- お役立ち記事
- Impact of smart factories on quality control in the manufacturing industry and the role of the quality assurance department
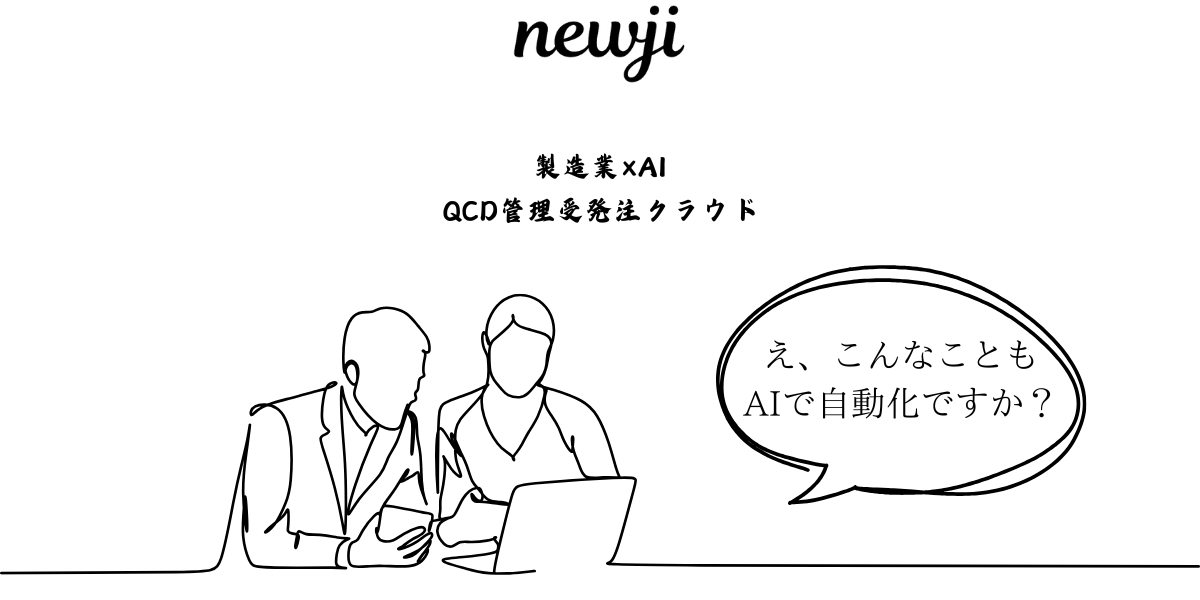
Impact of smart factories on quality control in the manufacturing industry and the role of the quality assurance department
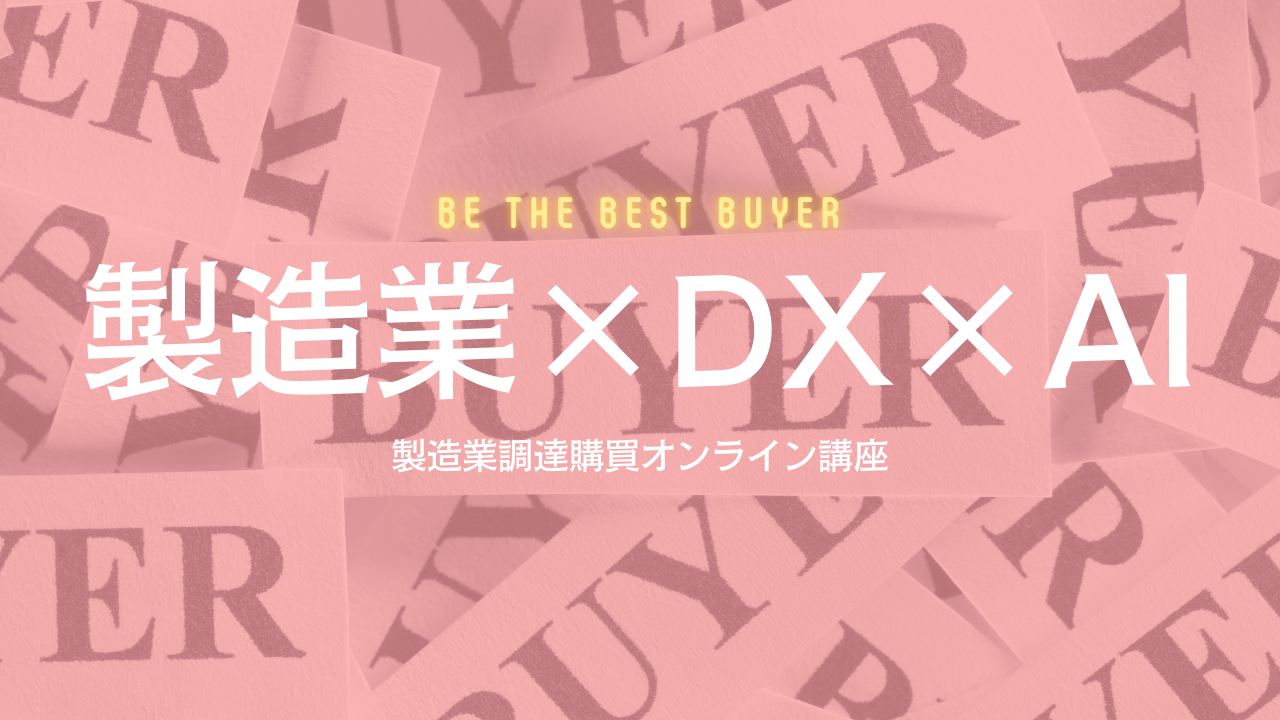
Quality control has always played an important role in manufacturing to ensure products are safe and meet specifications. However, the rise of smart factory technology is changing how quality is monitored and enforced on production lines. With automated systems taking on more tasks, the quality assurance department now focuses more on data analysis and oversight instead of direct inspection.
