- お役立ち記事
- How Japanese Manufacturing Excellence Sets the Global Technical Standard: A Deep Dive
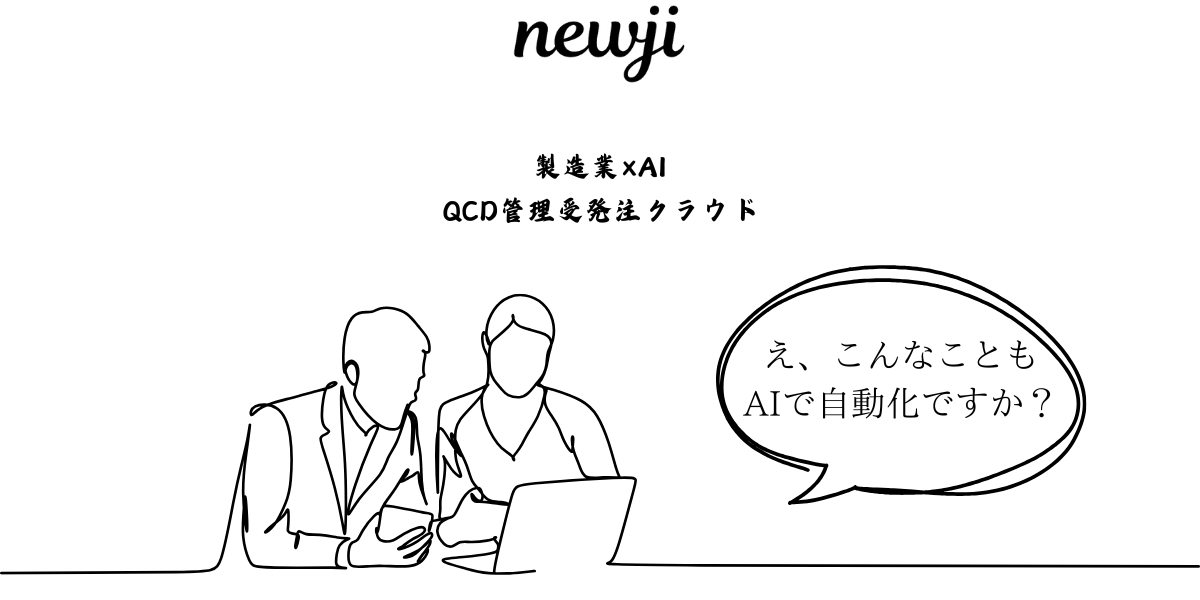
How Japanese Manufacturing Excellence Sets the Global Technical Standard: A Deep Dive
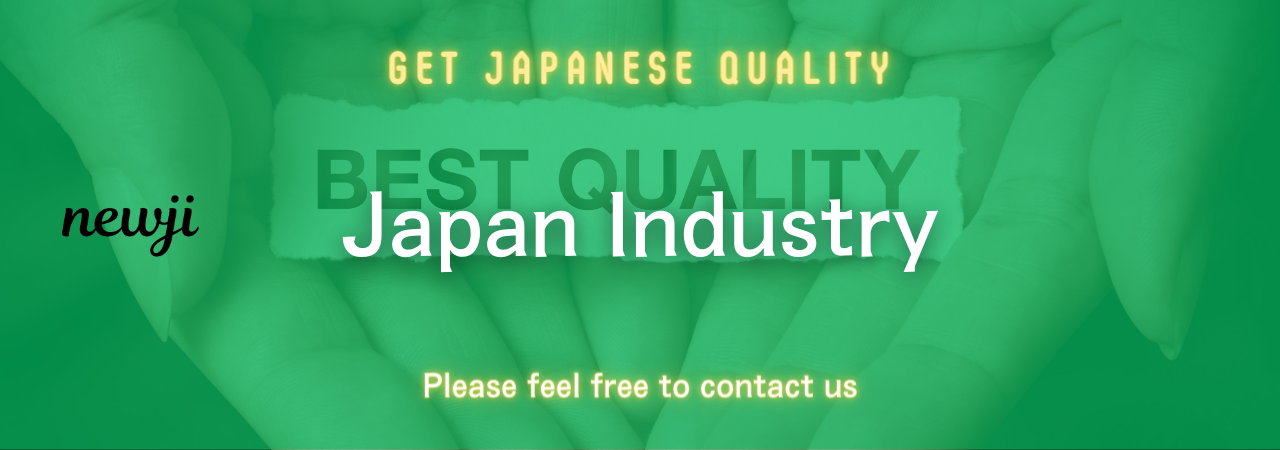
目次
Introduction to Japanese Manufacturing Excellence
Japanese manufacturing has long been regarded as a global benchmark for precision, efficiency, and innovation.
