- お役立ち記事
- The Fusion of Digital and Reality AR/VR in Manufacturing
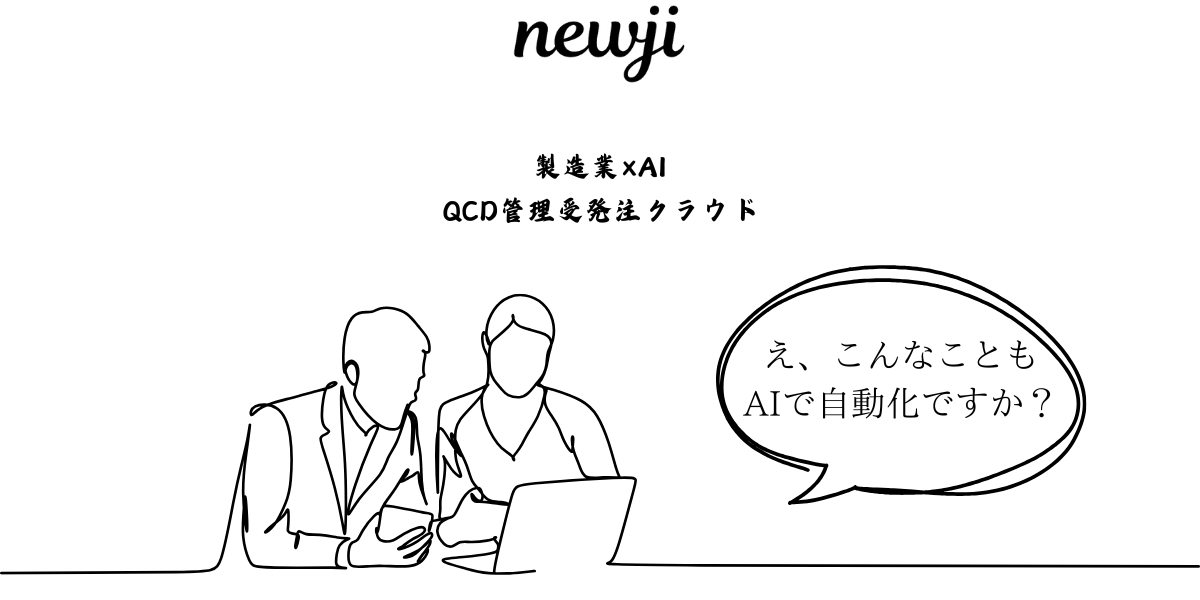
The Fusion of Digital and Reality AR/VR in Manufacturing
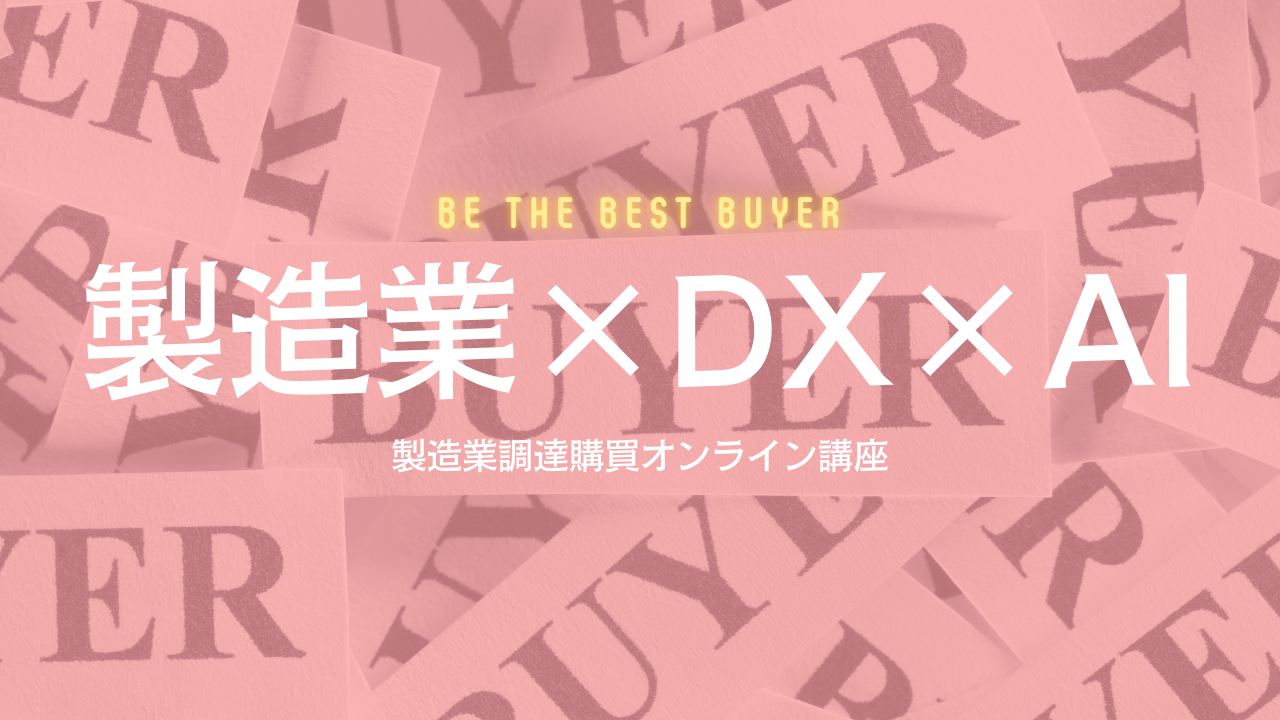
The manufacturing industry has traditionally relied on physical machinery and processes to design, build, and test products.
