- お役立ち記事
- Improvement Points for Enhancing Efficiency in Extrusion Molding
Improvement Points for Enhancing Efficiency in Extrusion Molding
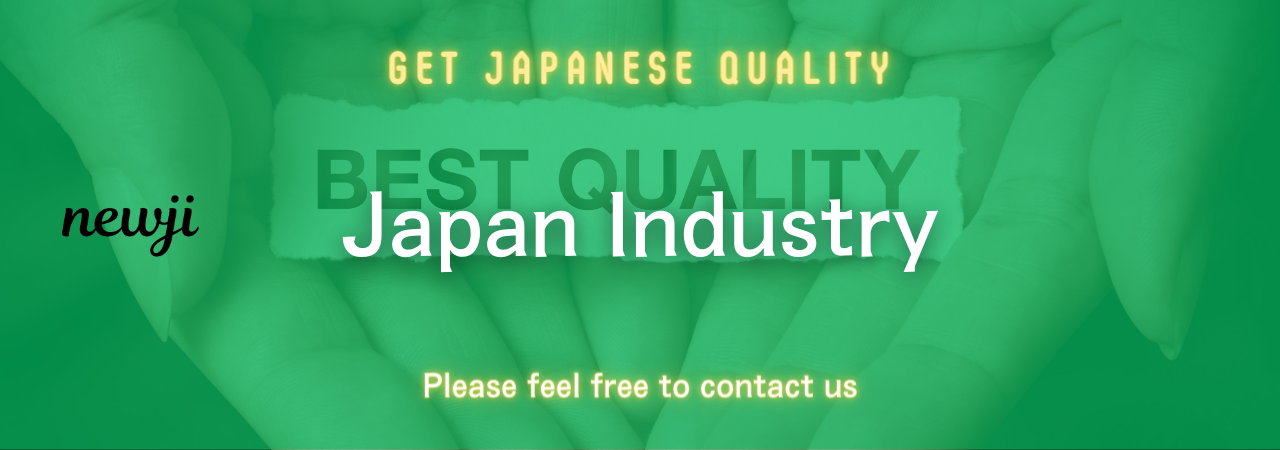
目次
Understanding Extrusion Molding
Extrusion molding is a process used in manufacturing to create objects with a consistent cross-section.
Materials such as plastic, metal, or rubber are pushed through a specialized mold, or die, to produce long shapes like pipes, tubes, or sheets.
The process begins with the feeding of raw material into an extruder, where it is melted and formed into a continuous shape as it passes through the die.
Extrusion molding is widely used in industries like automotive, construction, and packaging due to its ability to produce items quickly and with minimal waste.
However, like any manufacturing process, there are always opportunities to improve efficiency.
Importance of Efficiency in Extrusion Molding
Enhancing efficiency in extrusion molding translates into significant cost savings, improved product quality, and reduced environmental impact.
Efficient processes utilize less energy and produce fewer defective products, ultimately driving more profit for manufacturers.
Moreover, with growing environmental concerns, efficiency improvements can contribute to lower carbon emissions by reducing energy consumption and waste production.
By focusing on enhancing efficiency, manufacturers can also optimize their use of resources and improve their competitive edge in the market.
Optimization of Temperature Control
One critical area for improving efficiency in extrusion molding is temperature control.
Precise temperature management is essential for maintaining consistent material flow and product quality.
Improper temperature settings can lead to issues such as uneven material distribution, poor surface finish, and even defects.
To enhance temperature control, manufacturers can invest in advanced heating and cooling systems that provide uniform temperature distribution throughout the extrusion process.
Routine maintenance of the heating elements and regular calibration of temperature sensors can also contribute to more efficient processes by ensuring accuracy and reducing thermal inconsistencies.
Material Selection and Quality
Selecting the right material for the extrusion process plays a vital role in efficiency.
High-quality and consistent materials ensure smoother operation and better end-product characteristics.
Using inferior or inconsistent materials can lead to frequent process disruptions, increased waste, and lower product quality.
Manufacturers should establish strong relationships with reliable suppliers to secure quality raw materials.