This reputation stems from decades of cultivating unique practices and philosophies that prioritize quality and lean operations.
Japanese companies like Toyota, Sony, and Panasonic have not only captured significant market shares but have also influenced global production and supply chain methodologies.
Their focus on continuous improvement, known as “Kaizen,” alongside a strong culture of respect for skilled artisans, or “Takumi,” has set them apart.
In this article, we delve into the intricacies of Japanese manufacturing, exploring the strengths and potential challenges they face, as well as their impact on global technical standards.
Understanding Japanese Procurement and Purchasing Practices
At the core of Japanese manufacturing excellence lies their robust procurement and purchasing practices.
Notably, they prioritize long-term relationships with suppliers.
This differs from many Western approaches that often emphasize cost savings by frequently switching suppliers.
Advantages of Japanese Procurement Strategies
1. **Reliability and Quality**: Japanese suppliers focus deeply on quality control and precision.
By fostering trustworthy supplier relationships, manufacturing companies can ensure consistent quality over time.
This reliability allows for less stringent checks, reducing administrative and operational burdens.
2. **Technological Advancement**: Many suppliers in Japan invest significantly in advanced technology and innovation.
They often work closely with manufacturers to co-develop new products and processes, turning Japanese manufacturing industries into hotbeds of technological innovation.
3. **Cultural Cohesion**: Sharing cultural values such as dedication to craftsmanship promotes a higher understanding and smoother operational flow between manufacturers and suppliers.
Cultural alignment also ensures both parties uphold the same standards of quality and commitment, furthering mutual goals.
Challenges and Disadvantages
1. **Cost Implications**: The dedication to quality, while invaluable, can sometimes lead to higher costs.
Suppliers might invest in state-of-the-art machinery and skilled labor, raising procurement prices.
2. **Inflexibility**: Long-term relationships, while valuable, might sometimes result in less flexibility for manufacturing companies.
Switching suppliers could be fraught with contractual and cultural complexities, which may pose challenges in dynamic market conditions.
3. **Cultural Barriers**: For international companies, understanding and navigating Japanese business etiquette and practices might be challenging.
Non-Japanese companies may find it tough to adapt to the nuances associated with relationship building and negotiation tactics in Japan.
Effective Supplier Negotiation Techniques with Japanese Firms
Japanese negotiation tactics can differ markedly from Western practices.
To successfully engage with Japanese suppliers, consider the following strategies:
Building Trust
Japanese business culture places great emphasis on trust and respect.
Rushing through negotiations or placing undue emphasis on price without establishing a relationship can be counterproductive.
Invest time in building rapport before delving into contract specifics.
Regular face-to-face meetings, patience, and understanding their viewpoint will benefit long-term relationships.
Adopting a Long-term Perspective
Japanese firms prioritize stability and continuity over short-term gains.
When negotiating contracts, focus on long-term objectives and potential for collaboration rather than quick wins.
Highlighting how the partnership can evolve and contribute to mutual benefits over time can resonate well with Japanese suppliers.
Aligning with Quality Standards
Japanese suppliers value quality immensely.
When negotiating, emphasize the high standards of quality you seek to maintain and how their expertise aligns with your company’s goals.
Being clear on quality expectations, while also showing appreciation for their craftsmanship, can help bridge negotiations smoothly.
Market Conditions Impacting Japanese Manufacturing
Japan’s manufacturing sector doesn’t exist in a vacuum.
