- お役立ち記事
- 製造業の調達購買におけるPDCAサイクル活用術:効率と品質を同時に向上する方法
月間76,176名の
製造業ご担当者様が閲覧しています*
*2025年3月31日現在のGoogle Analyticsのデータより
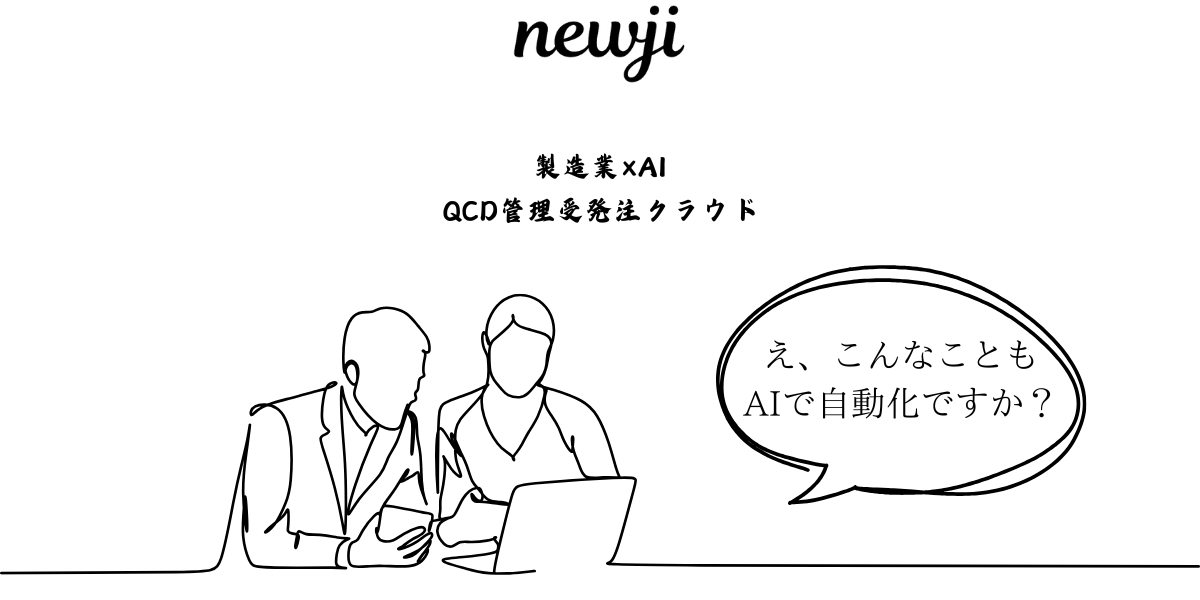
製造業の調達購買におけるPDCAサイクル活用術:効率と品質を同時に向上する方法
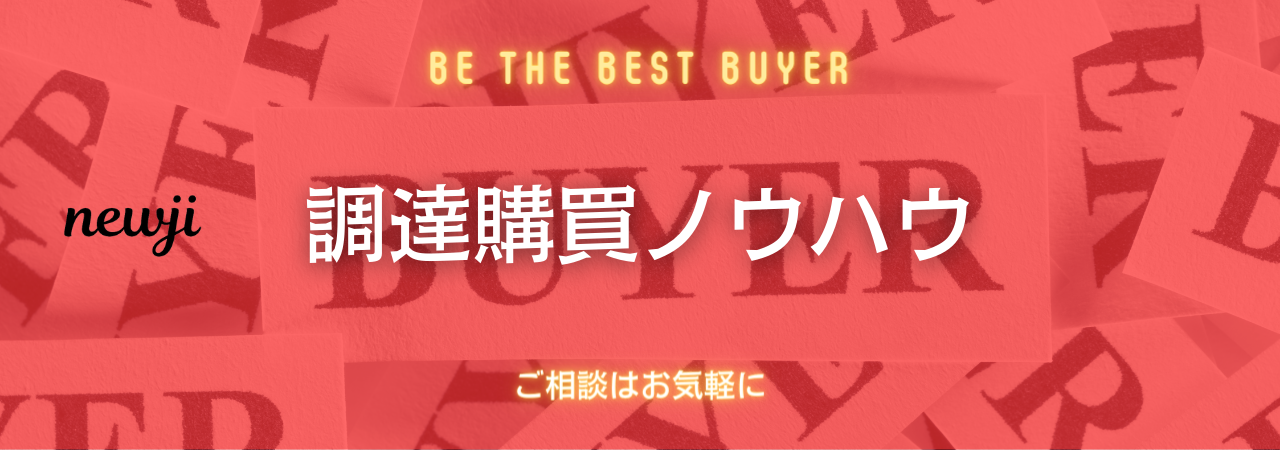
目次
はじめに
製造業における調達購買は、製品の品質や生産効率に直結する重要な業務です。調達購買部門が適切に機能しない場合、コストの増加や納期遅延、品質低下などの問題が発生し、企業全体の競争力に影響を及ぼします。そこで、PDCAサイクルを活用することで、調達購買プロセスの継続的改善を図り、効率と品質の両方を向上させることが可能です。本記事では、製造業の調達購買におけるPDCAサイクルの活用方法とその効果について詳しく解説します。
PDCAサイクルとは
PDCAサイクルは、Plan(計画)、Do(実行)、Check(評価)、Act(改善)の4つのステップから成り立つ継続的改善の手法です。このサイクルを繰り返すことで、業務プロセスの品質向上や効率化を図ることができます。調達購買部門においても、このPDCAサイクルを適用することで、調達活動の最適化が期待できます。
Plan(計画)
計画段階では、現在の調達プロセスの現状分析を行い、改善すべき点や目標を設定します。具体的には、以下の事項を検討します。
– 調達ニーズの明確化
– サプライヤーの選定基準の策定
– コスト削減目標の設定
– 品質要求事項の明確化
Do(実行)
実行段階では、計画で設定した目標に基づいて具体的な調達活動を行います。具体的なアクションとしては、
– サプライヤーと契約の締結
– 購買業務の実施
– サプライヤーとのコミュニケーション
– 調達システムの導入
などが挙げられます。
Check(評価)
評価段階では、実行した調達活動の成果を測定し、目標達成度を確認します。主な評価項目として、
– コスト削減の実現度
– 納期遵守率
– 品質の維持・向上
– サプライヤーのパフォーマンス
などがあります。これらの評価結果をもとに、計画と実績のギャップを分析します。
Act(改善)
改善段階では、評価結果に基づき、調達プロセスの改善策を検討・実施します。具体的な改善策としては、
– サプライヤーの再選定や条件交渉
– 調達手順の見直し
– 従業員の教育・研修の強化
– 調達システムの最適化
などが考えられます。改善策を実行に移した後、再びPDCAサイクルを回すことで、継続的な改善を図ります。
PDCAサイクルの調達購買への適用方法
調達購買部門でPDCAサイクルを効果的に活用するためには、各ステップを具体的に実践することが重要です。以下に、その具体的な方法を紹介します。
1. 計画(Plan)
調達ニーズの明確化が第一歩です。製品の仕様や数量、納期などを正確に把握し、必要な資材やサービスをリストアップします。また、市場調査を行い、適切なサプライヤーの選定基準を策定します。さらに、コスト削減や品質向上といった具体的な目標を設定し、それに向けた戦略を立てます。
2. 実行(Do)
