- お役立ち記事
- Basics and practical methods of quality function deployment (QFD) that new employees in the product design department should learn
月間93,089名の
製造業ご担当者様が閲覧しています*
*2025年6月30日現在のGoogle Analyticsのデータより
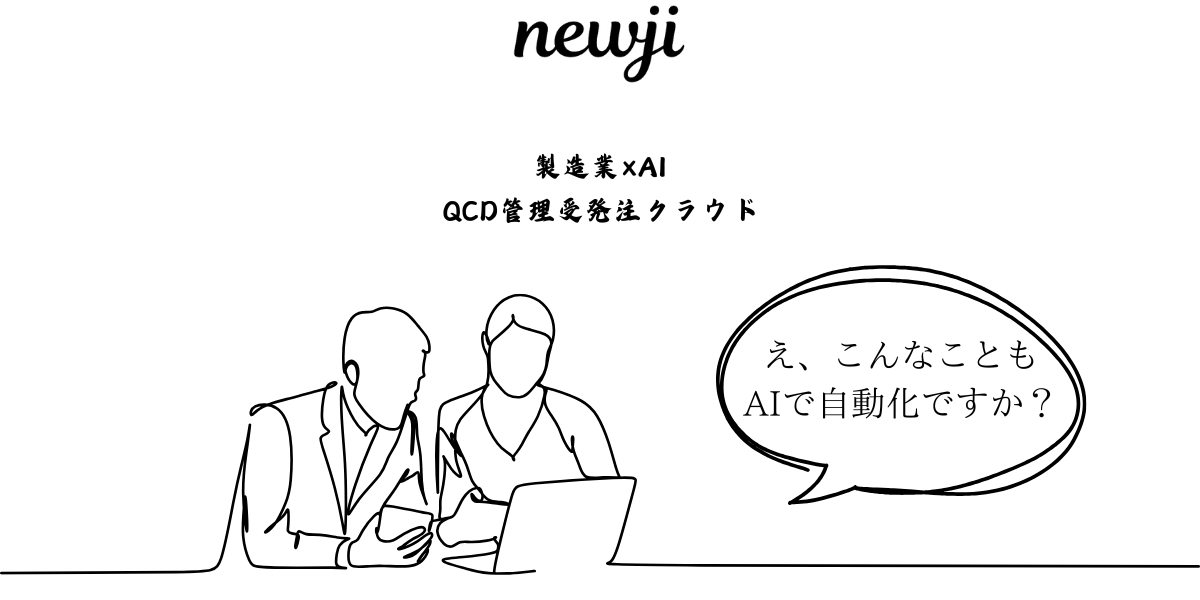
Basics and practical methods of quality function deployment (QFD) that new employees in the product design department should learn
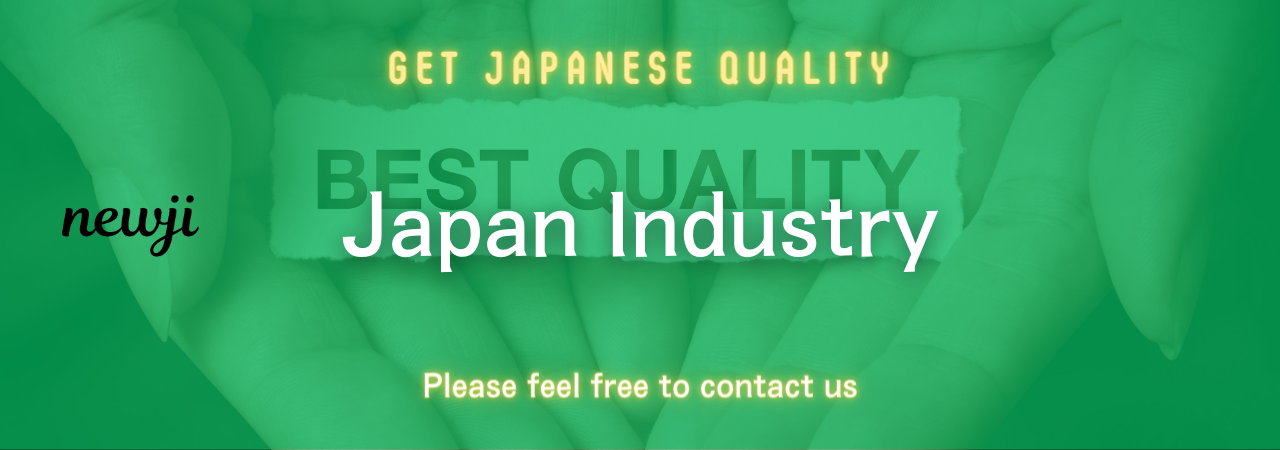
目次
Understanding Quality Function Deployment (QFD)
Quality Function Deployment (QFD) is a powerful tool used in the product design process to ensure that the final product meets or exceeds customer expectations.
It is a structured approach that helps translate customer requirements into appropriate company requirements at every stage, from research and development to engineering and manufacturing.
New employees in the product design department can benefit greatly from understanding the basics and practical methods of QFD to improve the efficiency and effectiveness of product development.
QFD originated in Japan in the late 1960s, mainly through the efforts of Yoji Akao.
