- お役立ち記事
- Preventing Production Troubles with Machining Simulation
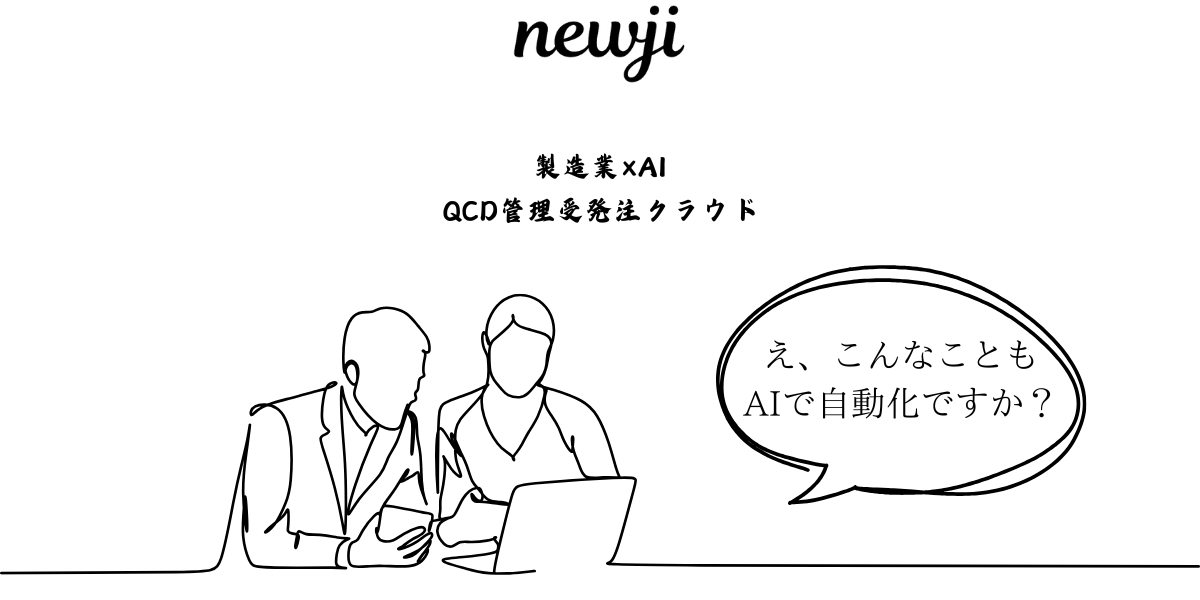
Preventing Production Troubles with Machining Simulation
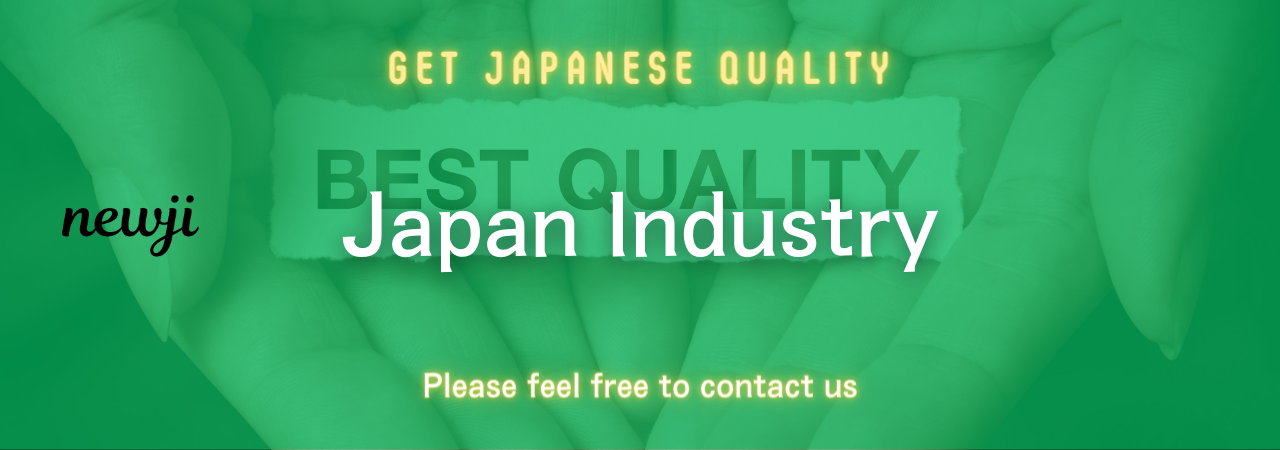
In the world of manufacturing, ensuring the smooth production of parts and components is crucial.
Machining simulation is a powerful tool that helps manufacturers prevent production troubles before they become costly issues.
Let’s dive into how machining simulation works and why it’s an essential part of modern manufacturing.
目次
What is Machining Simulation?
Machining simulation is a digital process that replicates the actions of machining tools and equipment on a computer.
This technology enables engineers and machinists to visualize and analyze the entire machining process before it even begins on the shop floor.
Through simulation, users can see how different tools interact with the material, allowing them to identify potential problems and inefficiencies.
Why is Machining Simulation Important?
The importance of machining simulation cannot be overstated.
It serves as a proactive approach to production, helping manufacturers avoid unexpected problems that can delay production schedules and increase costs.
Here are some key reasons why machining simulation is crucial:
Detecting Errors Early
One of the primary benefits of machining simulation is its ability to detect errors and issues at an early stage.
