- お役立ち記事
- The Key to Efficiency Manufacturing Digitalization Strategies to Reduce Costs
The Key to Efficiency Manufacturing Digitalization Strategies to Reduce Costs
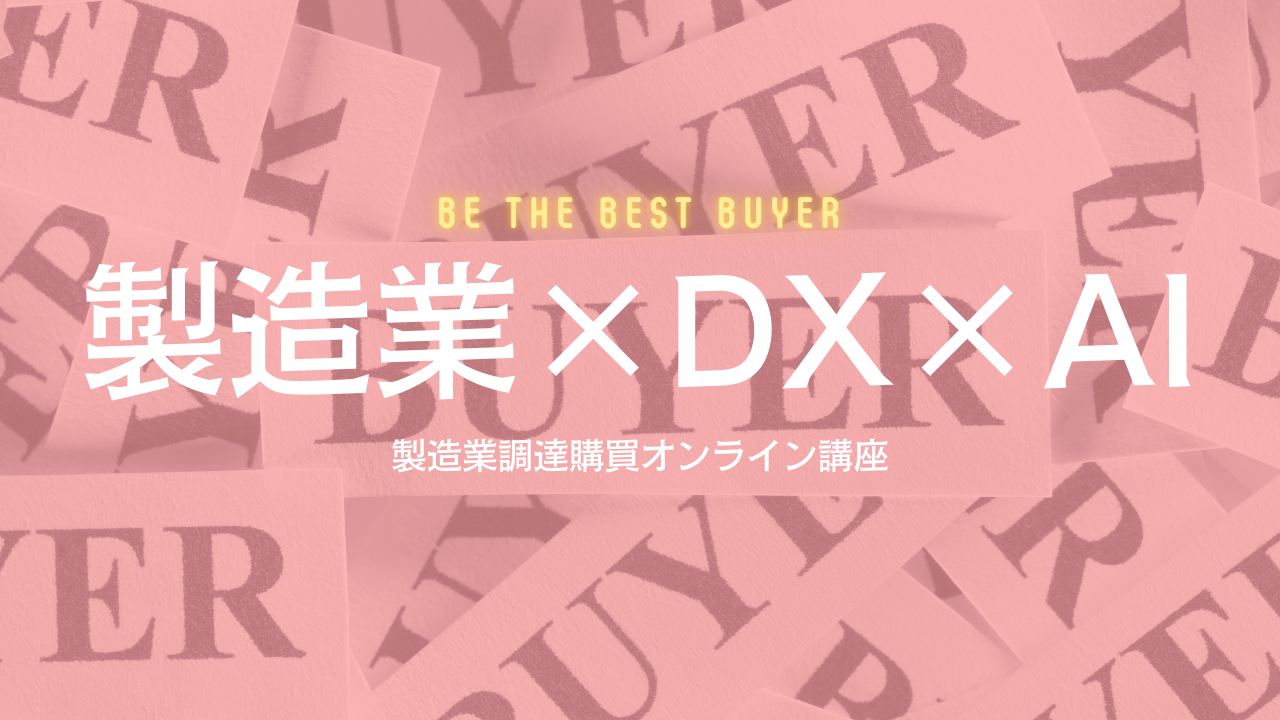
Digital technologies like advanced robotics, artificial intelligence, and data analytics are helping manufacturers reduce costs and improve efficiency in innovative new ways. By embracing digitalization strategies, companies have found proven methods to streamline production processes, minimize waste, and maximize output—all while minimizing expenses.
A major focus of digital transformation efforts revolves around robotics and automation. Robotic process automation (RPA) uses software bots to handle repetitive, routine administrative tasks previously done by human employees. This frees up staff to focus on more engaging, strategic work instead of tedious data entry or form filling tasks. RPAs can work 24/7 without breaks, resulting in round-the-clock productivity gains. Manufacturers in industries like automotive, electronics, and food processing have seen labor costs reduced by 30-50% by implementing various forms of robotic automation.