計画に基づき、具体的な調達活動を開始します。サプライヤーとの交渉を行い、最適な条件で契約を締結します。調達システムの導入やプロセスの標準化を図り、効率的な購買業務を実現します。また、サプライヤーとのコミュニケーションを密にし、信頼関係を築くことも重要です。
3. 評価(Check)
調達活動の成果を定期的に評価します。コスト削減の実績や納期遵守率、品質の評価など、設定した目標に対する達成度を測定します。また、サプライヤーのパフォーマンスを評価し、必要に応じて改善措置を講じます。この評価プロセスを通じて、調達プロセスの現状を正確に把握します。
4. 改善(Act)
評価結果をもとに、調達プロセスの改善策を策定・実施します。例えば、コスト削減が不十分な場合は、サプライヤーとの再交渉や新たなサプライヤーの探索を行います。また、品質に問題がある場合は、品質管理プロセスの見直しやサプライヤーの品質改善支援を行います。改善策を実行後、再度PDCAサイクルを回し、継続的な改善を図ります。
PDCAサイクル活用のメリットとデメリット
PDCAサイクルを調達購買に活用することで、多くのメリットがありますが、一方でいくつかのデメリットや課題も存在します。
メリット
- 継続的な改善: PDCAサイクルを繰り返すことで、調達プロセスの継続的な改善が可能です。
- 効率の向上: プロセスの標準化や無駄の排除により、業務の効率化が図れます。
- 品質の向上: 品質管理が強化されることで、調達品の品質が向上します。
- コスト削減: 効率化と品質向上により、総合的なコスト削減が実現します。
- リスク管理: サプライチェーンのリスクを事前に把握し、対応策を講じることが可能です。
デメリット
- 時間とリソースの投入: PDCAサイクルの実施には、時間と人材、資金などのリソースが必要です。
- 継続的な取り組みの必要性: PDCAサイクルは一度実施して終わりではなく、継続的な取り組みが求められます。
- 変化への対応: 市場や技術の変化に迅速に対応するためには、柔軟な改善策が必要です。
- 従業員の理解と協力: PDCAサイクルを効果的に実施するためには、従業員全体の理解と協力が不可欠です。
サプライヤー交渉術とPDCAサイクル
調達購買におけるサプライヤーとの交渉は、PDCAサイクルと密接に関連しています。効果的な交渉術をPDCAサイクルに組み込むことで、より良い調達条件を引き出すことが可能です。
計画段階での交渉準備
交渉を成功させるためには、事前の準備が重要です。市場調査を行い、サプライヤーの強みや弱みを把握します。また、自社のニーズや目標を明確にし、交渉戦略を策定します。競合他社の動向や価格相場も考慮に入れ、最適な交渉ポイントを見極めます。
実行段階での交渉技術
交渉の実行段階では、以下の技術を活用します。
- Win-Winの姿勢: サプライヤーとの長期的な関係を重視し、双方に利益がある合意を目指します。
- 情報の共有: 自社のニーズや制約を正直に伝えることで、サプライヤーとの信頼関係を築きます。
- 柔軟な交渉: 固定的な姿勢ではなく、サプライヤーの意見や提案にも耳を傾け、柔軟に対応します。
- 代替案の準備: 交渉が行き詰まった場合に備え、複数の代替案を準備しておくことが重要です。
評価段階での交渉成果の分析
交渉が終了した後、その成果を評価します。設定した目標が達成されたか、交渉過程での課題や成功点を分析します。この評価をもとに、次回の交渉に向けた改善策を検討します。
改善段階での交渉戦略の見直し
