- お役立ち記事
- A must-see for production control department managers! How to effectively introduce cell production methods to make your workplace more efficient
A must-see for production control department managers! How to effectively introduce cell production methods to make your workplace more efficient
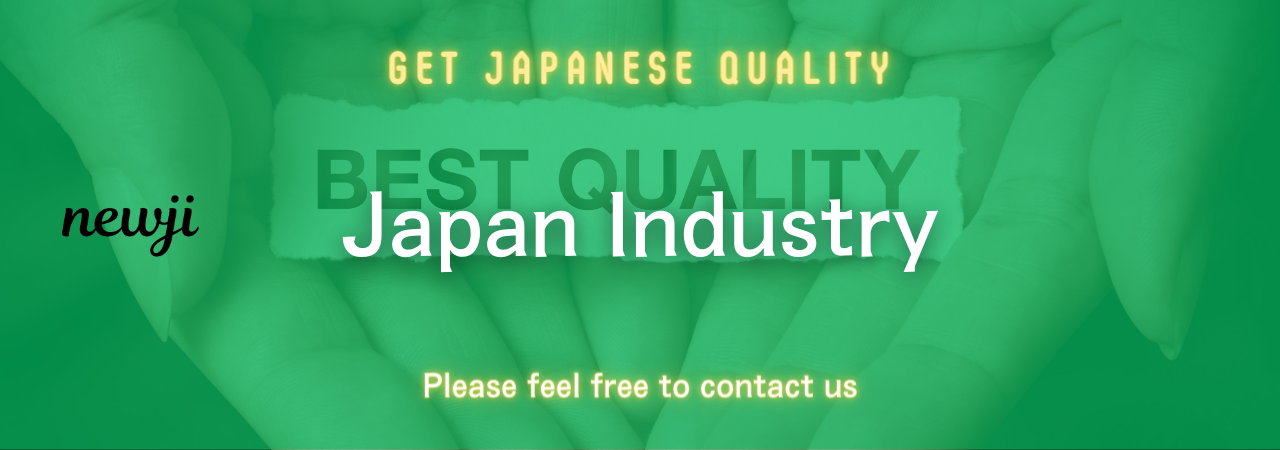
目次
Understanding Cell Production Methods
Cell production methods are a game-changer for manufacturing industries, offering a distinct approach to production management that emphasizes efficiency and flexibility.
Unlike traditional assembly lines, the cell production method groups workstations into cells, each responsible for a complete product or component.
This method minimizes waste, reduces lead times, and often results in higher quality outputs.
For production control department managers, understanding this approach is crucial as it can significantly improve workplace efficiency and employee satisfaction.
Benefits of Cell Production Methods
Increased Efficiency
One of the most notable advantages of cell production methods is the boost in efficiency.
By organizing production into cells, teams can work collaboratively, reducing downtime and bottlenecks.
Communication within a cell is smoother and quicker, which facilitates faster problem-solving and decision-making.
Tasks are often completed more quickly than in traditional production setups because team members can seamlessly transition between tasks.
Enhanced Flexibility
Cell production also introduces a higher level of flexibility in the manufacturing process.
Cells can be quickly reconfigured to adapt to new products, changes in demand, or improvements in technology.
This flexibility is especially valuable in industries subject to rapid changes, ensuring that production capabilities can scale up or down as necessary without incurring excessive costs or delays.
Improved Quality
With cell production methods, quality control is integrated into the process rather than being an afterthought.
Teams within cells take ownership of production stages, which often leads to higher-quality products.
Workers can identify and resolve issues in real time, preventing defects from propagating through the production line.
As a result, businesses can produce goods with fewer defects, improving customer satisfaction and reducing returns or recalls.
Enhanced Employee Engagement
The cell production method can also improve employee morale and engagement.
Workers are typically given more responsibility for managing the production process, which can increase job satisfaction.
They often develop a broader range of skills as they participate in multiple aspects of production, promoting personal and professional growth.
