- お役立ち記事
- DX of Strike Process Improves Base Metal Activation and Quality
DX of Strike Process Improves Base Metal Activation and Quality
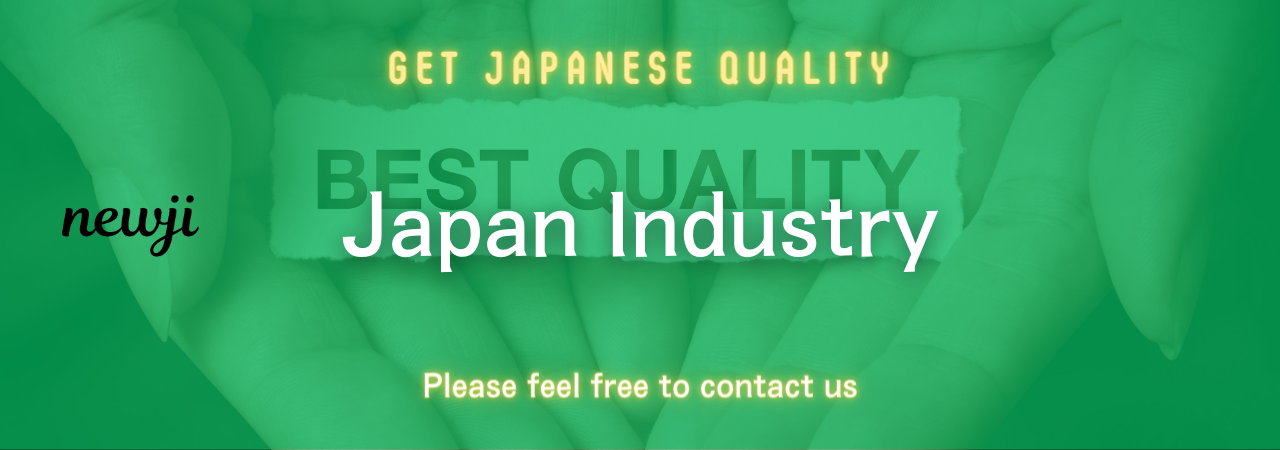
In today’s rapidly evolving technological landscape, industries continuously seek ways to improve efficiency, reduce costs, and enhance the quality of their products. One method that has gained significant attention is the digital transformation (DX) of various processes. In particular, the DX of the strike process has shown remarkable benefits in activating base metals and improving their overall quality.
Understanding the Strike Process and Its Importance
The strike process, commonly known as a flash plating or initial plating, is a critical step in the metal finishing industry. It involves depositing a thin layer of metal onto a substrate to activate the base metal, ensuring better adhesion of subsequent plating layers. This step is essential for enhancing the overall durability and quality of the final product.
By digitally transforming the strike process, industries can optimize this crucial step, leading to improved base metal activation and higher-quality finished products. Let’s delve into some key components and benefits.
Digital Transformation: The Cornerstone of Modern Industrial Processes
Digital transformation refers to integrating digital technology into all business areas, fundamentally changing operational methods and delivering value to customers. In the context of the strike process, it involves leveraging advanced technologies like data analytics, IoT (Internet of Things), and AI (Artificial Intelligence) to enhance process efficiency and effectiveness.
Enhancing Base Metal Activation
One of the primary benefits of DX in the strike process is the enhanced activation of base metals. By utilizing data analytics and IoT sensors, the strike bath chemistry can be monitored and controlled with unprecedented precision. This ensures optimal conditions for the activation layer, resulting in better adhesion and fewer defects in subsequent plating layers.
Data-Driven Decision Making
The integration of digital technologies allows for real-time data collection and analysis. By continuously monitoring parameters such as temperature, pH levels, and electrical current, manufacturers can make data-driven decisions to adjust the strike process in real time. This dynamic control significantly reduces the likelihood of errors and inconsistencies, leading to a higher-quality end product.
Predictive Maintenance for Improved Efficiency
DX enables the implementation of predictive maintenance strategies. IoT sensors and advanced analytics can predict when equipment is likely to fail or require maintenance. Manufacturers can schedule maintenance activities proactively, reducing downtime and preventing disruptions in the production process. This not only improves efficiency but also ensures the strike process operates at peak performance continually.
