- お役立ち記事
- 「不良ゼロ」への具体的なアプローチ
「不良ゼロ」への具体的なアプローチ
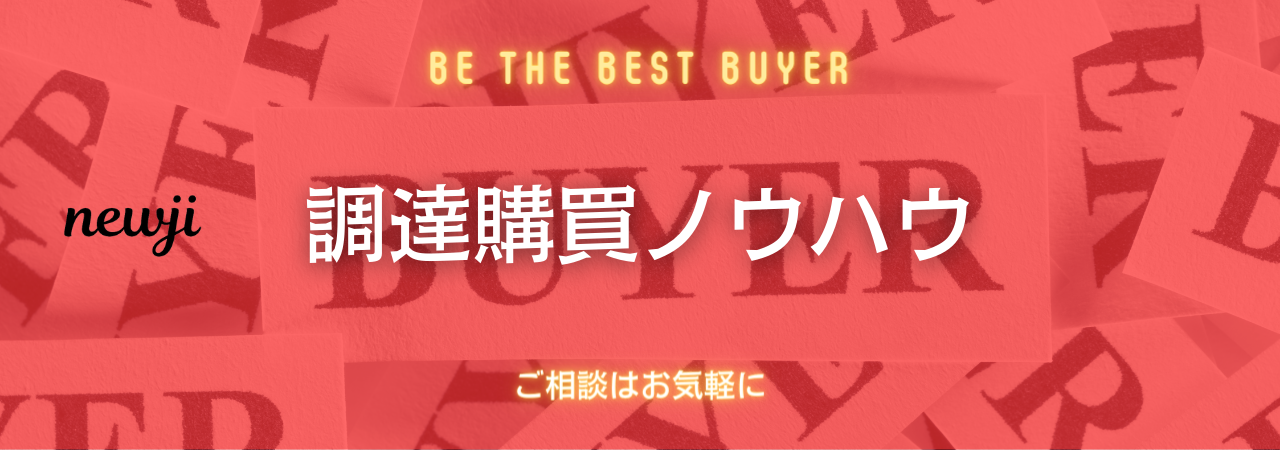
目次
はじめに
製造業において「不良ゼロ」は理想であり、多くの企業がこの目標を達成するために日々努力しています。
しかし、実際には多くの課題が存在し、その達成には高いハードルが立ちはだかります。
この記事では、製造業における「不良ゼロ」への具体的なアプローチについて解説します。
実践的な内容や最新の技術動向も交え、現場目線からの具体的な手法をご紹介します。
不良ゼロの重要性
顧客満足度の向上
不良品が発生すると、顧客に対してマイナスのイメージを与え、信頼を失う可能性があります。
顧客満足度の向上は、企業の持続的な成長に不可欠です。
そのため、不良品の削減は顧客満足度の向上に直結します。
例えば、自動車業界においては、リコールが発生すると顧客の信頼を大きく損ないます。
「不良ゼロ」を目指すことで、顧客からの信頼を確保し、ブランド価値を高めることができます。
コスト削減
不良品の発生は、製造過程においてコストがかかります。
再作業や材料の無駄、さらに不良品の処理などがその要因です。
これらのコストは、企業の利益を圧迫します。
「不良ゼロ」を目指すことで、無駄なコストを削減し、結果的に企業の収益性を向上させることができます。
従業員のモチベーションアップ
不良品が多いと、従業員の士気が下がり、作業効率が低下します。
逆に、高品質な製品を作り上げることができる環境を整えることで、従業員のモチベーションが向上します。
「不良ゼロ」を目指すプロジェクトに従業員を参画させることで、一体感が高まり職場全体の士気向上にもつながります。
不良ゼロへの具体的なアプローチ
品質管理の強化
品質管理を徹底することは、不良品の削減に直結します。
以下のような具体的な手法があります。
標準作業手順書の作成と遵守
標準作業手順書を作成し、従業員がそれに従って作業を行うことで品質のばらつきを減少させることができます。
さらに、定期的に手順書を見直し、最新の情報を反映させることが重要です。
品質監査の実施
内部監査と外部監査を定期的に実施することで、品質管理の状況を確認し、改善点を洗い出すことが可能です。
監査結果を基にしたPDCAサイクル(Plan-Do-Check-Act)の実践が効果的です。
生産管理の効率化
生産管理の効率化は、不良品を減少させるための重要な要素です。
生産計画の最適化
生産計画を最適化することで、工程中のムダやロスを減少させることができます。
需要予測を基にした計画立案やリアルタイムでの進捗管理が求められます。
ラインバランシングの最適化
製造ラインのバランシングを最適化することで、作業負荷を均等に分散し、不良発生のリスクを低減させることができます。
ボトルネックの特定とその改善が肝要です。
工場の自動化とデジタル化
現代の製造業では、工場の自動化とデジタル化が進んでいます。
これにより、高度な品質管理や効率的な生産管理が可能になります。
IoT技術の活用
IoT技術を活用することで、製造ラインの状況をリアルタイムで監視し、異常が発生した際には即座に対策を講じることができます。
これにより、不良品の発生を未然に防ぐことができます。
デジタルツインの導入
デジタルツイン技術を導入することで、製品やプロセスの仮想モデルを作成し、実際の製造過程で発生する可能性のある不良をシミュレーションで事前に検出することができます。
これにより、実際の製造ラインでの不良発生を大幅に削減できます。
サプライヤーとの連携強化