評価結果を基に、交渉戦略を見直します。成功した点を強化し、課題があった点を改善することで、次回以降の交渉の質を向上させます。例えば、交渉前の準備をより徹底する、サプライヤーとのコミュニケーション方法を改善するなどの対策が考えられます。
現在の市況と調達購買への影響
2023年時点での市場環境は、グローバルなサプライチェーンの再編やデジタルトランスフォーメーションの進展など、大きな変化が見られます。これらの変化は、調達購買に以下のような影響を与えています。
サプライチェーンのグローバル化
グローバル化により、サプライチェーンが複雑化しています。複数の国や地域にまたがるサプライヤーとの取引が増える一方で、政治的リスクや物流の障害などが課題となっています。PDCAサイクルを活用して、これらのリスクを管理し、柔軟な調達戦略を構築することが重要です。
デジタルトランスフォーメーションの進展
デジタル技術の進展により、調達購買プロセスの自動化やデータ分析が可能となっています。調達システムやERP(Enterprise Resource Planning)の導入により、データの可視化やリアルタイムなモニタリングが実現します。PDCAサイクルとデジタル技術を組み合わせることで、調達プロセスの効率化と精度向上を図ることができます。
持続可能性とCSRの重要性
環境負荷の低減や社会的責任(CSR)の観点から、持続可能な調達が求められています。サプライヤー選定においても、環境基準や倫理的な基準を重視する企業が増えています。PDCAサイクルを通じて、持続可能な調達基準を設定し、サプライヤーとの協力関係を構築することが重要です。
PDCAサイクルを活用した成功事例
実際にPDCAサイクルを活用して調達購買プロセスを改善し、成功を収めた企業の事例を紹介します。
事例1: 大手自動車メーカーの調達改革
ある大手自動車メーカーでは、調達購買プロセスの効率化とコスト削減を目指してPDCAサイクルを導入しました。まず、調達ニーズの詳細な分析を行い、サプライヤーのパフォーマンス評価基準を策定しました。実行段階では、調達システムの導入やサプライヤーとの積極的なコミュニケーションを実施。評価段階では、コスト削減率や納期遵守率の向上を確認し、改善段階では、さらなるサプライヤーの最適化やプロセスの自動化を進めました。その結果、調達コストが15%削減され、納期遵守率が95%以上に向上しました。
事例2: 電子機器メーカーの品質管理強化
ある電子機器メーカーでは、調達購買における品質問題を解決するためにPDCAサイクルを導入しました。計画段階では、品質管理基準の見直しとサプライヤーの品質評価基準の策定を行いました。実行段階では、サプライヤーに対する品質教育や監査を実施し、品質データの収集を強化。評価段階では、製品不良率の低下やサプライヤーの品質改善状況を評価し、改善段階では、問題が発生したサプライヤーへの改善指導や新たな品質管理ツールの導入を行いました。これにより、製品の品質が大幅に向上し、顧客満足度も向上しました。
事例3: 食品メーカーのサプライチェーン最適化
ある食品メーカーでは、サプライチェーン全体の最適化を目指してPDCAサイクルを導入しました。計画段階では、調達プロセスの現状分析と改善目標の設定を行いました。実行段階では、調達システムの導入とサプライヤーとの協力体制の強化を図りました。評価段階では、物流コストの削減や在庫管理の精度向上を測定し、改善段階では、在庫管理システムのさらなる最適化やサプライヤーとのデータ共有を進めました。その結果、物流コストが20%削減され、在庫回転率が向上しました。