Quality Control and Assurance
Quality control is paramount in the metal finishing industry. The digital transformation of the strike process facilitates comprehensive quality assurance protocols. By comparing real-time data to historical trends, manufacturers can identify deviations and take corrective actions promptly. This proactive approach minimizes defects and ensures consistent, high-quality plating results.
Environmental Sustainability
Beyond quality and efficiency, the DX of the strike process contributes to environmental sustainability. Traditional plating processes can be resource-intensive and generate hazardous waste. However, digital technologies enable precise control over chemical usage, reducing waste generation and minimizing environmental impact. Additionally, real-time monitoring allows for the efficient recycling of plating solutions, further promoting sustainability.
Case Studies: Real-World Applications and Success Stories
Case studies from various industries highlight the transformative potential of DX in the strike process. For instance, a leading automotive manufacturer implemented IoT-enabled sensors in their strike baths, resulting in a 30% reduction in process variability. This improvement led to enhanced adhesion of subsequent plating layers, improving product durability and reducing warranty claims.
Similarly, an electronics manufacturer incorporated AI-driven analytics into their strike process, achieving a 25% increase in production yield. The ability to predict and mitigate issues before they escalated ensured a consistent, high-quality output, enhancing customer satisfaction and loyalty.
Future Prospects: A Glimpse into the Future of Metal Finishing
The DX of the strike process is just the beginning. As technology continues to evolve, so will the possibilities for further improvements in metal finishing. Emerging trends such as machine learning, advanced robotics, and digital twins hold the potential to revolutionize the industry further.
Machine Learning and Artificial Intelligence
Machine learning algorithms can analyze vast data sets to identify patterns and optimize the strike process parameters. Over time, these algorithms can develop predictive models that continuously improve process efficiency and product quality. AI-driven automation can also streamline repetitive tasks, freeing human operators to focus on more complex and strategic activities.
Advanced Robotics and Automation
Advanced robotics can enhance the precision and consistency of the strike process. Robotic arms equipped with sensors can perform intricate movements with micrometer-level accuracy, ensuring uniform deposition of the activation layer. Automation not only improves process control but also reduces human error and increases productivity.
Digital Twins for Simulation and Optimization
Digital twins, virtual replicas of physical processes, enable simulation and optimization in a risk-free environment. By creating a digital replica of the strike process, manufacturers can experiment with different parameters and scenarios to identify the most efficient and effective methods. Digital twins also facilitate remote monitoring and troubleshooting, reducing the need for on-site interventions.
Conclusion: Embracing the Future of Metal Finishing
The digital transformation of the strike process marks a new era in the metal finishing industry. By harnessing the power of data analytics, IoT, AI, and other advanced technologies, industries can significantly enhance base metal activation and improve the overall quality of their products.
Efforts to integrate these digital solutions are not just about staying competitive but about driving innovation, sustainability, and superior outcomes for customers. As technology continues to advance, the possibilities for further improvements in the strike process are limitless. Embracing digital transformation is essential for industries looking to lead in quality, efficiency, and environmental responsibility.
資料ダウンロード
QCD調達購買管理クラウド「newji」は、調達購買部門で必要なQCD管理全てを備えた、現場特化型兼クラウド型の今世紀最高の購買管理システムとなります。
ユーザー登録
調達購買業務の効率化だけでなく、システムを導入することで、コスト削減や製品・資材のステータス可視化のほか、属人化していた購買情報の共有化による内部不正防止や統制にも役立ちます。
NEWJI DX
製造業に特化したデジタルトランスフォーメーション(DX)の実現を目指す請負開発型のコンサルティングサービスです。AI、iPaaS、および先端の技術を駆使して、製造プロセスの効率化、業務効率化、チームワーク強化、コスト削減、品質向上を実現します。このサービスは、製造業の課題を深く理解し、それに対する最適なデジタルソリューションを提供することで、企業が持続的な成長とイノベーションを達成できるようサポートします。
オンライン講座
製造業、主に購買・調達部門にお勤めの方々に向けた情報を配信しております。
新任の方やベテランの方、管理職を対象とした幅広いコンテンツをご用意しております。
お問い合わせ
コストダウンが利益に直結する術だと理解していても、なかなか前に進めることができない状況。そんな時は、newjiのコストダウン自動化機能で大きく利益貢献しよう!
(Β版非公開)