- お役立ち記事
- Fundamentals of CAN protocol and application to control technology and control software development
月間93,089名の
製造業ご担当者様が閲覧しています*
*2025年6月30日現在のGoogle Analyticsのデータより
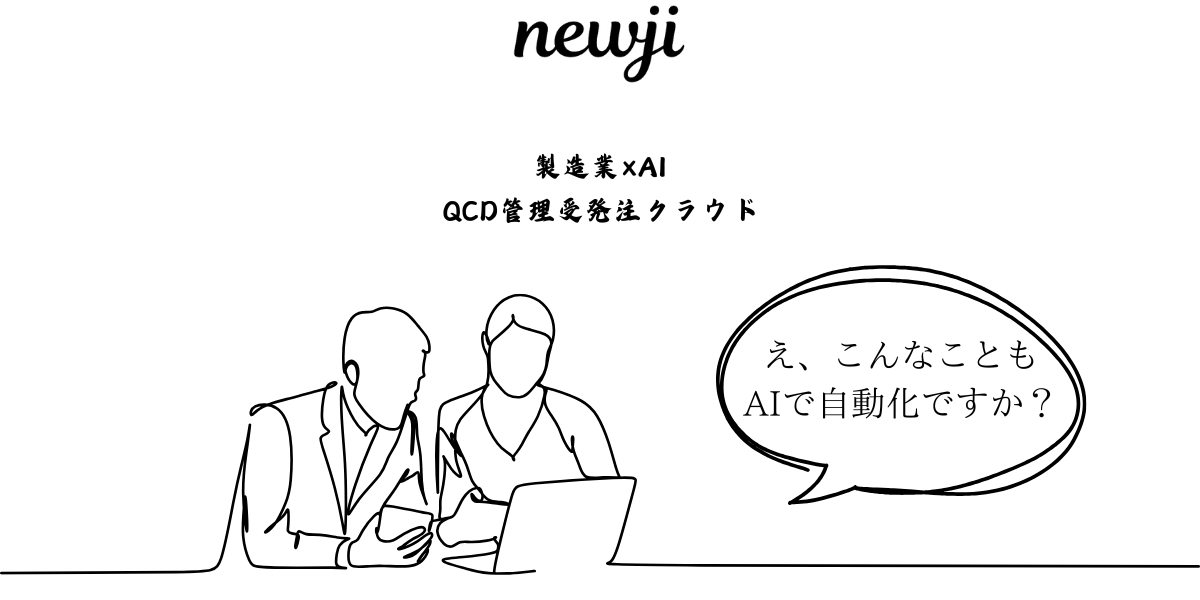
Fundamentals of CAN protocol and application to control technology and control software development
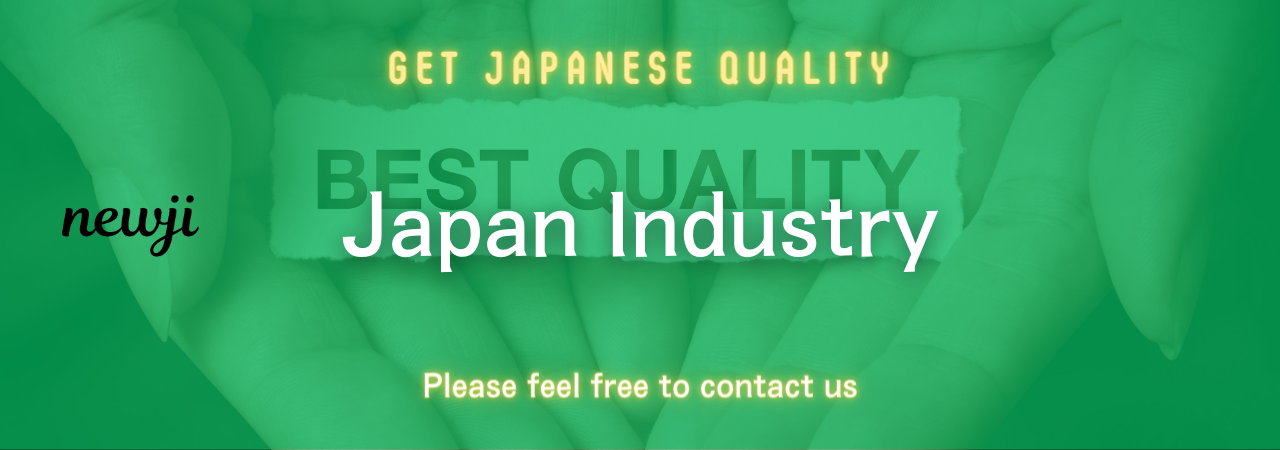
目次
Understanding the Basics of CAN Protocol
The Controller Area Network, commonly known as CAN, is a robust vehicle bus standard that allows microcontrollers and devices to communicate with each other without the need for a host computer.
Originally developed by Bosch in the 1980s, CAN is used in a variety of applications, including automotive, aerospace, and industrial automation.
At the heart of CAN protocol is its ability to provide reliable and efficient communication.
