- お役立ち記事
- Raw material management by procurement and purchasing departments to reduce processing defect rates in the manufacturing industry
Raw material management by procurement and purchasing departments to reduce processing defect rates in the manufacturing industry
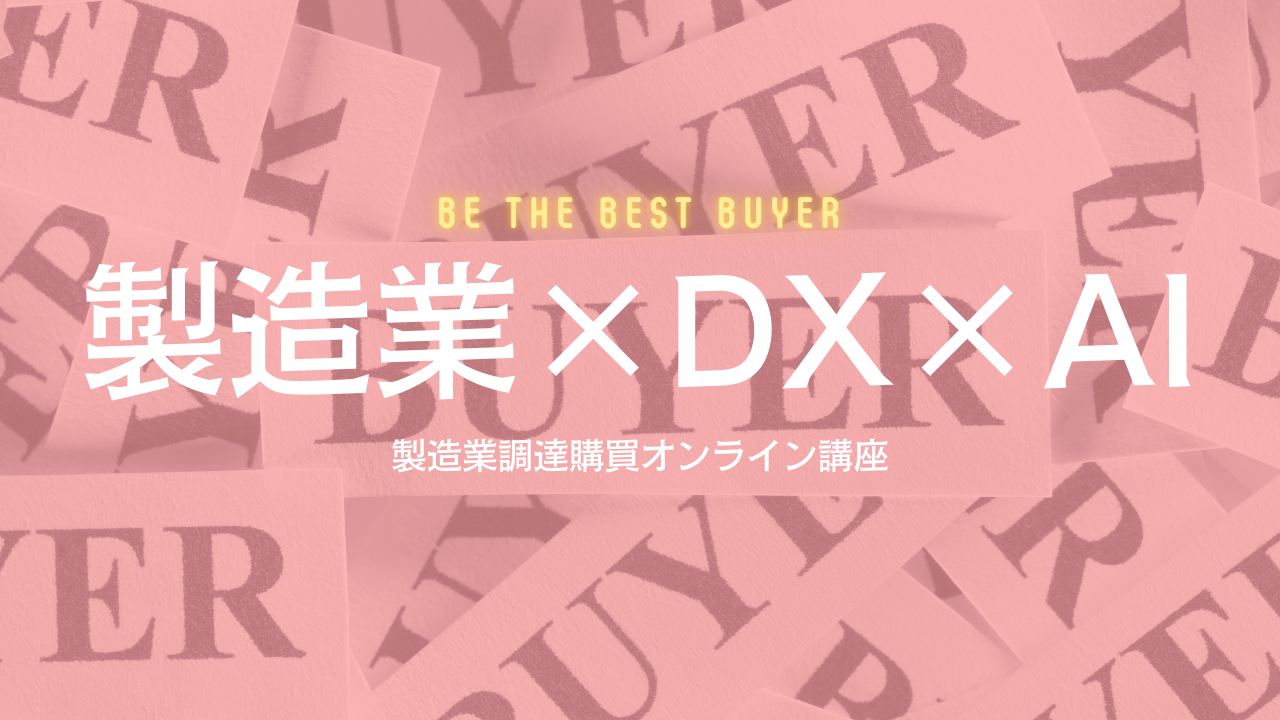
The procurement and purchasing departments play a critical role in effectively managing raw materials that serve as the foundational inputs for manufacturing processes. By closely monitoring the selection, quality control, and logistics of raw material suppliers, these teams can help minimize processing defects downstream on the production floor. Let’s explore some of the key raw material management strategies that these teams employ to reduce defect rates.
Performing due diligence on suppliers is paramount. Procurement professionals conduct extensive research into potential vendors to evaluate their track records, certifications, safety practices, and more. On-site audits provide valuable insights into the suppliers’ operations so issues and risks are identified proactively. Maintaining an approved supplier list with recurrent evaluations ensures raw materials are consistently sourced from partners committed to quality.
