- お役立ち記事
- 実装対応の成功事例と調達におけるリスク管理方法
月間76,176名の
製造業ご担当者様が閲覧しています*
*2025年3月31日現在のGoogle Analyticsのデータより
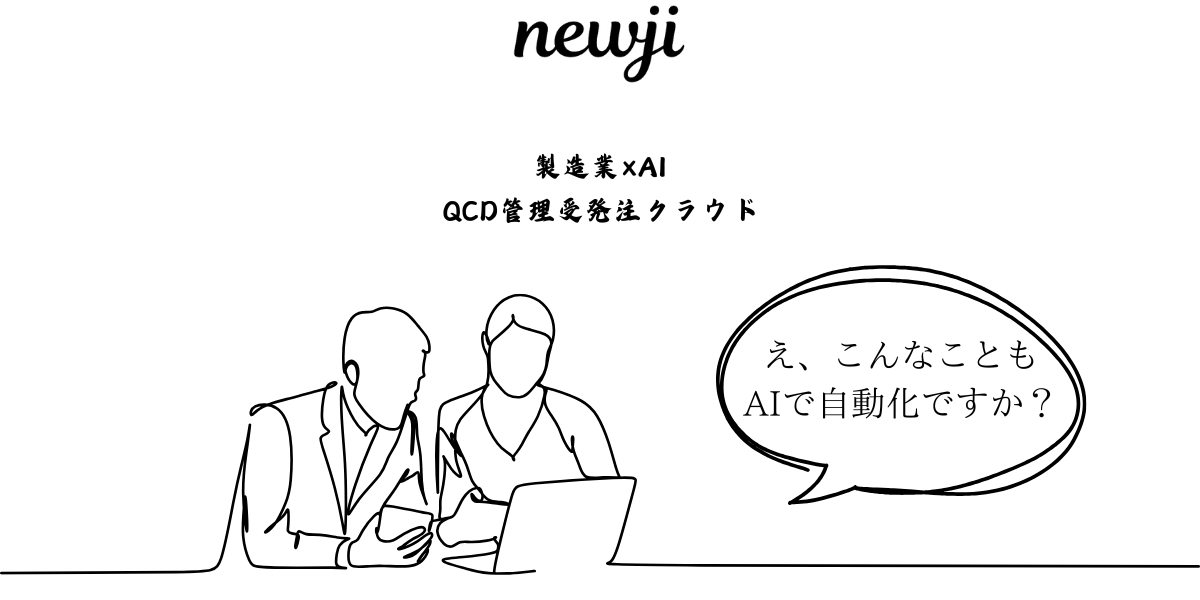
実装対応の成功事例と調達におけるリスク管理方法
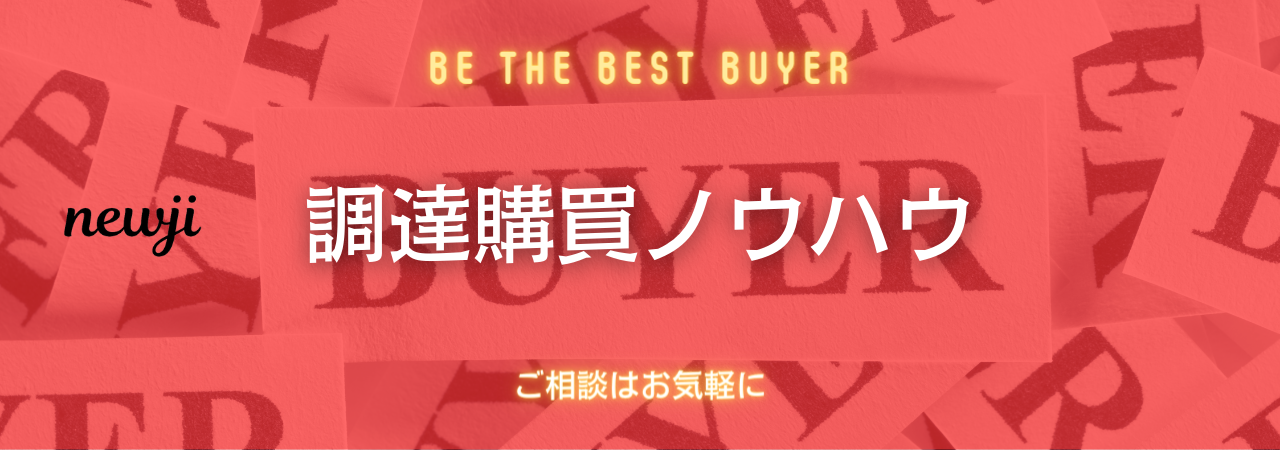
目次
はじめに
製造業において、技術の急速な進歩や市場の変動に迅速に対応しつつ、効果的なリスク管理を行うことは非常に重要です。
特に、実装対応や調達に関する作業は、企業の業績と成長に直結するため、その重要性は言うまでもありません。
本記事では、製造業の現場で培った知識と経験に基づき、実装対応の成功事例および調達におけるリスク管理方法について詳しく解説します。
実装対応の成功事例
成功した実装対応の事例を通じて、そのプロセスやポイントを具体的に見ていきます。
事例1:新規生産ラインの導入
ある大手製造業メーカーでは、新製品の需要増加に対応するため、新規生産ラインを導入する必要がありました。
プロジェクトチームが結成され、計画立案から実行まで一貫して進められました。
1. **計画立案**
生産ラインの設計、必要な設備の選定、予算の策定が行われました。
各ステークホルダーの意見を取り入れ、リスク評価を実施しました。
2. **試運転と調整**
新しい設備が導入された後、試運転と微調整が行われ、問題点を洗い出しました。
この段階で予見された課題を早期に解決することができました。
3. **トレーニングと教育**
新しい生産ラインに対応するため、オペレーターや技術者に対して徹底したトレーニングを実施しました。
熟練度を上げるための教育プログラムを設け、実操作と理論の両面から学びを深めました。
4. **稼働後のフォローアップ**
新規ラインが本格的に稼働した後も、継続的にデータをモニタリングし、改善点を見つける体制を維持しました。
これにより、潜在的な問題が発生する前に対処することができました。
この事例では、事前の計画立案と試運転、継続的な教育とフォローアップがキーとなり、新規生産ラインの導入がスムーズに進みました。
事例2:品質管理システムのアップデート
品質管理を厳格にし、顧客満足度を向上させるため、あるメーカーでは品質管理システムを最新のものにアップデートしました。
1. **現状評価と課題の洗い出し**
まず既存の品質管理システムの評価を行い、どこに問題があるのかを明確にしました。