Advanced robotics also provides advantages on the production floor. Collaborative robots or “cobots” are designed to safely work alongside human workers without endangering their safety. This allows previously human-only production tasks to be partially or fully automated while retaining a human workforce. Companies install cobots to take over strenuous, hazardous, or physically demanding jobs, reducing injuries and improving ergonomics. AGVs or automated guided vehicles also transport materials through factories automatically via guidance systems like lasers, magnets, or vision cameras, streamlining logistics and boosting throughput.
Predictive maintenance powered by AI and big data analytics saves substantial costs by preventing downtime before it occurs. Sensor-enabled industrial equipment transmits constant streams of performance data that AI systems analyze to detect early signs of impending failures or inefficiencies. By receiving advanced warnings, production managers can schedule maintenance at optimal low-activity times instead of emergencies disrupting schedules. Manufacturers report uptime improvements of 15-30% through predictive maintenance strategies, minimizing costly disruptions.
The Industrial Internet of Things (IIoT) further enhances productivity by connecting all phases of operations. Embedded sensors provide real-time visibility into production metrics, quality control, energy usage, asset performance, and more. IIoT platforms integrate previously siloed data sources into centralized environments where AI-driven analytics generate actionable insights. These help optimize processes, minimize changeover times between product runs, eliminate defects and waste, conserve energy, and maximize output according to demand signals. Dow Chemical, for instance, saved $250 million annually through IIoT-powered efficiency gains across its facilities worldwide.
Digital twins—virtual simulations of real-world systems, assets, and processes—have revolutionized manufacturing agility. Digital twins capture the attributes and performance characteristics of everything from individual machines to entire networked factories through sensor data synchronization. This allows virtual modeling, testing, and optimization of improvements long before physical implementation. Any design changes, process flows, or upgrades can undergo exhaustive simulations that predict downstream impacts, costs, and outcomes—mitigating risk. For example, airplane manufacturer Airbus shaved two years off production timelines and saved billions using digital twin technology for manufacturing modeling.
Additive manufacturing aka 3D printing unlocks untapped efficiencies by freeing production from expensive tooling constraints. Rather than costlier techniques like injection molding that require durable tooling, 3D printers can rapidly produce prototypes and end-use parts on demand without these fixed costs. They print parts layer by layer directly from digital designs, accelerating product development cycles. Boeing, for one, cuts $300 million in production costs yearly by 3D printing over 300 different aerospace components. Diversified manufacturers continue finding more industrial applications for additive technologies across industries.
As advanced digital methods like robotics, IoT, additive manufacturing, AI, and digital twins make inroads, they will transform global industry from top to bottom. Early adopters already gaining competitive advantages prove digital transformation delivers measurable productivity gains and cost reductions. But these gains barely scratch the surface of opportunities as technologies continue advancing. Manufacturers taking a proactive, innovation-first approach to digitalization strategies position themselves to sustain profitability in changing times—continually finding new efficiencies that may one day reshape entire sectors. By embracing digitalization and new industry 4.0 technologies, smart companies can thrive where laggards struggle in coming years.
資料ダウンロード
QCD調達購買管理クラウド「newji」は、調達購買部門で必要なQCD管理全てを備えた、現場特化型兼クラウド型の今世紀最高の購買管理システムとなります。
ユーザー登録
調達購買業務の効率化だけでなく、システムを導入することで、コスト削減や製品・資材のステータス可視化のほか、属人化していた購買情報の共有化による内部不正防止や統制にも役立ちます。
NEWJI DX
製造業に特化したデジタルトランスフォーメーション(DX)の実現を目指す請負開発型のコンサルティングサービスです。AI、iPaaS、および先端の技術を駆使して、製造プロセスの効率化、業務効率化、チームワーク強化、コスト削減、品質向上を実現します。このサービスは、製造業の課題を深く理解し、それに対する最適なデジタルソリューションを提供することで、企業が持続的な成長とイノベーションを達成できるようサポートします。
オンライン講座
製造業、主に購買・調達部門にお勤めの方々に向けた情報を配信しております。
新任の方やベテランの方、管理職を対象とした幅広いコンテンツをご用意しております。
お問い合わせ
コストダウンが利益に直結する術だと理解していても、なかなか前に進めることができない状況。そんな時は、newjiのコストダウン自動化機能で大きく利益貢献しよう!
(Β版非公開)