Negotiating favorable terms and prices is also crucial, but must avoid compromising on quality standards. Procurement aims to secure the best value for their organization, whether through competitive bidding processes, volume discounts, or long-term agreements. However, the lowest bid does not automatically equal the highest quality if other factors are sacrificed. A balanced approach balances costs with sustained access to compliant raw materials meeting technical specifications.
Closely monitoring raw material quality is imperative once suppliers are selected and production is underway. Random inspections, certifications, and test samples help procurement identify potential quality issues that could arise. State-of-the-art lab equipment and trained technicians rigorously analyze chemical compositions, physical properties, contaminants, and more to catch defects at the source before they impact operations. Statistical process controls may also be applied to batch acceptance.
Implementing robust packaging, labeling, and chain of custody procedures preserves raw material integrity from supplier to production line. Improper packaging could lead to damage or exposure during transportation, while unclear or missing labeling introduces the risk of incorrect materials being used in manufacturing. Traceability tools like barcodes empower quality assurance by confirming the source and attributes of incoming materials.
Forecasting demand accurately and maintaining optimal inventory levels prevents raw material shortages or surpluses that introduce risk. Lack of a needed input could halt a line, while excess materials tie up working capital unnecessarily. Procurement works closely with planning teams to match supply to the production schedule through replenishment techniques like just-in-time and kanban pull systems. Safety stocks also provide a buffer against disruptions.
Developing alternative suppliers broadens supply security. Single sourcing poses problems if that one partner faces production issues or natural disasters interrupt operations. Maintaining potential backups qualified to the same standards as primary suppliers ensures a degree of redundancy in the supply base. Alternative sourcing may also relieve capacity constraints or enable competitive negotiations by playing potential partners against each other.
Facilitating smooth logistics from initial order to delivery completion is a must. Procurement handles inbound transportation efficiently and cost-effectively, usually assuming responsibility for freight to the factory door. Well-coordinated shipping schedules avoid bottlenecks and ensure raw materials arrive precisely as needed to maintain production flow. Emergencies like delays or damaged goods are addressed swiftly through alternate routing or premium shipping as needed.
Implementing continuous improvement initiatives advances raw material management over time. New technologies may boost inspection accuracy, digitization may streamline documentation, and advanced analytics could surface supply chain optimization opportunities. Process reviews identify areas where quality can be tightened further as well as cost savings that don’t compromise standards. When both productivity and compliance are priorities, procurement plays a leading role in empowering sustainable success.
In summary, diligent raw material management from procurement and purchasing safeguards manufacturing operations from the very start. By tightly governing supplier selection, incoming quality controls, inventory practices and logistics, these upstream functions are a linchpin for minimizing defects caused by improper inputs. Their comprehensive strategic oversight helps manufacturing convert raw materials into finished goods as seamlessly as possible.
資料ダウンロード
QCD調達購買管理クラウド「newji」は、調達購買部門で必要なQCD管理全てを備えた、現場特化型兼クラウド型の今世紀最高の購買管理システムとなります。
ユーザー登録
調達購買業務の効率化だけでなく、システムを導入することで、コスト削減や製品・資材のステータス可視化のほか、属人化していた購買情報の共有化による内部不正防止や統制にも役立ちます。
NEWJI DX
製造業に特化したデジタルトランスフォーメーション(DX)の実現を目指す請負開発型のコンサルティングサービスです。AI、iPaaS、および先端の技術を駆使して、製造プロセスの効率化、業務効率化、チームワーク強化、コスト削減、品質向上を実現します。このサービスは、製造業の課題を深く理解し、それに対する最適なデジタルソリューションを提供することで、企業が持続的な成長とイノベーションを達成できるようサポートします。
オンライン講座
製造業、主に購買・調達部門にお勤めの方々に向けた情報を配信しております。
新任の方やベテランの方、管理職を対象とした幅広いコンテンツをご用意しております。
お問い合わせ
コストダウンが利益に直結する術だと理解していても、なかなか前に進めることができない状況。そんな時は、newjiのコストダウン自動化機能で大きく利益貢献しよう!
(Β版非公開)