- お役立ち記事
- A Guide to Optimizing Production Lines When Installing Injection Molding Machines
A Guide to Optimizing Production Lines When Installing Injection Molding Machines
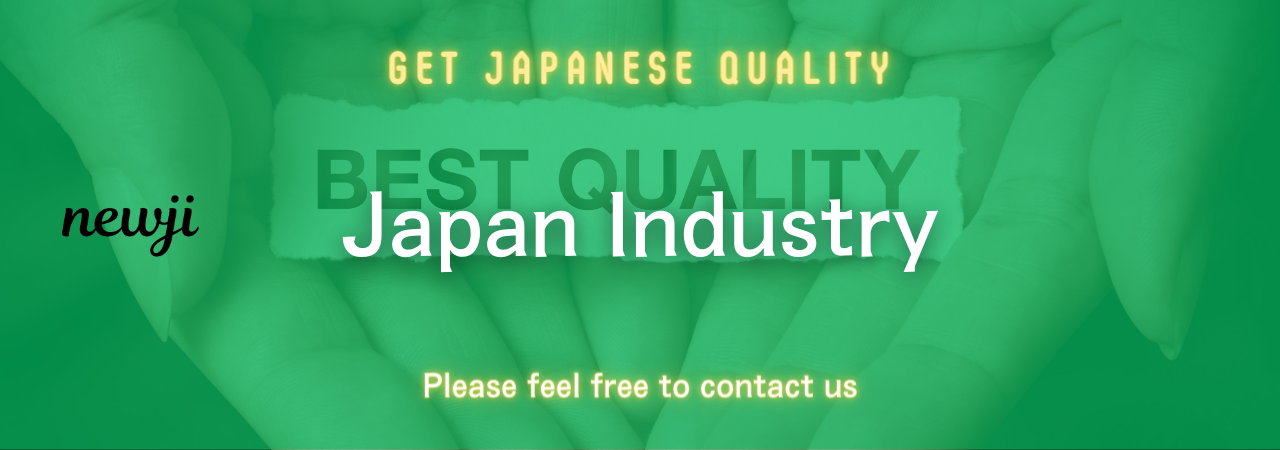
目次
Understanding Injection Molding Machines
Injection molding machines are vital assets in manufacturing, playing a crucial role in producing everyday products from automotive parts to household items.
These machines function by injecting molten materials into molds, which then cool and solidify into the desired shape.
With the right setup and optimization, they can dramatically enhance the efficiency and quality of production lines.
Types of Injection Molding Machines
Before you can optimize your production line, it’s important to understand the different types of injection molding machines available.
There are mainly three types: hydraulic, electric, and hybrid machines.
Hydraulic machines are reliable and cost-effective, suitable for tasks that require substantial clamping force.
Electric machines offer precision and energy efficiency, which is ideal for high-speed operations with tight tolerances.
Hybrid machines combine the benefits of both hydraulic and electric machines, providing a balance of power and efficiency.
Identifying the right machine type based on specific production needs is the first step towards optimization.
Evaluating Your Production Needs
Optimization starts with a thorough evaluation of your production requirements.
Consider the volume, complexity, and material of the products you plan to manufacture.
Higher complexity might demand machines with better precision, while high-volume production will benefit from machines equipped for rapid operations.
Determining the right balance of speed, accuracy, and energy consumption is essential for maximizing productivity and reducing costs.
Setting Clear Goals
Clear goals are necessary for successful line optimization.
These can include improving output quality, increasing production speed, or reducing energy costs.
Goals will guide decision-making throughout the process and help track progress over time.
Aligning them with overall business objectives ensures that optimization efforts contribute to greater organizational success.
Designing Efficient Workflow
An efficient workflow integrates all aspects of production: machine operation, material handling, and quality control.
Streamlined processes reduce bottlenecks and ensure smooth transitions between different stages of manufacturing.
