の品質が低ければ、最終製品の品質にそのまま反映されるためです。
そこで多くの企業が採用しているのが「ベンダー評価システム」です。
本記事では、このベンダー評価システムの基本概念から具体的な実践方法、さらには最新の技術動向までを詳しく解説し、高品質なサプライヤー選定のための実践的な情報を提供します。
ベンダー評価システムの基本概念
ベンダー評価システムとは、サプライヤー(ベンダー)の能力や信頼性、品質、納期遵守率などを評価・分析し、最適なサプライヤーを選定するためのツールやプロセスを指します。
このシステムを導入することで、企業は一貫した高品質の製品を生産し、市場での競争力を高めることができます。
評価項目の設定
ベンダー評価システムの第一歩は、評価項目を明確に設定することです。
一般的には以下のような項目が評価の対象となります。
– 品質: 提供される製品やサービスの品質。
– 価格: サプライヤーの価格競争力。
– 納期: 納期遵守率と納品の迅速さ。
– 信頼性: 過去の取引実績やトラブル対応能力。
– コミュニケーション: コミュニケーションの円滑さと対応の迅速さ。
これらの評価項目に基づき、各サプライヤーをスコアリングして総合評価を行います。
評価の手法
評価手法には定性的なものと定量的なものがあります。
定性的評価は、具体的な数値に基づかない主観的な評価を指します。
一方、定量的評価は具体的なデータや指標に基づいて評価を行います。
多くの企業では、これらを組み合わせたハイブリッド評価手法を採用しています。
フィードバックと改善
評価結果をもとに、サプライヤーには改善点のフィードバックを行います。
これにより、サプライヤーも自己改善を図ることができ、双方にとってメリットが生まれます。
実践的なベンダー評価システム導入のプロセス
では、具体的にベンダー評価システムをどのように導入すればよいのでしょうか。
ここでは、一般的なプロセスを紹介します。
ステップ1: 目標設定と評価基準の決定
まずは、自社の目標やニーズに応じた評価基準を設定します。
これには、製品の特性や市場の要求、企業の戦略などを考慮します。
ステップ2: サプライヤーのリストアップ
次に、評価対象となるサプライヤーをリストアップします。
既存のサプライヤーだけでなく、新規参入のサプライヤーも含めることが大切です。
ステップ3: 評価方法の策定
定性的評価と定量的評価を組み合わせた評価方法を策定します。
たとえば、定性的評価には業務担当者からのヒアリングやアンケートを使用し、定量的評価には納期遵守率や不良品の発生率などのデータを活用します。
ステップ4: 評価実施とデータ分析
評価基準に基づいて、各サプライヤーの評価を実施します。
評価結果はデータベースに集約し、分析を行います。
ここでは、データの偏りや主観を排除することが重要です。
ステップ5: フィードバックと共に改善提案
評価結果をもとに、各サプライヤーにフィードバックを行います。
これには、改善点や強化すべきポイントを具体的に伝えることが求められます。
また、定期的な評価を行い、サプライヤーの改善状況をモニタリングします。
最新の技術動向とベンダー評価のデジタル化
製造業のデジタル化が進む中、ベンダー評価システムもまたデジタルツールやプラットフォームを活用して高度化しています。
ビッグデータ解析の活用
ビッグデータ解析を活用することで、従来の手法では見落としがちな細かなデータを収集・分析することが可能です。
これにより、より精緻で客観的なサプライヤー評価が実現します。
クラウドベースの評価プラットフォーム
多くの企業がクラウドベースの評価プラットフォームを導入しています。
これにより、リアルタイムでのデータ共有や分析が可能となり、グローバルなサプライチェーン管理が強化されます。
AIと機械学習の応用
AI(人工知能)や機械学習を利用して、サプライヤーの評価プロセスを自動化する試みも進んでいます。
これにより、評価の精度が向上するだけでなく、人的リソースの削減も期待できます。
成功事例とその効果
ベンダー評価システムを導入することで、どのような成果が得られるのでしょうか。
ここでは、いくつかの成功事例を紹介します。
事例1: 大手自動車メーカーのケース
ある大手自動車メーカーは、ベンダー評価システムを導入したことで、サプライヤーの品質向上と納期遵守率の向上を実現しました。
具体的には、評価結果をもとにサプライヤーとの連携を強化し、不良品の発生率を大幅に削減することができました。
事例2: 電子機器メーカーのケース
電子機器メーカーでは、クラウドベースの評価プラットフォームを導入することで、グローバルなサプライチェーンの管理を効率化しました。
これにより、各国のサプライヤーの評価結果をリアルタイムで監視し、迅速な対応が可能となりました。
事例3: 食品業界のケース
食品業界でも、ベンダー評価システムを導入することで、原料サプライヤーの品質管理を徹底しました。
特に、食品の安全性が求められる中、評価システムの導入は顧客からの信頼を獲得するカギとなりました。
まとめ
ベンダー評価システムを導入することで、製造業におけるサプライヤー選定の精度が向上し、高品質な製品の提供が可能となります。
特に、最新のデジタル技術を駆使することで、評価プロセスの効率化と精度向上が実現します。
各企業が自身のニーズに合った評価システムを構築し、サプライヤーとの良好な関係を築くことが、今後の競争力強化の一つの指針となるでしょう。
資料ダウンロード
QCD調達購買管理クラウド「newji」は、調達購買部門で必要なQCD管理全てを備えた、現場特化型兼クラウド型の今世紀最高の購買管理システムとなります。
ユーザー登録
調達購買業務の効率化だけでなく、システムを導入することで、コスト削減や製品・資材のステータス可視化のほか、属人化していた購買情報の共有化による内部不正防止や統制にも役立ちます。
NEWJI DX
製造業に特化したデジタルトランスフォーメーション(DX)の実現を目指す請負開発型のコンサルティングサービスです。AI、iPaaS、および先端の技術を駆使して、製造プロセスの効率化、業務効率化、チームワーク強化、コスト削減、品質向上を実現します。このサービスは、製造業の課題を深く理解し、それに対する最適なデジタルソリューションを提供することで、企業が持続的な成長とイノベーションを達成できるようサポートします。
オンライン講座
製造業、主に購買・調達部門にお勤めの方々に向けた情報を配信しております。
新任の方やベテランの方、管理職を対象とした幅広いコンテンツをご用意しております。
お問い合わせ
コストダウンが利益に直結する術だと理解していても、なかなか前に進めることができない状況。そんな時は、newjiのコストダウン自動化機能で大きく利益貢献しよう!
(Β版非公開)