PDCAサイクルを成功させるためのポイント
PDCAサイクルを効果的に活用するためには、以下のポイントを押さえることが重要です。
1. 明確な目標設定
PDCAサイクルを回す際には、明確で具体的な目標を設定することが不可欠です。目標が明確であれば、各ステップでの活動が一貫性を持ち、効果的な改善が可能となります。
2. データの活用
調達購買プロセスの改善には、正確なデータが欠かせません。データを収集・分析し、現状を正確に把握することで、適切な改善策を講じることができます。デジタルツールやERPシステムの導入を検討しましょう。
3. チームの協力
PDCAサイクルは一部の担当者だけでなく、調達購買チーム全体で取り組むことが重要です。チーム内での情報共有やコミュニケーションを促進し、全員が改善に向けて協力する体制を整えましょう。
4. 柔軟な対応
市場環境やサプライチェーンの状況は常に変化します。PDCAサイクルを回す際には、柔軟に対応できる姿勢が求められます。必要に応じて計画や改善策を見直し、迅速に対応することが重要です。
5. 継続的な学習と改善
PDCAサイクルは一度実施して終わりではありません。継続的にサイクルを回し、学習と改善を繰り返すことで、調達購買プロセスの品質と効率を持続的に向上させることができます。
まとめ
製造業の調達購買においてPDCAサイクルを活用することで、プロセスの継続的な改善が可能となり、効率と品質の両方を向上させることができます。計画から改善までの各ステップを確実に実行し、サプライヤーとの良好な関係を築くことで、調達活動の成果を最大化することができます。さらに、現在の市場環境に適応し、デジタルトランスフォーメーションや持続可能な調達を推進することで、企業全体の競争力を強化することが可能です。PDCAサイクルを効果的に導入し、調達購買部門の発展に寄与しましょう。
資料ダウンロード
QCD管理受発注クラウド「newji」は、受発注部門で必要なQCD管理全てを備えた、現場特化型兼クラウド型の今世紀最高の受発注管理システムとなります。
ユーザー登録
受発注業務の効率化だけでなく、システムを導入することで、コスト削減や製品・資材のステータス可視化のほか、属人化していた受発注情報の共有化による内部不正防止や統制にも役立ちます。
NEWJI DX
製造業に特化したデジタルトランスフォーメーション(DX)の実現を目指す請負開発型のコンサルティングサービスです。AI、iPaaS、および先端の技術を駆使して、製造プロセスの効率化、業務効率化、チームワーク強化、コスト削減、品質向上を実現します。このサービスは、製造業の課題を深く理解し、それに対する最適なデジタルソリューションを提供することで、企業が持続的な成長とイノベーションを達成できるようサポートします。
製造業ニュース解説
製造業、主に購買・調達部門にお勤めの方々に向けた情報を配信しております。
新任の方やベテランの方、管理職を対象とした幅広いコンテンツをご用意しております。
お問い合わせ
コストダウンが利益に直結する術だと理解していても、なかなか前に進めることができない状況。そんな時は、newjiのコストダウン自動化機能で大きく利益貢献しよう!
(β版非公開)