- お役立ち記事
- DXing the Spacer Purging Process to Improve Quality and Reduce Costs
DXing the Spacer Purging Process to Improve Quality and Reduce Costs
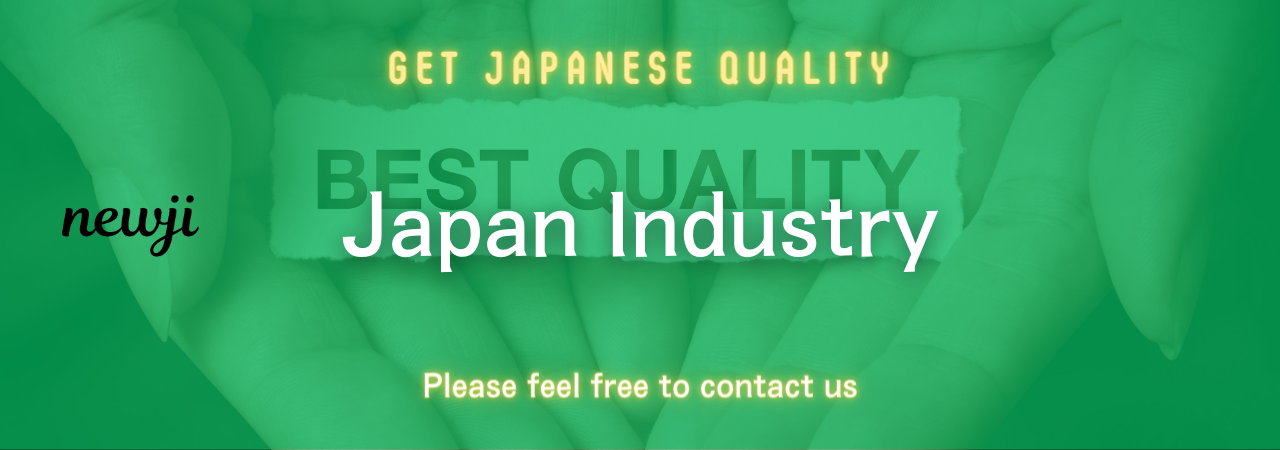
In the world of manufacturing, having a smooth and efficient process is key to ensuring high-quality products and keeping costs low. One such process that needs attention and optimization is the spacer purging process. This process is crucial in many industries but is often overlooked. By focusing on digital transformation, or DXing, the spacer purging process, businesses can see significant improvements in both quality and cost management.
目次
What is the Spacer Purging Process?
Before diving into the benefits of DXing the spacer purging process, it’s essential to understand what this process entails. Spacer purging involves the removal of unwanted material or gases from a specific space or cavity within a manufacturing process. This step is crucial in preventing contamination, ensuring material integrity, and promoting overall product quality.
In various industries like automotive, aerospace, and electronics, spacer purging plays a vital role. Improper purging can lead to defects, product recalls, and even safety hazards. Therefore, refining this process through digital means can bring about transformative benefits.
The Role of Digital Transformation (DX)
Digital transformation refers to the integration of digital technology into all areas of a business, fundamentally changing how industries operate and deliver value to customers. When applied to the spacer purging process, digital transformation can include the use of automation, data analysis, and advanced monitoring technologies.
1. Automation
Automating the spacer purging process can lead to increased efficiency and consistency. Automation tools can perform repetitive tasks without the risk of human error. For example, robotic arms or automated purging systems can be programmed to perform precise purging actions in a consistent manner, reducing the likelihood of contamination and defects.
2. Data Analysis
Implementing data analysis tools can provide valuable insights into the purging process. By collecting and analyzing data from various stages of the process, manufacturers can identify bottlenecks, inefficiencies, and areas for improvement. This continuous feedback loop allows for ongoing process refinement.
3. Advanced Monitoring Technologies
Advanced monitoring technologies, such as IoT sensors and machine learning algorithms, can play a significant role in optimizing the spacer purging process. These technologies can provide real-time monitoring and alerts, ensuring that any deviations or abnormalities are quickly addressed.
Benefits of DXing the Spacer Purging Process
Now that we understand the components of digital transformation, let’s explore the specific benefits of applying these technologies to the spacer purging process.
