- お役立ち記事
- Using IoT Technologies to Improve Manufacturing Site Efficiency
Using IoT Technologies to Improve Manufacturing Site Efficiency
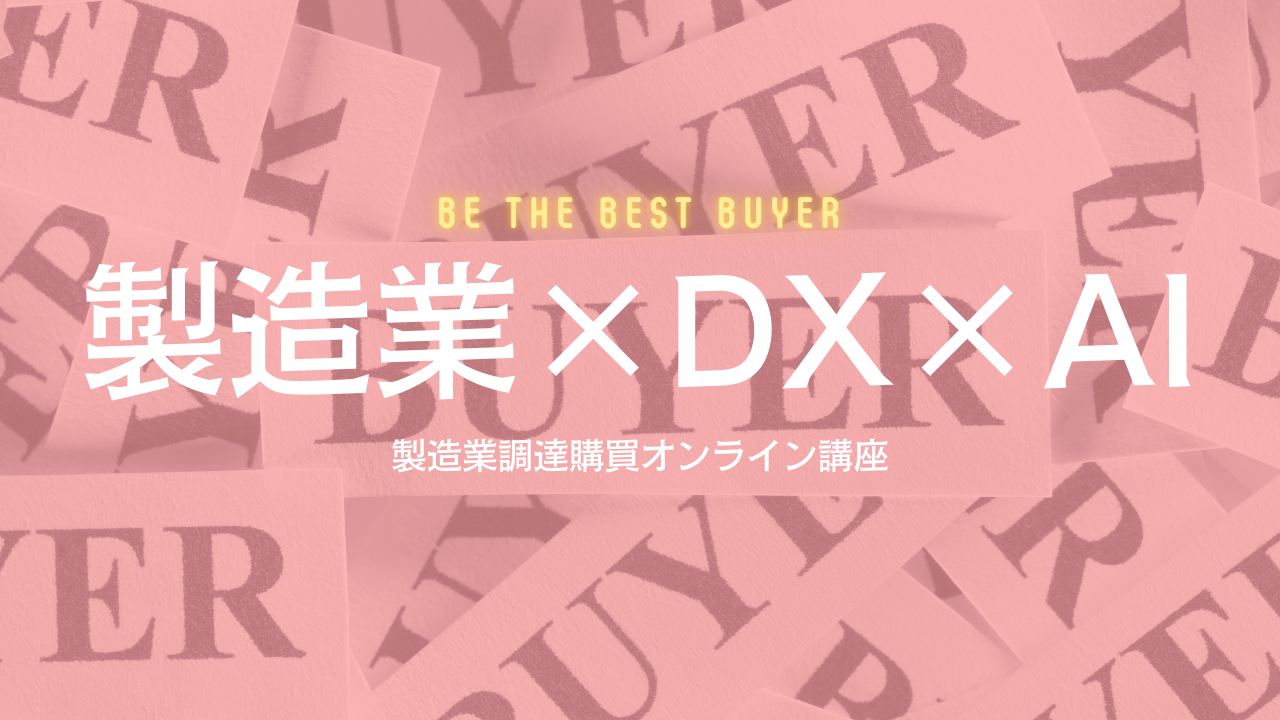
The manufacturing industry is highly competitive with tight margins. Improving efficiency through waste reduction and productivity gains is crucial for success. Fortunately, emerging Internet of Things (IoT) technologies provide opportunities for manufacturers to optimize operations at their sites.
IoT refers to the network of physical objects embedded with sensors, software, and other technologies to connect and exchange data with other devices and systems over the internet. When implemented strategically, IoT solutions can deliver valuable data insights for enhancing various aspects of a manufacturing operation.
Asset Tracking for Increased Uptime
Accurately monitoring the real-time location and usage of assets like machinery, vehicles, tools, and parts across a manufacturing site allows problems to be identified and addressed before major breakdowns occur. Wireless sensors placed on critical assets continuously transmit usage and condition data to the cloud for analysis. If an asset shows abnormal behavior or excessive wear that could lead to downtime, maintenance staff are promptly dispatched to perform repairs or replacements. Early intervention keeps equipment uptime high.