CAN operates on a message-based protocol, which means that messages are broadcast to all nodes in the network, allowing for decentralized control.
This peer-to-peer network communication ensures that no single point failure can bring down the entire system.
The protocol supports data transfer rates up to 1 Mbps, which, for many applications, is more than sufficient.
CAN uses two wires for communication: CAN High (CANH) and CAN Low (CANL).
These twisted pair wires help to shield against electromagnetic interference, providing robust communication even in noisy environments.
When a device wants to send a message, it creates a differential voltage between CANH and CANL.
Other devices on the network read this differential to receive the message.
Application of CAN in Control Technology
In control technology, CAN protocol has found a significant foothold due to its reliability and versatility.
One of its primary applications is in automotive systems.
Modern vehicles are equipped with a plethora of electronic control units (ECUs).
These units control everything from the engine and transmission to windows and seat adjustments.
CAN protocol enables seamless communication between these ECUs, ensuring real-time data sharing and efficient operation of the vehicle.
Beyond the automotive domain, CAN is extensively used in industrial automation systems.
In manufacturing plants, machinery often requires coordination to operate efficiently.
CAN protocol facilitates communication between various components of an automated assembly line, ensuring smooth operation and minimizing machine downtime.
This not only improves productivity but also reduces operational costs.
Aerospace is another area where CAN protocol is becoming increasingly popular.
In modern aircraft, having a reliable communication protocol is crucial.
CAN ensures that different systems such as navigation, monitoring, and control systems are in constant communication, enhancing both safety and performance.
The Role of CAN in Control Software Development
For software engineers developing control systems, understanding the CAN protocol is crucial.
At its core, CAN protocol simplifies the architecture of the system by reducing wiring complexities.
This modularity ensures that developers can add or remove devices without major overhauls to the network, making it adaptable to different use cases.
Software development for CAN requires adept knowledge in both embedded systems and network principles.
Engineers need to develop algorithms for efficient message handling, error detection, and correction.
The protocol’s error-checking capabilities are significant, as they maintain data integrity across the network.
Software engineers often utilize the CAN protocol’s built-in error management to create fault-tolerant systems that can catch and, in some circumstances, correct errors autonomously.
There are various software tools available today that facilitate CAN network setup and diagnostics.
These tools allow developers to simulate CAN networks, detect faults, and optimize performance.
Through again exploring advanced logging and diagnostic tools, developers can ensure their systems are robust and free from critical errors.
Challenges and Future Prospects of CAN Protocol
While the CAN protocol offers numerous benefits, it is not without its challenges.
One primary limitation is its maximum data transfer rate of 1 Mbps, which may not be sufficient for applications that require high bandwidth.
For such use cases, other protocols like Ethernet CAN or CAN FD (Flexible Data-rate) are gaining traction.
These variants offer higher data transfer rates while retaining the reliability CAN is known for.
Another challenge is addressing cybersecurity concerns.
As vehicles and industrial systems become more connected, the potential for malicious attacks over CAN networks increases.
It is imperative for developers to implement robust encryption and cybersecurity measures to protect CAN networks from unauthorized access and manipulation.
Looking ahead, the future of CAN protocol is promising with advancements like CAN FD.
CAN FD allows for frame lengths up to 64 bytes, compared to the 8 bytes supported by standard CAN, making it suitable for applications needing higher data throughput.
The simplicity, speed, and reliability of CAN, combined with these advancements, ensure that it will continue to be a vital protocol in control technology for years to come.
Conclusion
The CAN protocol remains a cornerstone in control technology and software development.
Its robust communication capabilities, error management, and adaptability make it ideal for automotive, industrial, and aerospace applications.
While there are challenges to overcome, particularly in terms of bandwidth and security, ongoing advancements continue to expand CAN’s potential.
As technology evolves, those proficient in CAN protocol will play a critical role in developing the next generation of control systems.
資料ダウンロード
QCD管理受発注クラウド「newji」は、受発注部門で必要なQCD管理全てを備えた、現場特化型兼クラウド型の今世紀最高の受発注管理システムとなります。
ユーザー登録
受発注業務の効率化だけでなく、システムを導入することで、コスト削減や製品・資材のステータス可視化のほか、属人化していた受発注情報の共有化による内部不正防止や統制にも役立ちます。
NEWJI DX
製造業に特化したデジタルトランスフォーメーション(DX)の実現を目指す請負開発型のコンサルティングサービスです。AI、iPaaS、および先端の技術を駆使して、製造プロセスの効率化、業務効率化、チームワーク強化、コスト削減、品質向上を実現します。このサービスは、製造業の課題を深く理解し、それに対する最適なデジタルソリューションを提供することで、企業が持続的な成長とイノベーションを達成できるようサポートします。
製造業ニュース解説
製造業、主に購買・調達部門にお勤めの方々に向けた情報を配信しております。
新任の方やベテランの方、管理職を対象とした幅広いコンテンツをご用意しております。
お問い合わせ
コストダウンが利益に直結する術だと理解していても、なかなか前に進めることができない状況。そんな時は、newjiのコストダウン自動化機能で大きく利益貢献しよう!
(β版非公開)