- お役立ち記事
- “Revolutionizing Efficiency: The Secrets of Japanese Production Management Systems”
“Revolutionizing Efficiency: The Secrets of Japanese Production Management Systems”
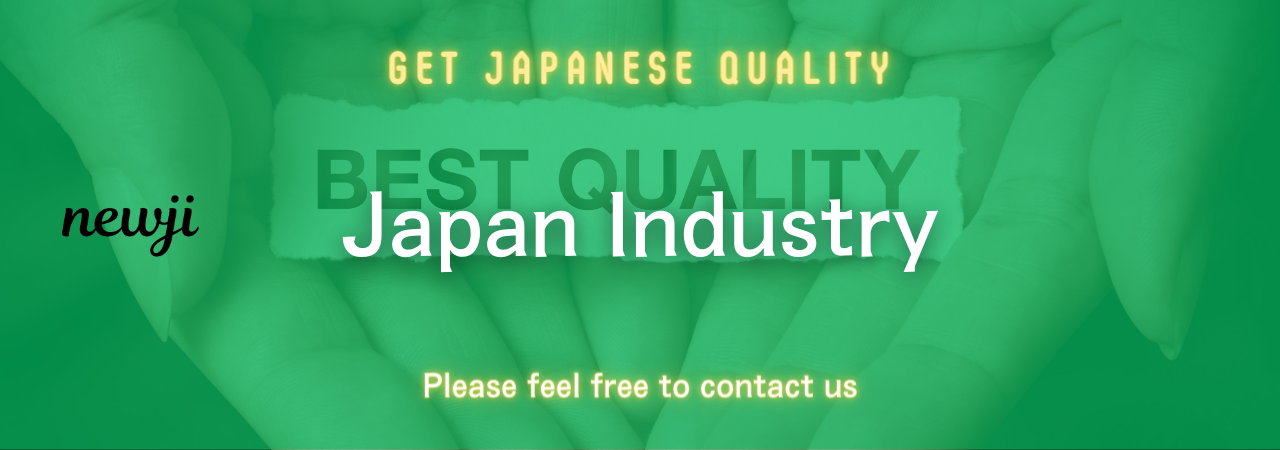
目次
Understanding Japanese Production Management Systems
Japanese production management systems have long been hailed as some of the most efficient and effective in the world. Known for their meticulous attention to detail, precision, and continuous improvement, these systems have set a benchmark in the manufacturing industry. Understanding these management methodologies involves delving into concepts like Just-In-Time (JIT), Kaizen, Poka-Yoke, and 5S – each contributing to a streamlined, efficient production environment.
Key Concepts in Japanese Production Management
Just-In-Time (JIT)
Just-In-Time production is a strategy that aims to reduce flow times within production systems, as well as response times from suppliers and to customers. It is a methodology driven by demand signals, ensuring that manufacturing processes produce only what is needed, when it is needed, and in the amount needed. This minimizes waste, reduces inventory costs, and enhances efficiency.
Kaizen
Kaizen, which translates to “continuous improvement,” is not a one-time strategy but a continuous one. It involves all employees, from the top management to the shop floor workers, in an effort to improve productivity, eliminate waste, and enhance quality through incremental changes. Regular Kaizen events provide opportunities for teams to tackle inefficiencies and innovate better working methods.
Poka-Yoke
Poka-Yoke, or “mistake-proofing,” is a technique designed to prevent errors by designing systems that make it almost impossible to make mistakes. This can involve anything from simple devices that alert operators of an error to sophisticated automated systems. The objective is to eliminate defects through prevention and facilitate quality control.
5S Methodology
The 5S methodology revolves around five Japanese words that stand for sort, set in order, shine, standardize, and sustain. This systematic approach is employed to organize the workplace, ensuring it is clean, efficient, and well-structured. A well-implemented 5S system reduces waste, enhances productivity, and contributes to a safer work environment.
Advantages of Japanese Production Management Systems
Enhanced Efficiency
One of the most significant benefits of Japanese production management systems is enhanced efficiency. By eliminating waste through methodologies like JIT and Kaizen, production processes become leaner and more streamlined.
Improved Quality Control
Quality control is integral to Japanese production management systems. Techniques like Poka-Yoke ensure that potential errors are mitigated, significantly improving the overall quality of the products.
Flexibility and Responsiveness
These systems are highly adaptable, allowing manufacturers to respond swiftly to market changes and customer demands. The flexibility offered by methods such as JIT can lead to better customer satisfaction and a stronger competitive position in the market.
Cost Reduction
By reducing waste and optimizing resource usage, Japanese production management systems contribute to significant cost savings. Lower inventory levels, minimized defects, and efficient operations collectively lead to a more cost-effective production process.