そして、改善が必要な部分をリスト化しました。
2. **システム選定とベンダー選び**
複数のシステムを比較し、自社に最適なものを選定しました。
信頼性とコストを考慮し、ベンダーと詳細な交渉を重ねました。
3. **導入計画の策定と実行**
導入計画を策定し、ステークホルダー全員に共有しました。
段階的にシステムを導入し、トライアルとフィードバックを繰り返しつつ最終的な調整を行いました。
4. **データ移行とトレーニング**
旧システムから新システムへのデータ移行をスムーズに行い、従業員に対してトレーニングを実施しました。
5. **稼働後のモニタリング**
新しい品質管理システムが稼働した後も、継続的にモニタリングを行い、問題発生時には即座に対応しました。
この事例では、現状評価と改善計画の明確化、段階的な導入とトレーニングが成功の鍵となりました。
調達におけるリスク管理方法
調達におけるリスク管理は、製造業において極めて重要です。
適切なリスク管理を行うことで、調達の信頼性を高め、コスト削減や納期遵守に貢献できます。
リスクの洗い出しと評価
1. **リスクの識別**
調達プロセスにおいてどのようなリスクが存在するのかを洗い出します。
一般的なリスク要因としては、サプライヤーの信頼性、原材料の価格変動、輸送の遅延などが挙げられます。
2. **リスク評価**
識別されたリスクについて、その影響度と発生確率を評価します。
これにより、優先的に対処すべきリスクが明確になります。
リスク対応策の策定と実行
1. **リスク対応策の策定**
リスク管理計画を策定し、リスクに対してどのように対応するかを具体的に決めます。
例えば、リスクの回避、リスクの軽減、リスクの移転、あるいはリスクの受容などの戦略を選択します。
2. **サプライチェーンの強化**
多様なサプライヤーとの関係を築き、一社依存を避けることでリスクを分散します。
また、サプライヤーの評価とモニタリングを定期的に行い、信頼性を確保します。
3. **在庫管理と予測手法の導入**
適切な在庫管理と需要予測手法を導入し、供給チェーンの安定性を高めます。
これにより、需給のミスマッチを防ぎ、供給不足や過剰在庫のリスクを軽減します。
リスク管理の実践事例
調達におけるリスク管理は理論だけでなく実践も重要です。
ここでは、成功事例を紹介します。
**事例:多様なサプライチェーンの構築**
ある電子部品メーカーでは、一部の部品供給に対する依存度が高かったため、供給不足のリスクが懸念されていました。
