- お役立ち記事
- For SMEs: Optimizing Cooling Time to Enhance Product Quality
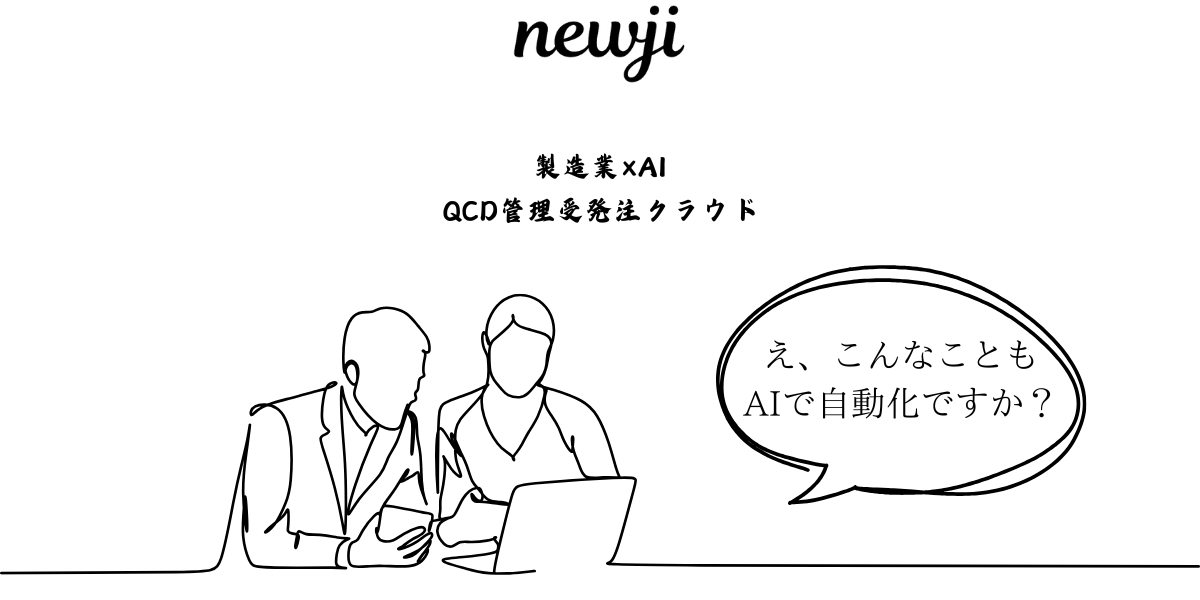
For SMEs: Optimizing Cooling Time to Enhance Product Quality
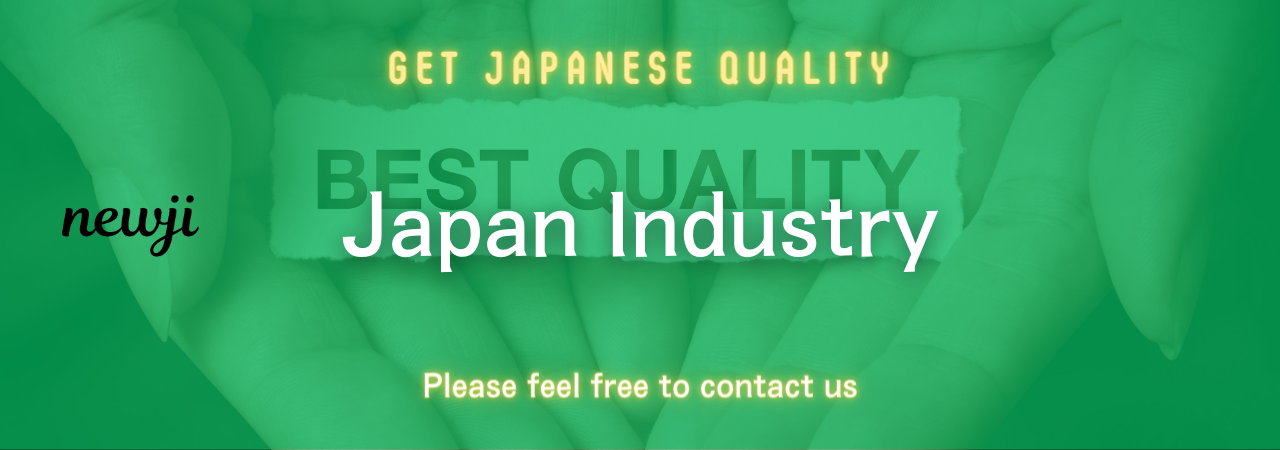
目次
Understanding the Importance of Cooling Time
In the manufacturing process, particularly for Small and Medium Enterprises (SMEs), cooling time plays a critical role in ensuring product quality.
Whether you produce food, plastic items, or any other products requiring temperature management, optimizing cooling time can significantly enhance the final output.
By understanding and managing this crucial phase, businesses can not only improve their products but also save on costs and reduce energy consumption.