Global market conditions and domestic challenges continuously influence its trajectory.
Technological Advancements
Japan has been at the forefront of technological advancements, particularly in robotics and automation.
Their robust R&D investments continue to spearhead innovations, adapting to evolving demands in sectors like electronics, automotive, and health tech.
These advancements ensure that Japanese manufacturers remain competitive globally.
They also set the technical standards that many aspire to meet.
Global Supply Chain Disruptions
Recent global challenges, such as the COVID-19 pandemic and ongoing geopolitical tensions, have disrupted supply chains worldwide.
Japan is no exception.
Companies are increasingly looking at diversifying suppliers and increasing domestic production capabilities to shield against unforeseen disruptions.
Given Japan’s reliance on exports, such dynamics necessitate flexibility and adaptability within its manufacturing circuit.
Demographic Challenges
Japan faces a unique challenge with its aging population.
An increase in retirements may lead to workforce shortages in manufacturing.
To counteract, there’s been a substantial push towards automation and AI integration.
Additionally, industries are investing in training younger professionals in traditional skills, ensuring that expertise is passed on to new generations.
Best Practices from Japanese Manufacturing
From lean manufacturing principles to continuous improvement, several practices set Japanese companies apart.
Lean Manufacturing
Japanese manufacturing practices, particularly those derived from the Toyota Production System, focus on maximizing efficiency while minimizing waste.
Adopting lean principles can significantly streamline operations, ensuring seamless production processes that eliminate inefficiencies.
Key elements include Just-in-Time production, maintaining an orderly workplace through “5S” methodology, and fostering a culture of Kaizen or continuous improvement.
Quality Circles
Quality circles involve small groups of workers coming together to identify, analyze, and solve work-related problems.
This grassroots approach empowers employees, boosts morale, and unearths practical solutions to improve quality and processes.
The inclusion of diverse perspectives ensures that decisions are both informed and swiftly executable.
Kaizen Philosophy
Kaizen emphasizes continuous improvement across all facets of a business, from manufacturing to management.
This philosophy encourages team-based efforts to incrementally improve processes, eliminating waste, and enhancing productivity daily.
Embedding Kaizen deeply within organizational culture leads to sustainable improvements and sets a global standard in operational practices.
Conclusion
Japanese manufacturing excellence is the result of a unique blend of cultural values, innovative practices, and robust strategies.
By prioritizing quality and efficiency, Japanese manufacturers set global technical standards, influencing industries worldwide.
However, with changing market dynamics, adapting to new challenges and leveraging their intrinsic strengths will remain pivotal.
For businesses looking to incorporate these practices, understanding the nuances and intricacies of Japanese methodologies is key to successful integration.
By doing so, they can harness the immense potential of these time-tested approaches to thrive in the competitive global landscape.
資料ダウンロード
QCD調達購買管理クラウド「newji」は、調達購買部門で必要なQCD管理全てを備えた、現場特化型兼クラウド型の今世紀最高の購買管理システムとなります。
ユーザー登録
調達購買業務の効率化だけでなく、システムを導入することで、コスト削減や製品・資材のステータス可視化のほか、属人化していた購買情報の共有化による内部不正防止や統制にも役立ちます。
NEWJI DX
製造業に特化したデジタルトランスフォーメーション(DX)の実現を目指す請負開発型のコンサルティングサービスです。AI、iPaaS、および先端の技術を駆使して、製造プロセスの効率化、業務効率化、チームワーク強化、コスト削減、品質向上を実現します。このサービスは、製造業の課題を深く理解し、それに対する最適なデジタルソリューションを提供することで、企業が持続的な成長とイノベーションを達成できるようサポートします。
オンライン講座
製造業、主に購買・調達部門にお勤めの方々に向けた情報を配信しております。
新任の方やベテランの方、管理職を対象とした幅広いコンテンツをご用意しております。
お問い合わせ
コストダウンが利益に直結する術だと理解していても、なかなか前に進めることができない状況。そんな時は、newjiのコストダウン自動化機能で大きく利益貢献しよう!
(Β版非公開)