- お役立ち記事
- Implementing a Risk-Based Approach in Manufacturing Quality Management: Introduction and Effects
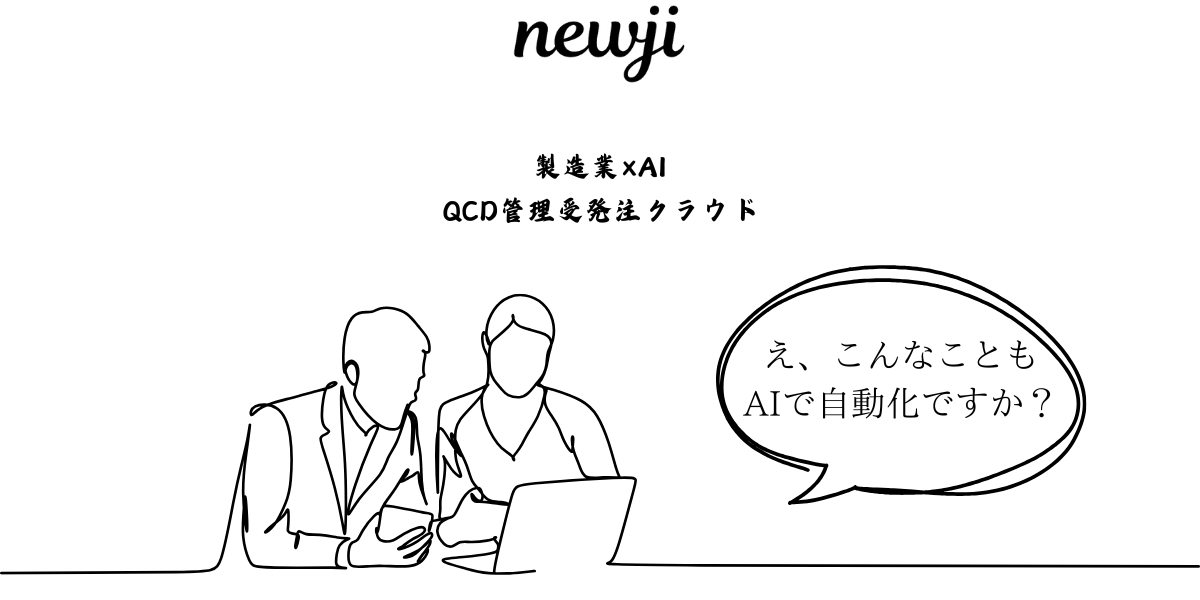
Implementing a Risk-Based Approach in Manufacturing Quality Management: Introduction and Effects
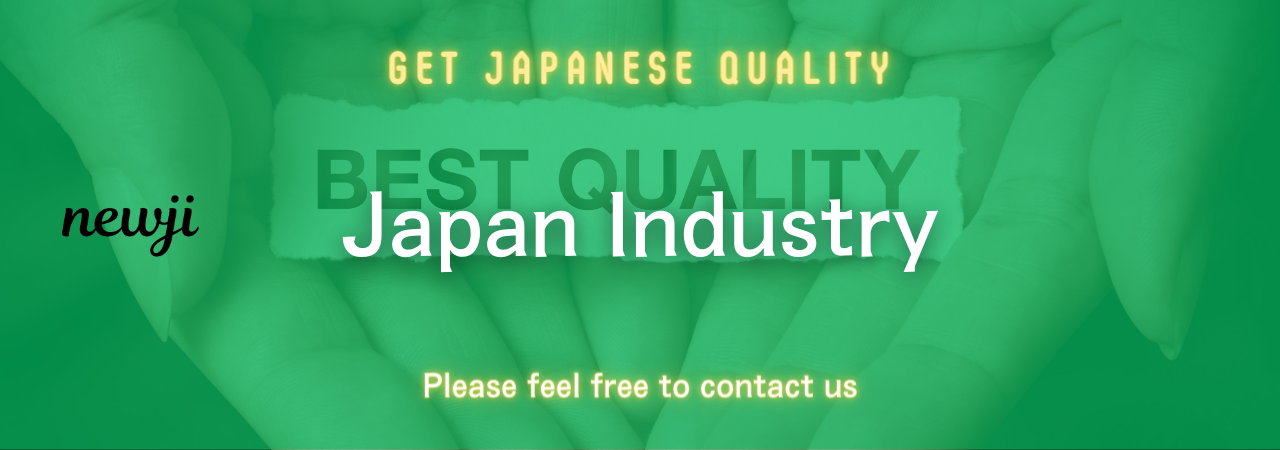
In the fast-paced world of manufacturing, ensuring high-quality outcomes while maintaining safety and efficiency is crucial.
One powerful strategy to achieve this is by implementing a risk-based approach in quality management.
This method involves identifying, assessing, and mitigating potential risks that may affect product quality and manufacturing processes.
目次
Understanding a Risk-Based Approach
A risk-based approach emphasizes the importance of evaluating potential threats and their impacts before they become problematic.
Instead of relying solely on traditional quality control measures, this strategy integrates risk management principles into the quality management system (QMS).
It aims to anticipate issues proactively and create a culture of continuous improvement.
Identifying Risks
The first step in this approach is identifying potential risks throughout the manufacturing process.
These risks can originate from various sources, including equipment malfunctions, human errors, raw material inconsistencies, or external factors like supply chain disruptions.
By thoroughly analyzing each stage of production, manufacturers can pinpoint areas where these risks are most likely to occur.
Assessing Risks
Once risks have been identified, the next step is to assess their potential impact and likelihood.