Smart factories utilize networked sensors, machines, software and analytics to streamline operations while improving visibility across the production process. Machines collect vast amounts of data on variables like temperature, pressure, vibration and more to monitor product and process quality in real-time. Any issues can be detected immediately rather than through occasional spot-checks. Early problem identification allows for quick corrective action to minimize waste.
Quality professionals have access to dashboards displaying live and historical sensor readings, machine performance metrics, product specifications and quality control limits. Powerful analytics can detect subtle patterns and predict problems before they occur. Rather than manually inspecting a sample of items, the entire production run is effectively being tested continuously. Problems that may have been missed can now be found through comprehensive data examination.
The data gives quality teams much deeper insight into how external factors like room temperature or machine wear impact product attributes. They can pinpoint root causes of defects that were previously unknown. Process parameters can be fine-tuned to minimize acceptable variability and maximize consistency. Statistical process control methods are applied to the vast sensor data to focus on reducing variations and improving process capability over time.
As machines communicate faults and maintenance needs to each other, planned and unplanned downtime is reduced. Quality assurance is involved in reviewing this equipment health data to address issues before they become quality problems. Their involvement ensures the predictive maintenance supported by Industry 4.0 technologies decreases defects and enhances product reliability.
With automated quality monitoring built into smart manufacturing, less direct inspection is required on the production line. Quality personnel can shift responsibilities from checking attributes and documentation to analyzing data trails and investigating anomalies. They play an advisory role focused on continuous process improvements based on insights from across the digital production environment.
While advanced technologies assume more quality responsibilities, there are still human factors critical to success. Quality specialists help workers understand new systems and leverage data/analytics tools more strategically. Over-reliance on automation without human verification can still result in quality escapes if anomalous data remains unexamined. Periodic audits where employees check samples are maintained as an extra safeguard against machine errors or cybersecurity threats.
Quality professionals also guide how non-conformances are addressed when issues do occur. For example, if variability increases in a process, they determine whether rework is acceptable or complete product recalls are necessary based on potential customer impact. Data governance policies are defined around retaining sensor measurements for traceability. Standards are set around data handling, visualization and alarming thresholds.
From an operational perspective, smart factory quality systems require less manpower on the shop floor yet more sophisticated roles managing digital quality programs. The enhanced data transparency drives culture changes as workers shift mindsets from transactional tasks to continual improvement through collaborative problem-solving. Success will rely on attracting talent proficient in data science, statistical methods, change management, as well as manufacturing fundamentals.
Quality 4.0 demands an educated, multi-disciplinary workforce. While advanced technologies augment human capabilities, quality results still stem from people. Smart factories change how quality assurance functions, not whether quality assurance is crucial. Looking ahead, the real impact will come from how organizations integrate systems with empowered workers to redefine excellence. When approached as a collaborative partnership between humans and machines, Quality 4.0 presents an immense opportunity to take operational effectiveness and customer satisfaction to an entirely new level.
資料ダウンロード
QCD調達購買管理クラウド「newji」は、調達購買部門で必要なQCD管理全てを備えた、現場特化型兼クラウド型の今世紀最高の購買管理システムとなります。
ユーザー登録
調達購買業務の効率化だけでなく、システムを導入することで、コスト削減や製品・資材のステータス可視化のほか、属人化していた購買情報の共有化による内部不正防止や統制にも役立ちます。
NEWJI DX
製造業に特化したデジタルトランスフォーメーション(DX)の実現を目指す請負開発型のコンサルティングサービスです。AI、iPaaS、および先端の技術を駆使して、製造プロセスの効率化、業務効率化、チームワーク強化、コスト削減、品質向上を実現します。このサービスは、製造業の課題を深く理解し、それに対する最適なデジタルソリューションを提供することで、企業が持続的な成長とイノベーションを達成できるようサポートします。
オンライン講座
製造業、主に購買・調達部門にお勤めの方々に向けた情報を配信しております。
新任の方やベテランの方、管理職を対象とした幅広いコンテンツをご用意しております。
お問い合わせ
コストダウンが利益に直結する術だと理解していても、なかなか前に進めることができない状況。そんな時は、newjiのコストダウン自動化機能で大きく利益貢献しよう!
(Β版非公開)