Item-level tracking with technologies like RFID makes it possible to instantly know the precise locations of all work-in-process inventory, raw materials, and finished goods as they move between production areas and warehouses. Not having to search for misplaced items saves time that would otherwise be wasted. Managers also gain greater visibility into internal logistics which enables process bottlenecks to be found and eliminated.
Environmental Monitoring Boosts Product Quality
By installing humidity, temperature, vibration, and other sensors around production floors and in storage facilities, manufacturers gain constant insight into environmental conditions that impact product quality. Deviations from optimal ranges can trigger alerts so adjustments are swiftly made before defects emerge. Precise environmental regulation leads to higher first-pass yields and less rework.
Energy and Resource Optimization Cuts Costs
IoT-enabled smart meters and submeters let energy, water, and raw material usage be analyzed on an equipment- or process-level basis across different time intervals. Consumption anomalies are pinpointed, as are the most wasteful assets or stages of production. This investigative data promotes targeted conservation efforts like maintenance, retrofitting, or process changes with measurable results. Less utility and material waste translates directly to cost savings.
Predictive Maintenance Prevents Breakdowns
When sensors are incorporated into manufacturing machinery to monitor operational parameters, the collected performance data can be applied to predictive maintenance and reliability programs. Statistical algorithms identify subtle signs of impending failures based on parameters like vibration levels, operating temperatures, usage patterns, and more. Maintenance technicians preemptively service equipment before breakdowns occur, minimizing disruptions to production schedules.
Digitization of Paperwork Improves Agility
Manual documentation systems are error-prone and lack the accessibility of digital formats. IoT-enabled smart forms, checklists, work instructions, safety procedures, and asset histories instead reside in the cloud for anytime, anywhere access via mobile devices. Real-time updates ensure everyone always works from the latest information. Digitization also erases paperwork bottlenecks that hinder quick decision making and increases manufacturing agility to respond to disruptions or changes in demand.
Data Analytics Drives Continuous Improvement
The foundation of an effective IoT implementation is extracting useful insights from the massive streams of granular data collected by sensors. Manufacturers employ advanced analytical tools to bring structure and meaning to this sensor data. Techniques like machine learning and artificial intelligence are applied to surface hidden patterns, predict outcomes, and prescribe optimization opportunities previously unseen by humans alone. Regular analysis cycles continuously refine processes and drive incremental gains.
Implementing IoT presents large upfront costs that require careful planning. However, the benefits of increased visibility, predictive capabilities, continuous improvement techniques, and overall operational efficiencies create a compelling case that eventually outweighs expenses when executed strategically. Global IoT spending in manufacturing is expected to grow significantly in coming years as more enterprises harness the power of connected devices and data analytics to achieve new levels of productivity, quality, and competitiveness.
資料ダウンロード
QCD調達購買管理クラウド「newji」は、調達購買部門で必要なQCD管理全てを備えた、現場特化型兼クラウド型の今世紀最高の購買管理システムとなります。
ユーザー登録
調達購買業務の効率化だけでなく、システムを導入することで、コスト削減や製品・資材のステータス可視化のほか、属人化していた購買情報の共有化による内部不正防止や統制にも役立ちます。
NEWJI DX
製造業に特化したデジタルトランスフォーメーション(DX)の実現を目指す請負開発型のコンサルティングサービスです。AI、iPaaS、および先端の技術を駆使して、製造プロセスの効率化、業務効率化、チームワーク強化、コスト削減、品質向上を実現します。このサービスは、製造業の課題を深く理解し、それに対する最適なデジタルソリューションを提供することで、企業が持続的な成長とイノベーションを達成できるようサポートします。
オンライン講座
製造業、主に購買・調達部門にお勤めの方々に向けた情報を配信しております。
新任の方やベテランの方、管理職を対象とした幅広いコンテンツをご用意しております。
お問い合わせ
コストダウンが利益に直結する術だと理解していても、なかなか前に進めることができない状況。そんな時は、newjiのコストダウン自動化機能で大きく利益貢献しよう!
(Β版非公開)