This involves evaluating the severity of the consequences and the probability of the risk happening.
Tools like Failure Modes and Effects Analysis (FMEA) and risk matrices can be instrumental in this process.
With a clear understanding of the risks, manufacturers can prioritize them based on their significance and address the most critical ones first.
Integrating Risk Management into QMS
Integrating risk management into the quality management system is essential for a seamless implementation.
This involves adopting a structured framework that aligns with international standards such as ISO 9001, which emphasizes risk-based thinking.
Instituting formal procedures and documentation to track and manage risks is also necessary.
Establishing Risk Control Measures
Effective risk management requires establishing control measures to mitigate identified risks.
These measures can include additional inspections, preventive maintenance, employee training, or more stringent supplier evaluations.
It’s essential to develop a comprehensive risk control plan that outlines specific actions to be taken to prevent or minimize the impact of each risk.
Monitoring and Reviewing Risks
Risk management is an ongoing process that requires continuous monitoring and reviewing.
Regularly updating risk assessments and control measures ensures that they remain effective and relevant.
This also involves collecting data from production processes, customer feedback, and audit results to identify new risks or reevaluate existing ones.
Benefits of Implementing a Risk-Based Approach
Adopting a risk-based approach in manufacturing quality management offers numerous advantages.
Enhanced Product Quality
By proactively addressing potential issues, manufacturers can significantly enhance the overall quality of their products.
The early detection and mitigation of risks help prevent defects and ensure that the final products meet the desired specifications and standards.
Increased Operational Efficiency
Risk management allows for streamlined processes and reduces the likelihood of disruptions.
This leads to improved operational efficiency as potential bottlenecks or delays are anticipated and addressed beforehand.
It also enables manufacturers to optimize resource allocation and minimize waste.
Cost Savings
Preventing quality issues before they escalate helps avoid costly recalls, rework, and scrap.
Investing in risk management may incur some initial costs, but the long-term savings from reduced quality-related expenses can be substantial.
Moreover, it helps build a positive reputation and maintains customer trust.
Compliance with Regulations
Many industries have stringent regulatory requirements regarding product safety and quality.
Implementing a risk-based approach ensures that manufacturers comply with these regulations.
This minimizes the risk of legal issues, fines, and market withdrawals due to non-compliance.
Improved Decision-Making
A risk-based approach provides a structured framework for decision-making based on data and analysis.
It helps stakeholders make informed choices by highlighting potential risks and their implications.
This leads to more strategic planning and better preparation for future challenges.
Enhanced Customer Satisfaction
Customers are more likely to trust and remain loyal to manufacturers that consistently deliver high-quality products.
By implementing a risk-based approach, manufacturers can ensure that customer expectations are met or exceeded.
This fosters a positive customer experience and boosts satisfaction.
Challenges in Implementing a Risk-Based Approach
Despite its benefits, implementing a risk-based approach in manufacturing quality management is not without challenges.
Resistance to Change
One of the primary challenges is resistance to change within the organization.
Employees and management may be accustomed to traditional quality control methods and may be hesitant to adopt a new approach.
Addressing this requires effective communication and training to demonstrate the benefits and necessity of risk-based thinking.
Resource Allocation
Implementing a risk-based approach requires allocating resources for risk assessment, control measures, and continuous monitoring.
This may involve additional time, personnel, and financial investment.
Proper planning and budgeting are essential to ensure a smooth transition without overburdening the organization.
Complexity of Processes
Manufacturing processes can be complex, with numerous variables and interdependencies.
Identifying and assessing risks in such environments can be challenging.
It’s essential to have a systematic approach and leverage technology and tools to manage this complexity effectively.
Maintaining Consistency
Maintaining consistency in risk management practices across different departments and production lines is crucial.
This requires establishing standardized procedures and ensuring that all employees are on the same page.
Regular training and audits can help uphold consistency and adherence to the risk management framework.
Conclusion
Implementing a risk-based approach in manufacturing quality management is a proactive strategy that offers substantial benefits.
By identifying, assessing, and mitigating risks, manufacturers can enhance product quality, improve operational efficiency, and achieve cost savings.
However, overcoming challenges like resistance to change and resource allocation is crucial for successful implementation.
With a well-structured risk management framework and a commitment to continuous improvement, manufacturers can build a resilient and high-performing quality management system.
資料ダウンロード
QCD調達購買管理クラウド「newji」は、調達購買部門で必要なQCD管理全てを備えた、現場特化型兼クラウド型の今世紀最高の購買管理システムとなります。
ユーザー登録
調達購買業務の効率化だけでなく、システムを導入することで、コスト削減や製品・資材のステータス可視化のほか、属人化していた購買情報の共有化による内部不正防止や統制にも役立ちます。
NEWJI DX
製造業に特化したデジタルトランスフォーメーション(DX)の実現を目指す請負開発型のコンサルティングサービスです。AI、iPaaS、および先端の技術を駆使して、製造プロセスの効率化、業務効率化、チームワーク強化、コスト削減、品質向上を実現します。このサービスは、製造業の課題を深く理解し、それに対する最適なデジタルソリューションを提供することで、企業が持続的な成長とイノベーションを達成できるようサポートします。
オンライン講座
製造業、主に購買・調達部門にお勤めの方々に向けた情報を配信しております。
新任の方やベテランの方、管理職を対象とした幅広いコンテンツをご用意しております。
お問い合わせ
コストダウンが利益に直結する術だと理解していても、なかなか前に進めることができない状況。そんな時は、newjiのコストダウン自動化機能で大きく利益貢献しよう!
(Β版非公開)