Engaged employees are more motivated, leading to improved productivity and lower turnover rates.
Steps to Introduce Cell Production Methods in Your Workplace
Evaluate Your Current Production System
Before introducing cell production methods, managers should thoroughly evaluate their current production system.
Understanding existing workflows, identifying bottlenecks, and analyzing productivity metrics are essential.
This assessment will serve as the foundation for designing cells and identifying areas where efficiency can be enhanced.
Create a Plan
Once you have a clear understanding of your current processes, develop a plan to implement cell production.
This should include a detailed layout of cell configurations, necessary equipment, and team assignments.
It’s crucial to set realistic goals and timelines for the transition and to consider any obstacles that may arise.
Engage and Train Employees
A successful transition to cell production hinges on employee involvement and training.
Involve your team in the planning phase to gather insights and foster a sense of ownership.
Conduct training sessions to equip employees with the skills needed to thrive in a cell production environment.
Focus on developing multitasking abilities, problem-solving skills, and teamwork.
Implement Gradually
Introducing cell production methods should be a gradual process.
Start with a pilot test on a small scale to evaluate the system’s effectiveness and make necessary adjustments.
Lessons learned during the pilot phase can be applied when scaling up the implementation across the entire production facility.
Monitor and Adjust
Post-implementation, it’s essential to closely monitor the performance of the new system.
Track key performance indicators (KPIs) such as productivity, quality, and employee satisfaction to gauge the success of cell production.
Regularly seek feedback from team members and be open to making adjustments to optimize the process.
Common Challenges and How to Overcome Them
Resistance to Change
Employees may resist the shift to a new production method due to fear of the unknown or concerns about increased workload.
To mitigate resistance, maintain clear and open communication.
Explain the benefits of the change and how it will enhance their work experience.
Providing adequate training and support also eases the transition.
Resource Constraints
Implementing cell production may require new equipment, additional training, or a reconfiguration of the workspace.
Resource constraints can pose a challenge, particularly for smaller organizations with limited budgets.
To address this, prioritize critical changes and explore options like leasing equipment or applying for grants that support process improvement initiatives.
Maintaining Quality Control
Quality control can be challenging in a cell production setting, especially if cells are producing varied products.
To maintain high standards, establish clear quality guidelines and regular inspections.
Encouraging a culture of responsibility and accountability within cells also ensures consistent quality.
Conclusion
Adopting cell production methods can transform your workplace into a more efficient, flexible, and engaging environment.
By following a strategic approach and addressing potential challenges, production control department managers can lead successful transitions to this innovative production style.
As the manufacturing landscape continues to evolve, embracing methods like cell production can provide a competitive edge and drive long-term success.
資料ダウンロード
QCD調達購買管理クラウド「newji」は、調達購買部門で必要なQCD管理全てを備えた、現場特化型兼クラウド型の今世紀最高の購買管理システムとなります。
ユーザー登録
調達購買業務の効率化だけでなく、システムを導入することで、コスト削減や製品・資材のステータス可視化のほか、属人化していた購買情報の共有化による内部不正防止や統制にも役立ちます。
NEWJI DX
製造業に特化したデジタルトランスフォーメーション(DX)の実現を目指す請負開発型のコンサルティングサービスです。AI、iPaaS、および先端の技術を駆使して、製造プロセスの効率化、業務効率化、チームワーク強化、コスト削減、品質向上を実現します。このサービスは、製造業の課題を深く理解し、それに対する最適なデジタルソリューションを提供することで、企業が持続的な成長とイノベーションを達成できるようサポートします。
オンライン講座
製造業、主に購買・調達部門にお勤めの方々に向けた情報を配信しております。
新任の方やベテランの方、管理職を対象とした幅広いコンテンツをご用意しております。
お問い合わせ
コストダウンが利益に直結する術だと理解していても、なかなか前に進めることができない状況。そんな時は、newjiのコストダウン自動化機能で大きく利益貢献しよう!
(Β版非公開)