What is Cooling Time?
Cooling time refers to the period needed for a product or material to reach its desired temperature after being exposed to heat during production.
In various industries, materials are heated to high temperatures for reshaping, molding, or cooking.
Once the desired shape or cooking stage is achieved, cooling down becomes essential to set the material, prevent deformations, and enhance product durability.
The Role of Cooling in Product Quality
The quality of a product is directly influenced by the cooling process.
For example, in the plastic molding industry, inadequate cooling times can lead to warping, reduced strength, and poor surface finishes.
In the food industry, improper cooling can affect taste, texture, and safety.
Thus, getting the cooling time just right is crucial for maintaining the integrity and appeal of the product.
Strategies for Optimizing Cooling Time
To ensure optimal cooling time in your production processes, consider the following strategies:
1. Understand Material Properties
Every material behaves differently when cooled.
Some may require gradual cooling, while others need a rapid decrease in temperature.
Understanding the thermal properties of your materials is the first step in determining the optimal cooling method.
Consult with material experts or conduct experiments to gain insights into the specific cooling needs of your products.
2. Implement Advanced Cooling Technologies
Modern cooling technologies such as chillers, cooling tunnels, and heat exchangers can be employed to ensure even and rapid cooling.
These devices not only enhance efficiency but also allow for better control over the cooling process, ensuring consistency across batches.
3. Monitor and Control the Environment
The environment where cooling takes place can significantly impact the cooling time.
Factors such as ambient temperature, humidity, and airflow need to be monitored and controlled to maintain optimal conditions.
Utilizing sensors and automated systems can help maintain these environmental factors within the desired range.
4. Conduct Regular Maintenance
Equipment used in the cooling process should be regularly maintained to prevent any inefficiencies or malfunctions.
Regular maintenance ensures that coolers and related machinery are operating at their optimal capacity, which contributes to consistent cooling times.
5. Evaluate and Adjust Cooling Time
Continuously evaluate your cooling times and make adjustments as necessary.
This may involve altering equipment settings based on seasonal changes or new material specifications.
Regular evaluations help in fine-tuning the cooling process and staying adaptable to any changes in production requirements.
Benefits of Optimizing Cooling Time
Optimizing the cooling time in production not only leads to higher product quality but also provides a myriad of other benefits:
1. Improved Product Consistency
By maintaining a consistent cooling process, you ensure that every product manufactured meets the same quality standards.
This is particularly important for businesses that rely on brand reputation and customer satisfaction.
2. Energy Efficiency
Reduced cooling times often translate to lower energy consumption, which can lead to significant cost savings.
Efficient cooling reduces the need for lengthy machine operation and minimizes energy waste, making the process more sustainable.
3. Increased Production Throughput
Optimizing cooling times allows for quicker turnover in production cycles.
This means more products can be manufactured in the same timeframe, increasing overall production capacity without compromising on quality.
4. Reduced Defects and Waste
With the right cooling times, the chances of defects such as warping, brittleness, or spoilage are minimized.
This reduces the amount of waste produced and decreases the need for rework, leading to overall cost savings.
Conclusion
For SMEs looking to enhance product quality, optimizing cooling time is a practical and impactful strategy.
By understanding material properties, implementing advanced cooling technologies, and maintaining control over environmental conditions, businesses can significantly improve product consistency, reduce energy consumption, and boost production efficiency.
Regular evaluations and adjustments further ensure that the cooling process remains effective amid varying production needs.
Investing time and resources into optimizing this crucial phase can lead to better products, happier customers, and a more successful business in the long run.
資料ダウンロード
QCD調達購買管理クラウド「newji」は、調達購買部門で必要なQCD管理全てを備えた、現場特化型兼クラウド型の今世紀最高の購買管理システムとなります。
ユーザー登録
調達購買業務の効率化だけでなく、システムを導入することで、コスト削減や製品・資材のステータス可視化のほか、属人化していた購買情報の共有化による内部不正防止や統制にも役立ちます。
NEWJI DX
製造業に特化したデジタルトランスフォーメーション(DX)の実現を目指す請負開発型のコンサルティングサービスです。AI、iPaaS、および先端の技術を駆使して、製造プロセスの効率化、業務効率化、チームワーク強化、コスト削減、品質向上を実現します。このサービスは、製造業の課題を深く理解し、それに対する最適なデジタルソリューションを提供することで、企業が持続的な成長とイノベーションを達成できるようサポートします。
オンライン講座
製造業、主に購買・調達部門にお勤めの方々に向けた情報を配信しております。
新任の方やベテランの方、管理職を対象とした幅広いコンテンツをご用意しております。
お問い合わせ
コストダウンが利益に直結する術だと理解していても、なかなか前に進めることができない状況。そんな時は、newjiのコストダウン自動化機能で大きく利益貢献しよう!
(Β版非公開)