Since then, it has been widely adopted by companies around the world to enhance the quality of products.
By prioritizing customer needs and preferences, QFD helps create products that not only meet quality standards but also provide value to customers.
The Basics of QFD
QFD is based on the principle that customer satisfaction should drive the product development process.
To achieve this, QFD translates the voice of the customer into design specifications.
This is done using a QFD matrix, also known as the House of Quality.
The House of Quality is the most widely used matrix in QFD.
It helps visualize the relationship between customer requirements and the company’s ability to meet those requirements.
The matrix includes customer requirements, technical descriptors, and a relationship matrix that connects them.
Customer requirements are typically gathered through surveys, interviews, focus groups, and other research methods.
These are often referred to as the “Whats.”
Technical descriptors, or the “Hows,” are the means by which the company plans to fulfill these requirements.
The relationship matrix is a crucial component of the House of Quality.
It shows the strength of the correlation between customer requirements and technical descriptors, allowing teams to focus on areas that need significant attention.
Steps in Quality Function Deployment
QFD involves several steps to systematically convert customer needs into product features and processes.
New employees should understand these steps to effectively contribute to the product design process.
1. Identify Customer Needs
The first step in QFD is to gather and identify customer needs.
This can be done through various market research techniques.
The aim is to capture the voice of the customer accurately and comprehensively.
Customer needs should be ranked in terms of importance to determine which features to prioritize.
2. Establish Design Requirements
Once customer needs are gathered, the next step is to establish design requirements, or technical descriptors, for the product.
These are specific, measurable, and actionable features that must be included to satisfy the customer needs identified in the first step.
3. Develop the House of Quality
The House of Quality is then developed to map out the relationship between customer needs and design requirements.
This involves creating a matrix that shows how each customer need relates to the design requirements and the strength of these relationships.
This step also involves brainstorming and collaboration among various departments, including marketing, design, engineering, and manufacturing.
4. Prioritize Requirements
With the House of Quality in place, the next step is prioritizing design requirements.
This is done by analyzing the strength of the relationships illustrated in the matrix.
Requirements that have a significant impact on fulfilling customer needs are given higher priority.
5. Implement Design Solutions
After prioritizing the design requirements, the product design team develops specific design solutions to meet these requirements.
This step involves detailed planning and coordination to ensure that the final product aligns with the customer’s expectations.
Practical Methods for Using QFD
New employees can adopt several practical methods when implementing QFD to enhance their understanding and execution of the tool.
Collaborative Teamwork
QFD is inherently a collaborative process.
Involving cross-functional teams early in the process can lead to more informed decisions and better solutions.
Regular meetings and workshops with representatives from all related departments ensure that every aspect of product design is considered.
Iterative Approach
QFD is most effective when used iteratively.
Continuous refinement and iteration based on feedback help in aligning the product more closely with customer needs.
Regular updates to the House of Quality keep the design aligned with evolving customer preferences and market trends.
Customer Feedback
Direct involvement of customers in the QFD process can provide deeper insights into their needs.
Employing methods like co-creation workshops or customer feedback sessions during the design phase ensures that the product team is on the right track.
Training and Development
New employees should pursue training sessions on QFD to deepen their understanding of its methodologies.
Learning from experienced team members and engaging in training workshops can be incredibly beneficial in mastering QFD techniques.
Utilizing Software Tools
Many software solutions are available that simplify the creation of QFD matrices and automate much of the analysis required.
These tools can help streamline the process, ensuring accuracy and efficiency.
Conclusion
Quality Function Deployment is an invaluable tool for new employees in the product design department.
By systematically translating customer needs into product specifications, QFD ensures that the products developed are aligned with market demands.
Understanding and applying the basics and practical methods of QFD can significantly enhance the ability of new employees to contribute to successful product outcomes.
With practice and experience, QFD can transform into an integral part of the product design process, leading to products that truly delight customers.
資料ダウンロード
QCD管理受発注クラウド「newji」は、受発注部門で必要なQCD管理全てを備えた、現場特化型兼クラウド型の今世紀最高の受発注管理システムとなります。
ユーザー登録
受発注業務の効率化だけでなく、システムを導入することで、コスト削減や製品・資材のステータス可視化のほか、属人化していた受発注情報の共有化による内部不正防止や統制にも役立ちます。
NEWJI DX
製造業に特化したデジタルトランスフォーメーション(DX)の実現を目指す請負開発型のコンサルティングサービスです。AI、iPaaS、および先端の技術を駆使して、製造プロセスの効率化、業務効率化、チームワーク強化、コスト削減、品質向上を実現します。このサービスは、製造業の課題を深く理解し、それに対する最適なデジタルソリューションを提供することで、企業が持続的な成長とイノベーションを達成できるようサポートします。
製造業ニュース解説
製造業、主に購買・調達部門にお勤めの方々に向けた情報を配信しております。
新任の方やベテランの方、管理職を対象とした幅広いコンテンツをご用意しております。
お問い合わせ
コストダウンが利益に直結する術だと理解していても、なかなか前に進めることができない状況。そんな時は、newjiのコストダウン自動化機能で大きく利益貢献しよう!
(β版非公開)