Challenges and Disadvantages
Initial Implementation Costs
Implementing Japanese production management systems often requires a substantial initial investment. This includes costs associated with training, restructuring, and sometimes, upgrading equipment.
Employee Resistance
Employees may resist changes, especially if they are accustomed to traditional methods. Overcoming this resistance requires effective communication, training, and sometimes, a cultural shift within the organization.
High Dependency on Suppliers
Systems like JIT make manufacturers heavily reliant on their suppliers. Any disruption in the supplier’s operations can cause significant issues within the production process.
Continuous Vigilance
Maintaining the benefits of these systems requires continuous monitoring and improvement. It demands a sustained commitment from all employees and the organization as a whole.
Supplier Negotiation Techniques
Effective negotiation with suppliers is crucial for the success of Japanese production management systems. Here are some techniques:
Building Strong Relationships
Japanese business culture places a high value on relationships. Building strong, long-term relationships based on trust and mutual benefit can lead to better deals and more reliable supply chains.
Transparent Communication
Clear, open communication with suppliers ensures that expectations are aligned. Regular meetings and updates can prevent misunderstandings and foster a collaborative approach to problem-solving.
Understanding Supplier Capabilities
Knowing the strengths and limitations of your suppliers is essential. This allows you to work with them to optimize processes, improve quality, and ensure timely deliveries.
Leveraging Data and Analytics
Using data and analytics in negotiations can provide insights into supplier performance, market conditions, and pricing trends, allowing for more informed decision-making.
Current Market Conditions and Trends
Embracing Industry 4.0
The adoption of Industry 4.0 technologies is revolutionizing production management. Integrating IoT, AI, and automation can further enhance the efficiency and responsiveness of production processes in line with Japanese principles.
Sustainability Focus
Sustainability is increasingly becoming a priority in the manufacturing industry. Japanese production management systems, with their emphasis on waste reduction and resource optimization, align well with sustainable manufacturing practices.
Global Supply Chain Challenges
Recent global events have highlighted vulnerabilities in supply chains. Adopting flexible and resilient production management systems is essential to navigate these challenges.
Best Practices in Production Management
Regular Training and Development
Continuously training and developing employees ensures that they are up-to-date with the latest best practices and technologies, fostering a culture of continuous improvement.
Employee Involvement
Involving employees at all levels in decision-making processes and improvement initiatives encourages ownership and accountability, leading to better outcomes.
Consistent Process Audits
Regular audits of production processes help identify areas for improvement and ensure that standards are consistently met.
Leveraging Technology
Embracing new technologies and integrating them into production processes can significantly enhance efficiency, quality, and flexibility.
Conclusion
Japanese production management systems offer a robust framework for achieving unparalleled efficiency and quality in manufacturing. While there are challenges, the long-term benefits of implementing these methodologies far outweigh the initial hurdles. By understanding and adopting key concepts such as JIT, Kaizen, Poka-Yoke, and 5S, and integrating them with modern technologies and best practices, manufacturers can revolutionize their production processes, leading to significant improvements in performance, cost savings, and customer satisfaction.
The journey of implementing Japanese production management systems is ongoing and requires a sustained commitment to continuous improvement and innovation. By embracing these principles, manufacturers can stay competitive in an ever-evolving market and achieve lasting success.
資料ダウンロード
QCD調達購買管理クラウド「newji」は、調達購買部門で必要なQCD管理全てを備えた、現場特化型兼クラウド型の今世紀最高の購買管理システムとなります。
ユーザー登録
調達購買業務の効率化だけでなく、システムを導入することで、コスト削減や製品・資材のステータス可視化のほか、属人化していた購買情報の共有化による内部不正防止や統制にも役立ちます。
NEWJI DX
製造業に特化したデジタルトランスフォーメーション(DX)の実現を目指す請負開発型のコンサルティングサービスです。AI、iPaaS、および先端の技術を駆使して、製造プロセスの効率化、業務効率化、チームワーク強化、コスト削減、品質向上を実現します。このサービスは、製造業の課題を深く理解し、それに対する最適なデジタルソリューションを提供することで、企業が持続的な成長とイノベーションを達成できるようサポートします。
オンライン講座
製造業、主に購買・調達部門にお勤めの方々に向けた情報を配信しております。
新任の方やベテランの方、管理職を対象とした幅広いコンテンツをご用意しております。
お問い合わせ
コストダウンが利益に直結する術だと理解していても、なかなか前に進めることができない状況。そんな時は、newjiのコストダウン自動化機能で大きく利益貢献しよう!
(Β版非公開)