However, new technologies like augmented reality (AR) and virtual reality (VR) are allowing manufacturers to “fuse the digital and the real.” AR and VR are transforming how manufacturers design complex products, train employees, and collaborate with partners worldwide.
AR enhances the real world by overlaying digital information.
With AR, manufacturers can overlay digital schematics, assembly instructions, or other information directly onto physical products or prototypes as they are being built. Workers can see annotations, measurements, or instructions on transparent displays without having to continuously refer back to manuals or diagrams.
This streamlines production and assembly processes. AR is also being used in product design. Engineers can overlay digital designs directly onto spaces to see how a product might fit before building physical prototypes. They can collaborate remotely by sharing AR experiences.
VR fully immerses users in digital environments through headsets.
Manufacturers are using VR for virtual prototyping and testing. Complex products like airplanes, cars, and industrial equipment are too expensive to repeatedly build physical prototypes.
With VR, digital prototypes can be engineered, tested, and improved virtually before a single physical part is made.
Engineers can walk around and interact with virtual prototypes to spot design flaws or points of failure.
They can review prototypes with international partners in VR without the need for travel.
VR is also being used for complex employee training. Rather than traditional manuals or videos, workers can experience virtual simulations of their tasks and environments.
Both AR and VR are helping reduce costs for manufacturers.
By identifying issues with digital prototypes earlier in the design process, fewer physical prototypes need to be built, tested, and reworked. Fewer late stage changes mean less time and materials wasted.
AR and VR enable remote global collaboration, reducing the need for travel.
Employees can be trained more quickly and effectively through virtual simulations rather than manuals or trial and error on production equipment.
Overall, AR and VR allow manufacturers to be more efficient, flexible, and achieve higher product quality sooner.
While the opportunities are great, there are still some challenges to mainstream adoption of AR and VR in manufacturing.
High-quality AR and VR systems can be expensive to deploy across whole factories and production lines.
Technical challenges remain around stability, field of view, and user fatigue over extended periods of work. Software ecosystems and content libraries are still developing robust specialized applications for manufacturing workflows.
Safety must also be considered, as AR and VR could potentially distract workers or obstruct situational awareness in some production environments.
As technology improves and costs decline, adoption will likely accelerate.
Many major manufacturers have already integrated AR and VR into workflows.
Boeing uses HoloLens AR headsets to overlay technical instructions for assembly tasks. Daimler uses VR to train technicians on maintenance of large machinery.
SpaceX designs rockets in VR and reviews prototypes virtually before building.
As the benefits become clearer, and new generations familiar with these technologies enter the workforce, AR and VR will continue to reshape how production is planned, tested, and carried out.
In the future, it may be hard to distinguish where the digital ends and the real manufacturing begins.
In summary, augmented reality (AR) and virtual reality (VR) are bringing the digital world into the physical processes of manufacturing.
By fusing real and virtual, these technologies allow manufacturers to design, test, and collaborate in new immersive ways.
While technical and adoption challenges remain, AR and VR promise to make production more efficient, flexible and globally connected.
As the tools evolve, these cutting-edge methods will transform how future factories function to the benefit of businesses and customers.
The fusion of digital and real has only begun, with greater integrations of AR and VR on the manufacturing horizon.
資料ダウンロード
QCD調達購買管理クラウド「newji」は、調達購買部門で必要なQCD管理全てを備えた、現場特化型兼クラウド型の今世紀最高の購買管理システムとなります。
ユーザー登録
調達購買業務の効率化だけでなく、システムを導入することで、コスト削減や製品・資材のステータス可視化のほか、属人化していた購買情報の共有化による内部不正防止や統制にも役立ちます。
NEWJI DX
製造業に特化したデジタルトランスフォーメーション(DX)の実現を目指す請負開発型のコンサルティングサービスです。AI、iPaaS、および先端の技術を駆使して、製造プロセスの効率化、業務効率化、チームワーク強化、コスト削減、品質向上を実現します。このサービスは、製造業の課題を深く理解し、それに対する最適なデジタルソリューションを提供することで、企業が持続的な成長とイノベーションを達成できるようサポートします。
オンライン講座
製造業、主に購買・調達部門にお勤めの方々に向けた情報を配信しております。
新任の方やベテランの方、管理職を対象とした幅広いコンテンツをご用意しております。
お問い合わせ
コストダウンが利益に直結する術だと理解していても、なかなか前に進めることができない状況。そんな時は、newjiのコストダウン自動化機能で大きく利益貢献しよう!
(Β版非公開)