- お役立ち記事
- トヨタ流「なぜなぜ分析」による真因追及とトラブル未然防止への応用
トヨタ流「なぜなぜ分析」による真因追及とトラブル未然防止への応用
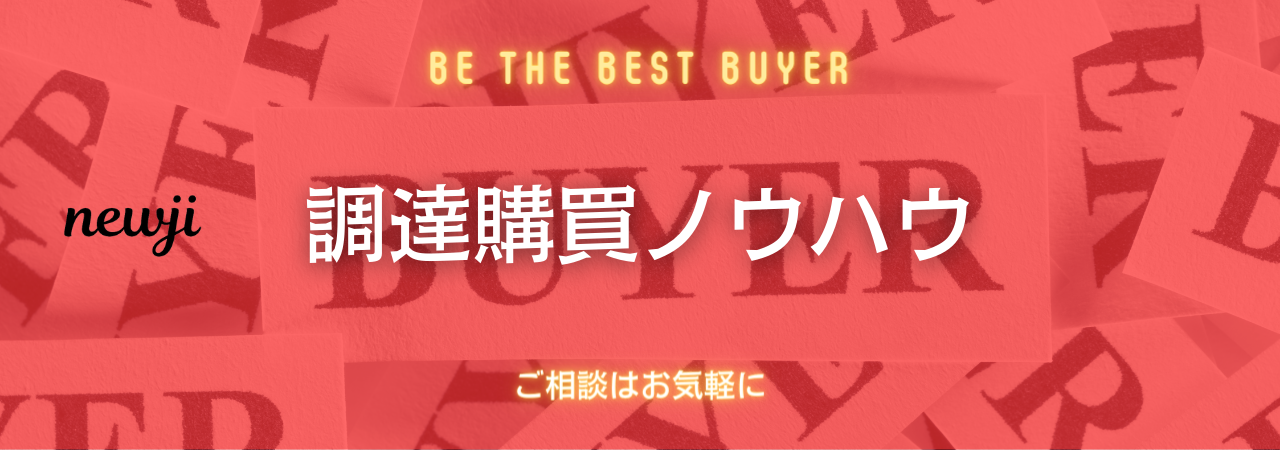
目次
はじめに
トヨタ自動車は長年にわたり、高品質な製品と卓越したプロセス効率で世界をリードしてきた企業です。
その秘訣の一つとして知られるのが、「なぜなぜ分析」です。
これは問題の真因を追及し、トラブルを未然に防ぐための強力なツールとして、製造業界で広く認知されています。
本記事では、トヨタ流「なぜなぜ分析」の基本的な考え方やその実践方法、さらに現場での応用例をご紹介します。
この知識は、製造業に携わる方々やバイヤーを目指す方、サプライヤーとしてバイヤーの考え方を理解したい方々にとって、有益なものであると確信しています。
トヨタ流「なぜなぜ分析」とは
基本的な考え方
「なぜなぜ分析」とは、問題が発生した際にその表面的な原因にとどまらず、真の原因を探り当てる手法です。
この手法は、問題の再発を防ぎ、より根本的な解決策を見いだすことを目的としています。
具体的には、問題が発生した時に「なぜ?」を繰り返し問いかけることによって、真因にたどり着くという思考プロセスです。
一般的に5回「なぜ」を繰り返すことで、表面的な原因から深層の原因に至ると言われています。
なぜ5回なのか?