Consider automating repetitive tasks and strategically arranging equipment to minimize downtime.
Lean manufacturing principles can be applied to eliminate waste and enhance productivity.
Material Selection and Management
Choosing the right materials impacts both the quality of the final product and the efficiency of the injection molding process.
Evaluate the properties of different materials, such as strength, durability, and cost-effectiveness.
Once selected, manage materials wisely by maintaining optimal inventory levels and ensuring proper storage conditions.
This prevents machine interruptions due to supply shortages and preserves material quality.
Training and Skill Development
Optimizing production lines often requires skilled operators who understand both the machinery and the overall manufacturing process.
Continuous training programs can improve their understanding of machine operations and maintenance requirements.
Skilled employees are better equipped to identify issues early and implement solutions effectively, reducing machine downtime and enhancing production quality.
Utilizing Technology and Software
Advancements in technology have introduced powerful tools and software that can assist in optimizing production lines.
Integrated software systems can monitor machine performance, predict maintenance needs, and streamline scheduling.
Employing such technology helps in making data-driven decisions that enhance efficiency and product quality.
Regular Maintenance and Calibration
Maintaining injection molding machines is crucial for consistent production quality and reduced downtime.
Regular maintenance checks identify and address potential issues before they escalate.
Calibration ensures that machines operate within specified parameters, preserving product consistency and reducing waste.
Implementing a routine maintenance schedule keeps machines running at peak efficiency, thereby extending their lifespan and reducing costs.
Continuous Improvement and Monitoring
Optimization is an ongoing process.
Regularly monitoring machine performance and production outcomes allows you to make necessary adjustments and improvements over time.
Encourage feedback from machine operators and other team members to identify areas for further enhancement.
By fostering a culture of continuous improvement, production lines can adapt to changing market demands and technological advancements.
The Benefits of Optimization
Optimizing production lines when installing injection molding machines offers numerous benefits.
Improved efficiency translates to faster production times and lower operational costs.
Enhanced product quality meets customer expectations and strengthens brand reputation.
Additionally, reduced resource consumption contributes to sustainable manufacturing practices, which is increasingly important in today’s environmentally-conscious market.
Conclusion
Optimizing production lines with injection molding machines requires a strategic approach that considers machine types, production needs, workflow design, and more.
By setting clear goals and leveraging advanced technologies, manufacturers can achieve higher efficiency and better-quality products.
Regular maintenance and a focus on continuous improvement further ensure that production lines remain adaptive and competitive.
Ultimately, thoughtful optimization enhances productivity, reduces costs, and supports sustainable manufacturing practices, benefiting both the organization and its customers.
資料ダウンロード
QCD調達購買管理クラウド「newji」は、調達購買部門で必要なQCD管理全てを備えた、現場特化型兼クラウド型の今世紀最高の購買管理システムとなります。
ユーザー登録
調達購買業務の効率化だけでなく、システムを導入することで、コスト削減や製品・資材のステータス可視化のほか、属人化していた購買情報の共有化による内部不正防止や統制にも役立ちます。
NEWJI DX
製造業に特化したデジタルトランスフォーメーション(DX)の実現を目指す請負開発型のコンサルティングサービスです。AI、iPaaS、および先端の技術を駆使して、製造プロセスの効率化、業務効率化、チームワーク強化、コスト削減、品質向上を実現します。このサービスは、製造業の課題を深く理解し、それに対する最適なデジタルソリューションを提供することで、企業が持続的な成長とイノベーションを達成できるようサポートします。
オンライン講座
製造業、主に購買・調達部門にお勤めの方々に向けた情報を配信しております。
新任の方やベテランの方、管理職を対象とした幅広いコンテンツをご用意しております。
お問い合わせ
コストダウンが利益に直結する術だと理解していても、なかなか前に進めることができない状況。そんな時は、newjiのコストダウン自動化機能で大きく利益貢献しよう!
(Β版非公開)