1. Improved Quality Control
One of the most significant benefits of DXing the spacer purging process is improved quality control. Automated systems and advanced monitoring technologies can maintain consistent purging conditions, significantly reducing the risk of contamination. This leads to higher-quality products and fewer defects, ultimately enhancing customer satisfaction.
2. Cost Reduction
By implementing automation and data analysis, manufacturers can reduce labor costs and minimize waste. Automated purging systems can perform tasks more efficiently than humans, freeing up skilled workers to focus on more complex and value-added activities. Additionally, data-driven insights can help identify areas where resources are being underutilized or wasted, leading to cost savings.
3. Increased Efficiency
Digital transformation can streamline the spacer purging process, reducing the time required to complete each cycle. By eliminating bottlenecks and optimizing workflow, manufacturers can achieve higher throughput and faster production times. This increased efficiency translates to greater overall productivity.
4. Enhanced Safety
Spacer purging often involves handling hazardous materials or working in environments with stringent safety requirements. Automation and advanced monitoring can reduce the need for human intervention in potentially dangerous situations, improving overall workplace safety.
5. Data-Driven Decision Making
With the continuous flow of data from automated systems and monitoring technologies, manufacturers can make more informed decisions. These insights enable proactive maintenance, allowing companies to address potential issues before they escalate. Data-driven decision-making also supports strategic planning and process optimization.
Implementing DX in the Spacer Purging Process
To successfully DX the spacer purging process, manufacturers need a well-defined strategy and a phased approach. Here are some key steps to consider:
1. Assess Current Processes
Start by conducting a thorough assessment of the current spacer purging process. Identify pain points, inefficiencies, and areas where digital technologies can make a significant impact. This assessment will serve as a baseline for measuring improvements.
2. Define Objectives
Clearly articulate the objectives of the digital transformation initiative. Whether it’s improving quality, reducing costs, increasing efficiency, or enhancing safety, having well-defined goals will guide the implementation process.
3. Select Appropriate Technologies
Based on the assessment and objectives, choose the digital technologies that best suit your needs. This may include automation tools, IoT sensors, data analytics software, and machine learning algorithms. Consider working with technology partners or consultants to ensure a smooth integration.
4. Pilot and Iterate
Implement the chosen technologies on a small scale, such as a pilot project. Monitor the results closely and gather feedback from stakeholders. Use this feedback to refine and optimize the process before scaling up.
5. Scale and Monitor
Once the pilot phase is successful, scale up the implementation across the entire spacer purging process. Continuously monitor performance, analyze data, and make ongoing adjustments to maintain and improve efficiency and quality.
DXing the spacer purging process is a powerful way to enhance quality, reduce costs, and increase efficiency in manufacturing. By embracing automation, data analysis, and advanced monitoring technologies, businesses can achieve significant improvements in their operations. The benefits of digital transformation extend beyond the purging process, influencing overall production, customer satisfaction, and profitability. As industries continue to evolve, those who invest in digital transformation will be better positioned to thrive in a competitive landscape.
資料ダウンロード
QCD調達購買管理クラウド「newji」は、調達購買部門で必要なQCD管理全てを備えた、現場特化型兼クラウド型の今世紀最高の購買管理システムとなります。
ユーザー登録
調達購買業務の効率化だけでなく、システムを導入することで、コスト削減や製品・資材のステータス可視化のほか、属人化していた購買情報の共有化による内部不正防止や統制にも役立ちます。
NEWJI DX
製造業に特化したデジタルトランスフォーメーション(DX)の実現を目指す請負開発型のコンサルティングサービスです。AI、iPaaS、および先端の技術を駆使して、製造プロセスの効率化、業務効率化、チームワーク強化、コスト削減、品質向上を実現します。このサービスは、製造業の課題を深く理解し、それに対する最適なデジタルソリューションを提供することで、企業が持続的な成長とイノベーションを達成できるようサポートします。
オンライン講座
製造業、主に購買・調達部門にお勤めの方々に向けた情報を配信しております。
新任の方やベテランの方、管理職を対象とした幅広いコンテンツをご用意しております。
お問い合わせ
コストダウンが利益に直結する術だと理解していても、なかなか前に進めることができない状況。そんな時は、newjiのコストダウン自動化機能で大きく利益貢献しよう!
(Β版非公開)