通常、問題の表層的な原因は一度の「なぜ」で明らかになりますが、その背景には更なる根本的な要因があります。
直感的には1回や2回の「なぜ」で解決できるように思えますが、実際には5回程度の「なぜ」により、複数のレイヤーに隠された問題に深くアプローチすることが可能になります。
このプロセスにより、真因が明らかになり、持続可能な改善策が施せるようになるのです。
なぜなぜ分析のステップ
問題の明確化
「なぜなぜ分析」を行う際の最初のステップは、問題の明確化です。
ここでは、発生した問題やイベントを具体的な事象として記録し、他の問題と混同しないように注意が必要です。
例えば「製品が基準外の寸法である」という問題を表現します。
問題を漠然と「品質が悪い」としてしまうと、何が真因なのかだれも特定することができません。
なぜを繰り返す
1度の「なぜ?」から始め、具体的な原因を追求します。
そして次の「なぜ?」では、その原因がさらにどうして発生したのかを探ることになります。
このプロセスを少なくとも5回繰り返すことで、問題の背景にある本当に重要な原因に到達します。
例えば、「なぜ製品が基準外の寸法になったのか?」という問いに「機械の設定ミス」が答えなら、「なぜ機械の設定をミスしたのか?」と尋ねていく形になります。
根本原因の特定と対応策の策定
真の原因が分かったら、次にすべきはその原因を解決するための具体的な対策を策定することです。
仮に、機械の設定ミスが真因だと特定されたならば、その対策としてオペレーターに対する教育プログラムの充実化や、誤設定を防ぐためのマニュアルの見直し、新たな検証プロセスの導入などが考えられます。
製造業現場での応用事例
製造ラインでの品質不良時の応用
トヨタでは、品質不良が発生した場合に「なぜなぜ分析」をすぐに行います。
例えば、組み立て工程での不良発見時には、その不良がなぜ発生したのか、特定の作業者のミスなのか、機材の故障なのかなど、様々な観点から分析します。
そして、その背景にある深層原因に対して、恒久的な対策を講じることが重要です。
生産設備のダウンタイムの削減
トヨタでは、設備の停止が生産効率を大きく左右します。
そのため、ダウンタイムが発生した際には、その原因を「なぜなぜ分析」により追求します。
例えば、ある機械が故障した際には「なぜ故障したのか?」から始まり、「なぜ必要なメンテナンスが行われなかったのか?」などと掘り下げ、基盤的な管理体制の改善が必要である場合もあります。
「なぜなぜ分析」の効果と限界
効果とその持続性
「なぜなぜ分析」は、単なる問題解決の手段を超え、企業文化として組織内に根付かせることで、大きな効果を持ちます。
なぜなら、問題を解決するだけでなく、再発防止策を考えることで、同じ問題が起こる確率が減少し、結果的にコスト削減や生産性の向上につながります。
限界と注意点
一方で、「なぜなぜ分析」には限界も存在します。
正確な「なぜ」を問うためには、十分なデータと現場に精通したメンバーの参与が求められます。
また、問題の根本原因を特定するだけでなく、実行可能な対策が見つからない場合、分析が無意味になるケースもあり得ます。
そのため、効果的な対策の策定と組織全体での実行力が求められます。
製造業での今後の展開となぜなぜ分析への期待
2023年以降、製造業は急速な自動化やデジタルトランスフォーメーションなどの変革が進んでいます。
その中で「なぜなぜ分析」は、伝統的でありながらも現場での問題解決の基礎法として、今後も重要性を増すと考えられます。
AIやIoTを活用したデータ収集により、より迅速で精度の高い「なぜなぜ分析」が可能になるでしょう。
それにより、問題の発見から解決までのサイクルが短縮され、企業の革新を支える原動力となることが期待されます。
まとめ
本記事では、トヨタ流「なぜなぜ分析」の基本的な考え方とその実践方法、工場現場での活用事例について解説しました。
なぜなぜ分析は、製造業における品質管理のみならず、効率的な生産管理、調達購買の問題解決にも応用可能です。
これを機に、業界全体での継続的改善のための強力なツールとして、この手法を活用してみてはいかがでしょうか。
資料ダウンロード
QCD調達購買管理クラウド「newji」は、調達購買部門で必要なQCD管理全てを備えた、現場特化型兼クラウド型の今世紀最高の購買管理システムとなります。
ユーザー登録
調達購買業務の効率化だけでなく、システムを導入することで、コスト削減や製品・資材のステータス可視化のほか、属人化していた購買情報の共有化による内部不正防止や統制にも役立ちます。
NEWJI DX
製造業に特化したデジタルトランスフォーメーション(DX)の実現を目指す請負開発型のコンサルティングサービスです。AI、iPaaS、および先端の技術を駆使して、製造プロセスの効率化、業務効率化、チームワーク強化、コスト削減、品質向上を実現します。このサービスは、製造業の課題を深く理解し、それに対する最適なデジタルソリューションを提供することで、企業が持続的な成長とイノベーションを達成できるようサポートします。
オンライン講座
製造業、主に購買・調達部門にお勤めの方々に向けた情報を配信しております。
新任の方やベテランの方、管理職を対象とした幅広いコンテンツをご用意しております。
お問い合わせ
コストダウンが利益に直結する術だと理解していても、なかなか前に進めることができない状況。そんな時は、newjiのコストダウン自動化機能で大きく利益貢献しよう!
(Β版非公開)