- お役立ち記事
- For SMEs: Mold Design and Management Techniques to Prevent Burrs
For SMEs: Mold Design and Management Techniques to Prevent Burrs
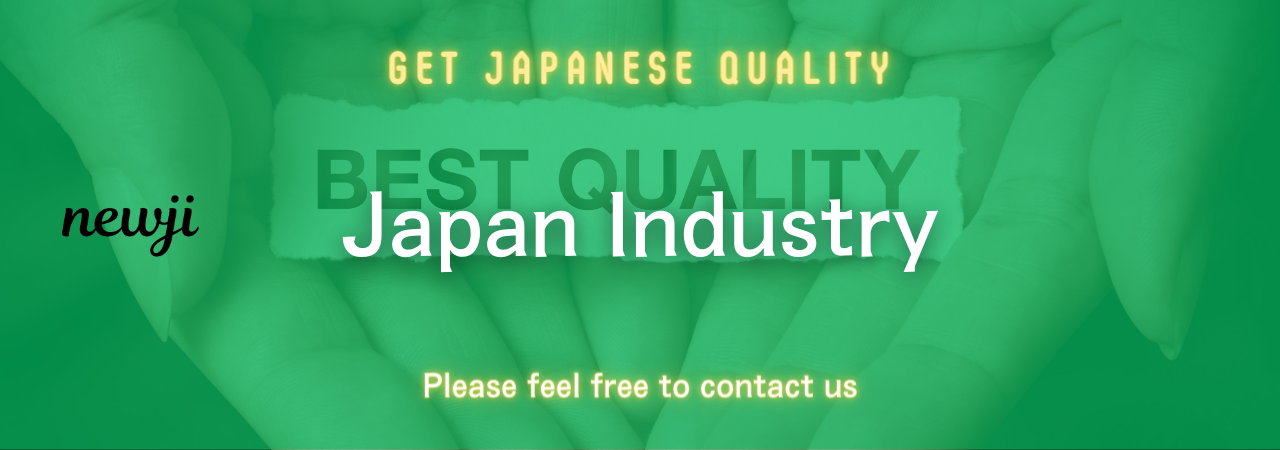
目次
Understanding the Importance of Mold Design in Small and Medium Enterprises
In the world of manufacturing, particularly for Small and Medium Enterprises (SMEs), efficient mold design plays a crucial role in ensuring product quality and minimizing defects.
One common issue faced in this process is the presence of burrs, the unwanted rough edges or protrusions on manufactured parts.
Understanding how to effectively design and manage molds can significantly help in preventing these unwanted imperfections, thereby improving the overall quality of the products.
What Causes Burrs in Molded Products?
Before delving into techniques to prevent burrs, it is essential to understand why they occur in the first place.
Burrs typically form due to misalignments in the mold or when excessive plastic or other materials escape through the mold cavity during the injection process.
Factors like improper clamping pressure, incorrect material temperature, or poor mold maintenance can exacerbate this issue.
The end result is a product with aesthetic and functional defects, something every SME aims to avoid.
Effective Mold Design Techniques
1. Precision in Mold Alignment
One of the fundamental aspects of preventing burrs is ensuring perfect alignment of the mold components.
This includes precise calibration of the core and cavity halves.
Regular monitoring and adjustments can help maintain the integrity of the design, thereby reducing the risk of material leakage.
2. Optimal Clamping Force
Appropriate clamping force is vital in keeping the mold closed during the injection process.
Too little pressure can result in gaps where material can leak out, forming burrs.
Conversely, excessive pressure might damage the mold.
It is crucial to determine the optimal clamping force specific to your materials and product specifications.
3. Temperature Control
Maintaining the right temperature during the molding process is another critical factor.
If the material is too hot, it becomes overly fluid and is more likely to escape the mold, resulting in burrs.
Implementing precise temperature controls ensures that the material is at an ideal consistency for molding.
Importance of Mold Maintenance
1. Regular Inspections
Conducting regular inspections of the mold is essential to identify wear and tear that might compromise the product’s quality.
Inspections can highlight any misalignments or damages that need immediate attention.
2. Cleaning and Lubrication
Routine cleaning and lubrication of the mold can prevent build-up that might affect the mold’s closing mechanism.
This upkeep is crucial to ensure smooth operations and to prevent the occurrence of burrs due to external debris.
3. Upgrading Components
Over time, some mold components may need upgrading or replacement.
Using advanced materials or technologies can significantly enhance the mold’s efficiency and lifespan, reducing the risk of defects.
Adopting Modern Technologies
Incorporating modern technologies in mold design and management can lead to better control and precision.
Software solutions, like CAD (Computer-Aided Design), allow SMEs to simulate the molding process, foresee potential problems, and make design improvements before physical implementation.
Automated monitoring systems can alert operators to any discrepancies in real-time, ensuring swift corrective measures are taken to prevent defects.
Training and Skilled Workforce
A well-trained workforce is fundamental to the effective execution of mold design and management strategies.
Investing in training programs helps employees understand the intricacies of the molding process and the impact of their roles in maintaining quality.
Experienced operators can make informed decisions quickly, which is vital in preventing burrs and similar issues.
Conclusion: The Impact on SMEs
For SMEs, efficient mold design and management are paramount to producing high-quality products that stand out in a competitive market.
By understanding and implementing strategies to prevent burrs, businesses can enhance their products’ aesthetic and functional value.
Proactive measures not only minimize defects but also reduce costs related to waste, rework, and returns.
As technology continues to advance, SMEs that keep pace with modern methods and tools are likely to lead the way in quality manufacturing.
This foresight is essential for long-term success and sustainability in the ever-evolving manufacturing industry.
資料ダウンロード
QCD調達購買管理クラウド「newji」は、調達購買部門で必要なQCD管理全てを備えた、現場特化型兼クラウド型の今世紀最高の購買管理システムとなります。
ユーザー登録
調達購買業務の効率化だけでなく、システムを導入することで、コスト削減や製品・資材のステータス可視化のほか、属人化していた購買情報の共有化による内部不正防止や統制にも役立ちます。
NEWJI DX
製造業に特化したデジタルトランスフォーメーション(DX)の実現を目指す請負開発型のコンサルティングサービスです。AI、iPaaS、および先端の技術を駆使して、製造プロセスの効率化、業務効率化、チームワーク強化、コスト削減、品質向上を実現します。このサービスは、製造業の課題を深く理解し、それに対する最適なデジタルソリューションを提供することで、企業が持続的な成長とイノベーションを達成できるようサポートします。
オンライン講座
製造業、主に購買・調達部門にお勤めの方々に向けた情報を配信しております。
新任の方やベテランの方、管理職を対象とした幅広いコンテンツをご用意しております。
お問い合わせ
コストダウンが利益に直結する術だと理解していても、なかなか前に進めることができない状況。そんな時は、newjiのコストダウン自動化機能で大きく利益貢献しよう!
(Β版非公開)