- お役立ち記事
- PCL programming in ROS development environment
月間93,089名の
製造業ご担当者様が閲覧しています*
*2025年6月30日現在のGoogle Analyticsのデータより
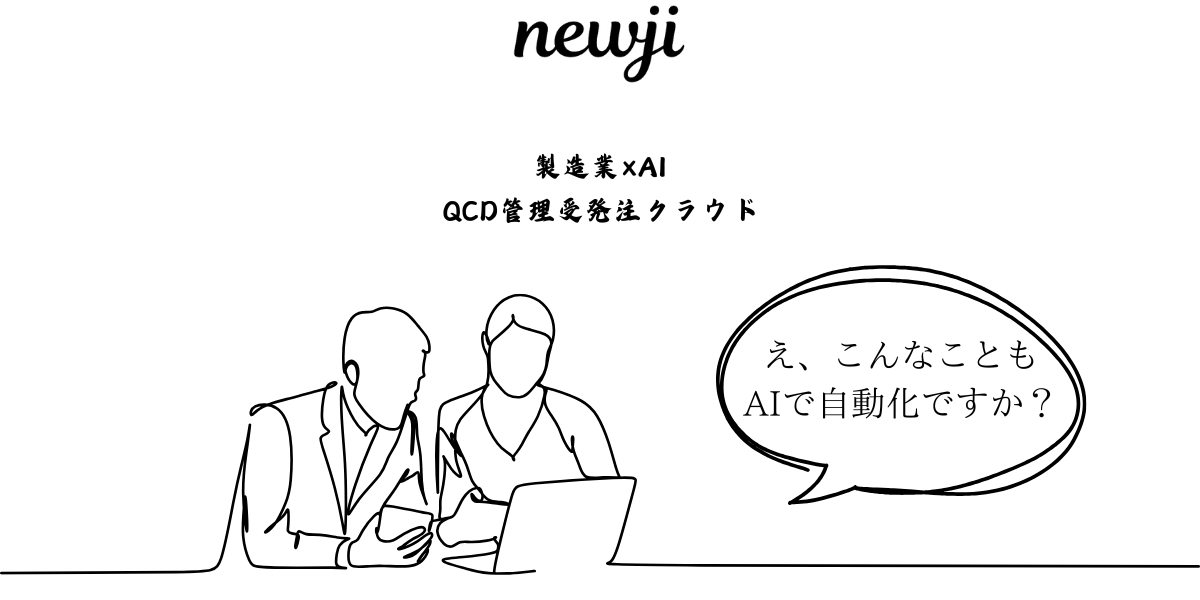
PCL programming in ROS development environment
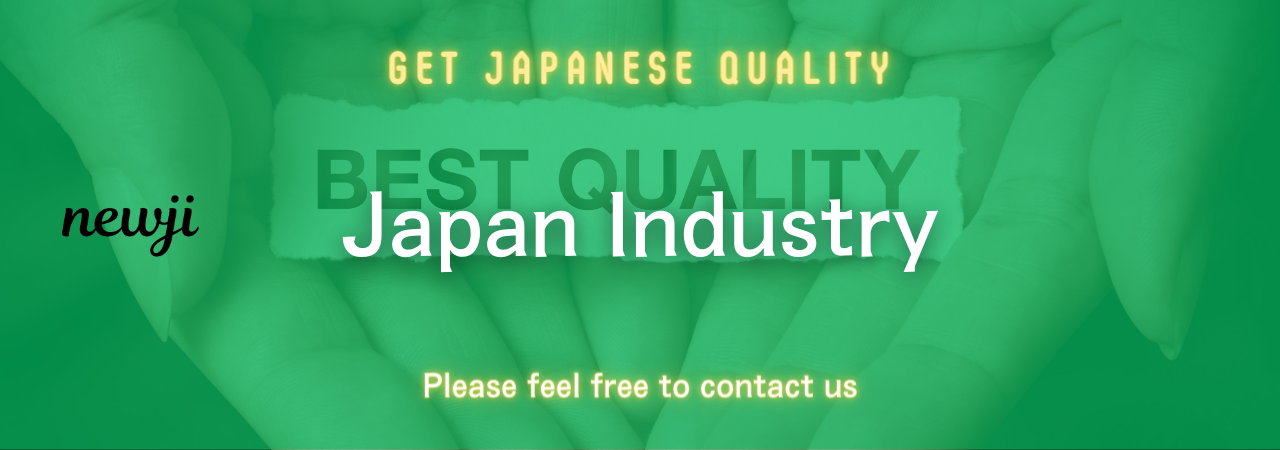
目次
Introduction to PCL Programming in ROS
PCL, or Point Cloud Library, is a powerful open-source library designed for processing 3D point cloud data.
When paired with the Robot Operating System (ROS), it offers robust tools and resources for developers working on robotics and automation projects.
Understanding how to integrate and utilize PCL within the ROS development environment can significantly elevate your robotics applications.
What is PCL?
PCL is a large-scale, open-source project tailored for 2D and 3D image and point cloud processing.
It contains algorithms for filtering, segmentation, registration, surface reconstruction, and many more operations.
Given its flexibility and expansive functionality, PCL is an essential tool for developers dealing with 3D data.
Key Features of PCL
– **Filtering:** Removing noise and unnecessary details from point clouds.
– **Segmentation:** Dividing a point cloud into useful parts, making data analysis and manipulation more manageable.
– **Registration:** Aligning point clouds to create complete models from partial data.
– **Surface Reconstruction:** Creating surfaces from point cloud data for a more detailed and accurate understanding of the environment.