サプライヤーとの連携を強化することで、部品や材料の品質を確保し、不良品の発生を防ぐことが可能です。
サプライヤー評価システムの導入
サプライヤーの品質評価を定期的に行い、優れたサプライヤーとの取引関係を継続することが重要です。
評価結果を基にした改善要請やフォローアップも欠かせません。
共同プロジェクトの実施
サプライヤーと共同プロジェクトを実施することで、品質向上に向けた取り組みを共有し、連携強化を図ります。
例えば、部品の設計段階から品質を考慮したアプローチを取ることが考えられます。
最新技術による品質向上の取り組み
AI技術の活用
AI技術は、不良品の発生を未然に防ぐための強力なツールです。
画像認識による検査の自動化
AIを活用した画像認識技術により、製品の外観検査を自動化することができます。
人間の目では見逃してしまうような微細な不良も、高精度の画像認識技術を用いることで検出が可能となります。
機械学習による予測保全
機械学習アルゴリズムを利用して、設備の故障を予測し、事前にメンテナンスを行うことで不良品の発生を防ぎます。
これにより、予期せぬダウンタイムを防ぎ、安定した生産を維持することができます。
ブロックチェーン技術の導入
ブロックチェーン技術を導入することで、製品の生産履歴をトレースしやすくなり、不良品の原因を迅速に特定することが可能です。
トレーサビリティの向上
ブロックチェーンを活用することで、製品の製造段階ごとのデータを詳細に記録し、トレーサビリティを確保します。
これにより、不良品発生時に迅速に原因を特定し、対策を講じることができます。
透明性の確保
サプライチェーン全体の透明性を確保することで、不良品の原因となる要素を排除することが可能です。
サプライヤーからの情報をブロックチェーンで共有し、リアルタイムでの情報監視が実現します。
まとめ
「不良ゼロ」へのアプローチは、多岐にわたり、様々な手法や技術が必要です。
品質管理、生産管理の強化、自動化技術の導入、サプライヤーとの連携強化など、各方面からのアプローチを総合的に実施することが重要です。
さらに、最新のAI技術やブロックチェーン技術を積極的に活用することで、より効果的な不良品削減が期待できます。
製造業の現場で培った知識や経験を活かし、「不良ゼロ」を目指して取り組んでいきましょう。
資料ダウンロード
QCD調達購買管理クラウド「newji」は、調達購買部門で必要なQCD管理全てを備えた、現場特化型兼クラウド型の今世紀最高の購買管理システムとなります。
ユーザー登録
調達購買業務の効率化だけでなく、システムを導入することで、コスト削減や製品・資材のステータス可視化のほか、属人化していた購買情報の共有化による内部不正防止や統制にも役立ちます。
NEWJI DX
製造業に特化したデジタルトランスフォーメーション(DX)の実現を目指す請負開発型のコンサルティングサービスです。AI、iPaaS、および先端の技術を駆使して、製造プロセスの効率化、業務効率化、チームワーク強化、コスト削減、品質向上を実現します。このサービスは、製造業の課題を深く理解し、それに対する最適なデジタルソリューションを提供することで、企業が持続的な成長とイノベーションを達成できるようサポートします。
オンライン講座
製造業、主に購買・調達部門にお勤めの方々に向けた情報を配信しております。
新任の方やベテランの方、管理職を対象とした幅広いコンテンツをご用意しております。
お問い合わせ
コストダウンが利益に直結する術だと理解していても、なかなか前に進めることができない状況。そんな時は、newjiのコストダウン自動化機能で大きく利益貢献しよう!
(Β版非公開)