そこで、以下のアプローチを取りました。
1. **サプライヤーの多様化**
主要部品に対して複数のサプライヤーを確保し、一社依存から脱却しました。
新規サプライヤーとの契約を結び、供給安定性を高めました。
2. **定期的な評価とフィードバック**
サプライヤーのパフォーマンスを定期的に評価し、フィードバックを行いました。
これにより、サプライヤーの改善点を共有し、共同でリスク軽減策を進めました。
3. **予測システムの導入**
需要予測システムを導入し、需要変動に対する柔軟な対応が可能になりました。
これにより、在庫量を最適化し、リスクを最小限に抑えることができました。
この事例では、サプライチェーンの多様化と需給予測の精度向上が成功の要因となりました。
まとめ
製造業における実装対応と調達におけるリスク管理は、企業の競争力を高めるために欠かせない要素です。
成功事例から学ぶことで、より効果的な戦略やプロセスを導入できるでしょう。
リスクを事前に識別し、適切に対応することで、安定した生産活動を維持し、さらなる成長を遂げることができます。
以上、実践的な内容を基に、製造業の現場で役立つ情報を提供いたしました。
ぜひ、自社のプロジェクトに取り入れてみてください。
資料ダウンロード
QCD管理受発注クラウド「newji」は、受発注部門で必要なQCD管理全てを備えた、現場特化型兼クラウド型の今世紀最高の受発注管理システムとなります。
ユーザー登録
受発注業務の効率化だけでなく、システムを導入することで、コスト削減や製品・資材のステータス可視化のほか、属人化していた受発注情報の共有化による内部不正防止や統制にも役立ちます。
NEWJI DX
製造業に特化したデジタルトランスフォーメーション(DX)の実現を目指す請負開発型のコンサルティングサービスです。AI、iPaaS、および先端の技術を駆使して、製造プロセスの効率化、業務効率化、チームワーク強化、コスト削減、品質向上を実現します。このサービスは、製造業の課題を深く理解し、それに対する最適なデジタルソリューションを提供することで、企業が持続的な成長とイノベーションを達成できるようサポートします。
製造業ニュース解説
製造業、主に購買・調達部門にお勤めの方々に向けた情報を配信しております。
新任の方やベテランの方、管理職を対象とした幅広いコンテンツをご用意しております。
お問い合わせ
コストダウンが利益に直結する術だと理解していても、なかなか前に進めることができない状況。そんな時は、newjiのコストダウン自動化機能で大きく利益貢献しよう!
(β版非公開)