– **Visualization:** Provides various ways to visualize point clouds for better interpretation and analysis of data.
Understanding ROS
The Robot Operating System (ROS) is a set of software libraries and tools that aid in building robot applications.
Think of it as the backbone for robotics development, offering essential features like device control, hardware abstraction, and inter-process communication.
An open-source initiative, ROS allows a wide range of developers and researchers to collaborate and advance robotics technology efficiently.
Core Components of ROS
– **Nodes:** Individual processes that perform computations. Nodes communicate with each other using messages.
– **Topics:** Channels used for sending and receiving messages between nodes.
– **Services:** Define request-response interactions between nodes for more complex tasks.
– **Packages:** Collections of files like libraries, nodes, and configurations that serve specific purposes in ROS.
Integrating PCL with ROS
Combining PCL with ROS makes handling 3D data in robotic systems more efficient and streamlined.
Here’s a step-by-step guide on how to integrate the two:
1. Setting Up the ROS Environment
Before beginning with PCL, ensure that ROS is installed and configured on your development machine.
This setup involves choosing a specific ROS distribution and following its installation instructions.
After installation, it’s crucial to set up an appropriate workspace for your projects, typically referred to as a catkin workspace.
2. Installing PCL
To use PCL in ROS, you need to have it installed on your system.
Most modern ROS distributions come with PCL as a built-in dependency, but it can also be installed manually.
You can install it using a package manager like apt on Ubuntu systems:
“`
sudo apt-get install libpcl-dev
“`
This command will fetch the necessary PCL libraries and dependencies.
3. Creating a ROS Package with PCL
Once ROS and PCL are in place, the next step is to create a ROS package that utilizes PCL.
Use the catkin tool to create a new package:
“`
catkin_create_pkg pcl_tutorial roscpp pcl_ros pcl_msgs
“`
This creates a package named `pcl_tutorial` that depends on `roscpp` and PCL libraries like `pcl_ros` and `pcl_msgs`.
4. Writing the Code
In your newly created package, create a `src` directory and write your PCL processing code using C++ or Python.
Include necessary headers provided by PCL and ROS to handle 3D point clouds.
Here’s a simple example in C++ to give you a basic understanding:
“`cpp
#include
#include
typedef pcl::PointCloud
int main(int argc, char** argv) {
ros::init(argc, argv, “pcl_example”);
ros::NodeHandle nh;
ros::Publisher pub = nh.advertise
PointCloud::Ptr cloud(new PointCloud);
cloud->header.frame_id = “map”;
cloud->height = 1;
cloud->width = 100;
cloud->points.resize(cloud->width * cloud->height);
for (auto& point : cloud->points) {
point.x = 1024 * rand() / (RAND_MAX + 1.0f);
point.y = 1024 * rand() / (RAND_MAX + 1.0f);
point.z = 1024 * rand() / (RAND_MAX + 1.0f);
}
ros::Rate loop_rate(1);
while (ros::ok()) {
cloud->header.stamp = ros::Time::now().toNSec() / 1000ull;
pub.publish(cloud);
ros::spinOnce();
loop_rate.sleep();
}
return 0;
}
“`
5. Building the Package
After writing your code, navigate to your catkin workspace and build the package:
“`
cd ~/catkin_ws
catkin_make
“`
This command compiles your package and ensures everything is linked correctly.
Benefits of Using PCL in ROS
– **Seamless Integration:** PCL’s seamless integration with ROS streamlines development processes, allowing for efficient handling of 3D data in robotic applications.
– **Comprehensive Libraries:** Access to robust libraries for a variety of tasks, from basic filtering to complex object recognition.
– **Active Community:** Both PCL and ROS boast active communities that provide support and constant updates, helping you stay ahead in your development work.
– **Enhanced Performance:** By leveraging the strengths of both PCL and ROS, developers can achieve high-performance applications that are scalable and adaptable to a range of robotics solutions.
Conclusion
Incorporating PCL programming within the ROS development environment can greatly enhance your ability to work with 3D data in robotics.
With the proper setup and understanding, utilizing these powerful tools becomes a straightforward part of the development process.
Whether you’re new to robotics or an experienced developer, mastering PCL in ROS can significantly impact your projects’ quality and capabilities.
資料ダウンロード
QCD管理受発注クラウド「newji」は、受発注部門で必要なQCD管理全てを備えた、現場特化型兼クラウド型の今世紀最高の受発注管理システムとなります。
ユーザー登録
受発注業務の効率化だけでなく、システムを導入することで、コスト削減や製品・資材のステータス可視化のほか、属人化していた受発注情報の共有化による内部不正防止や統制にも役立ちます。
NEWJI DX
製造業に特化したデジタルトランスフォーメーション(DX)の実現を目指す請負開発型のコンサルティングサービスです。AI、iPaaS、および先端の技術を駆使して、製造プロセスの効率化、業務効率化、チームワーク強化、コスト削減、品質向上を実現します。このサービスは、製造業の課題を深く理解し、それに対する最適なデジタルソリューションを提供することで、企業が持続的な成長とイノベーションを達成できるようサポートします。
製造業ニュース解説
製造業、主に購買・調達部門にお勤めの方々に向けた情報を配信しております。
新任の方やベテランの方、管理職を対象とした幅広いコンテンツをご用意しております。
お問い合わせ
コストダウンが利益に直結する術だと理解していても、なかなか前に進めることができない状況。そんな時は、newjiのコストダウン自動化機能で大きく利益貢献しよう!
(β版非公開)