Additionally, routine testing and inspection of incoming materials can identify potential issues before they affect the production line.
By ensuring that only the best materials enter the extrusion process, manufacturers can boost both efficiency and product reliability.
Die Design and Maintenance
The design and maintenance of dies are other critical factors influencing the efficiency of extrusion molding.
Well-designed dies can minimize friction, distribute material evenly, and reduce energy consumption.
Advanced die designs, such as those using computer-aided design (CAD) technology, can offer precise and customized solutions for specific product requirements.
Regular maintenance and cleaning of dies prevent material build-up, which can lead to defects and require additional energy to rectify.
By investing in the latest die technologies and adhering to a strict maintenance schedule, manufacturers can enhance the productivity and longevity of their extrusion equipment.
Extruder Equipment Upgrades
Extruders are at the core of the extrusion molding process, and upgrading this equipment can yield significant efficiency gains.
Modern extruders equipped with energy-efficient motors and improved screw designs can offer higher throughputs while consuming less energy.
Incorporating real-time monitoring systems in extrusion equipment can help identify and resolve issues proactively, thus preventing downtime and optimizing process conditions continuously.
Regular audits of existing equipment can reveal opportunities for upgrades, ensuring that manufacturers stay aligned with the latest industry standards and technological advancements.
Process Automation and Control Systems
Automation plays a pivotal role in the modern manufacturing landscape, and extrusion molding is no exception.
Automated control systems can enhance consistency and accuracy, minimizing human error and optimizing process efficiency.
Integrating sensors and control technologies into extrusion lines allows for real-time data collection and analysis.
This information can be utilized to adjust parameters and improve overall process performance dynamically.
A comprehensive automation strategy can also enhance worker safety and free up human resources for other critical tasks, further driving operational efficiency.
Employee Training and Involvement
Efficiency improvements are not solely reliant on technology and equipment but also on the people operating them.
Comprehensive training programs ensure that employees are well-versed in the latest processes and safety protocols.
Involving staff in continuous improvement initiatives can foster a culture of efficiency and innovation.
Employees can provide valuable insights into potential bottlenecks or areas for improvement, given their hands-on experience with the equipment and processes.
Regular feedback sessions and incentives for efficiency breakthroughs can further motivate employees and enhance their engagement with efficiency objectives.
Conclusion
Improving efficiency in extrusion molding is a multifaceted process that involves optimizing temperature control, material quality, die design, and equipment upgrades, among other areas.
By integrating advanced technology, enhancing process control, and fostering a culture of continuous improvement, manufacturers can significantly boost their operational efficiency.
Ultimately, these enhancements lead to cost savings, better product quality, and reduced environmental impact, which are essential in maintaining competitiveness in today’s demanding market landscape.
Proactive efforts to optimize extrusion molding processes yield long-term benefits that resonate across the manufacturing sector and contribute positively to overall business performance.
資料ダウンロード
QCD調達購買管理クラウド「newji」は、調達購買部門で必要なQCD管理全てを備えた、現場特化型兼クラウド型の今世紀最高の購買管理システムとなります。
ユーザー登録
調達購買業務の効率化だけでなく、システムを導入することで、コスト削減や製品・資材のステータス可視化のほか、属人化していた購買情報の共有化による内部不正防止や統制にも役立ちます。
NEWJI DX
製造業に特化したデジタルトランスフォーメーション(DX)の実現を目指す請負開発型のコンサルティングサービスです。AI、iPaaS、および先端の技術を駆使して、製造プロセスの効率化、業務効率化、チームワーク強化、コスト削減、品質向上を実現します。このサービスは、製造業の課題を深く理解し、それに対する最適なデジタルソリューションを提供することで、企業が持続的な成長とイノベーションを達成できるようサポートします。
オンライン講座
製造業、主に購買・調達部門にお勤めの方々に向けた情報を配信しております。
新任の方やベテランの方、管理職を対象とした幅広いコンテンツをご用意しております。
お問い合わせ
コストダウンが利益に直結する術だと理解していても、なかなか前に進めることができない状況。そんな時は、newjiのコストダウン自動化機能で大きく利益貢献しよう!
(Β版非公開)