By simulating the machining process, engineers can spot potential clashes, tool overloading, and other problems that could lead to defective parts.
Identifying these issues early allows for adjustments to be made before the actual manufacturing begins, saving time and resources.
Improving Tool Life
Proper tool usage is vital for maintaining efficiency and reducing costs in manufacturing.
Machining simulation helps identify the best cutting strategies and tool paths, which can significantly improve tool life.
By optimizing the conditions under which tools operate, simulation ensures that they wear out less quickly, leading to fewer replacements and reduced downtime.
Enhancing Precision and Quality
Precision is key in machining.
Machining simulation allows for the fine-tuning of manufacturing processes to achieve the highest quality standards.
By analyzing tool paths and cutting strategies, engineers can ensure that the final parts meet the desired specifications and tolerances.
This leads to higher-quality products and increased customer satisfaction.
How Machining Simulation Works
To understand how machining simulation works, it’s essential to break down its core components and processes.
CAD and CAM Integration
Computer-Aided Design (CAD) and Computer-Aided Manufacturing (CAM) are integral to the machining simulation process.
CAD software is used to create 3D models of the parts to be manufactured, while CAM software translates these models into detailed instructions for the machining tools.
Machining simulation bridges the gap between these two technologies by creating a virtual environment where the CAD models and CAM instructions can be tested and optimized.
Virtual Machining Environment
In the virtual machining environment, a digital representation of the workshop and machinery is created.
This includes the workpiece, tools, and machines that will be used in the actual production process.
The simulation software performs a series of tests and analyses to determine how the tools interact with the material and identify any potential problems.
Tool Path Verification
One of the most critical aspects of machining simulation is tool path verification.
The simulation software generates the tool paths based on the CAM instructions and tests them in the virtual environment.
During this process, the software checks for collisions, gouges, and errors that could affect the final product.
Optimization and Adjustment
Once potential issues are identified, the simulation software allows engineers to make necessary adjustments.
This could involve changing tool paths, adjusting feed rates, or selecting different tools.
By fine-tuning these parameters, the risk of errors and defects is significantly reduced.
The Benefits of Using Machining Simulation
Utilizing machining simulation in a production environment brings numerous benefits beyond just error detection and prevention.
Cost Savings
One of the most tangible benefits of machining simulation is cost savings.
By identifying and correcting issues before they arise on the shop floor, manufacturers can avoid costly reworks, scrapped parts, and production delays.
Additionally, optimizing tool paths and cutting strategies reduces tool wear, further cutting down on expenses.
Increased Efficiency
Machining simulation helps streamline the production process by ensuring everything is optimized and running smoothly.
This leads to shorter production times and more efficient use of resources, resulting in increased overall productivity.
Improved Safety
By detecting potential collisions and tool overloads, machining simulation enhances workplace safety.
Preventing these issues before they occur reduces the risk of accidents and equipment damage, creating a safer working environment for employees.
Flexibility and Adaptability
Machining simulation provides manufacturers with the flexibility to test different scenarios and strategies without impacting actual production.
This adaptability allows for rapid changes and improvements to be made, ensuring the production process remains efficient and effective.
Case Study: Machining Simulation in Action
To illustrate the impact of machining simulation, let’s look at a real-world example of a company that successfully implemented this technology.
Company Background
XYZ Manufacturing, a leading producer of aerospace components, faced significant challenges with production delays and high scrap rates.
The complex geometries and tight tolerances of their parts presented difficulties that often led to tool breakages and defective products.
Implementing Machining Simulation
XYZ Manufacturing decided to integrate machining simulation into their production process.
They began by using advanced CAD/CAM software to create detailed 3D models and generated precise tool paths.
The simulation software was then used to verify and optimize these paths, identifying and eliminating potential collisions and issues.
Results and Benefits
The impact of machining simulation on XYZ Manufacturing was immediate and significant.
They experienced a substantial reduction in production delays and scrap rates, leading to considerable cost savings.
Tool life improved, and the overall quality of their components increased, resulting in greater customer satisfaction.
Conclusion
Machining simulation is an indispensable tool for modern manufacturing.
By identifying potential problems and optimizing processes before production begins, it helps prevent costly issues and ensures high-quality output.
From saving costs and improving efficiency to enhancing safety and flexibility, the benefits of machining simulation are vast.
Manufacturers who embrace this technology position themselves for success in an increasingly competitive industry.
資料ダウンロード
QCD調達購買管理クラウド「newji」は、調達購買部門で必要なQCD管理全てを備えた、現場特化型兼クラウド型の今世紀最高の購買管理システムとなります。
ユーザー登録
調達購買業務の効率化だけでなく、システムを導入することで、コスト削減や製品・資材のステータス可視化のほか、属人化していた購買情報の共有化による内部不正防止や統制にも役立ちます。
NEWJI DX
製造業に特化したデジタルトランスフォーメーション(DX)の実現を目指す請負開発型のコンサルティングサービスです。AI、iPaaS、および先端の技術を駆使して、製造プロセスの効率化、業務効率化、チームワーク強化、コスト削減、品質向上を実現します。このサービスは、製造業の課題を深く理解し、それに対する最適なデジタルソリューションを提供することで、企業が持続的な成長とイノベーションを達成できるようサポートします。
オンライン講座
製造業、主に購買・調達部門にお勤めの方々に向けた情報を配信しております。
新任の方やベテランの方、管理職を対象とした幅広いコンテンツをご用意しております。
お問い合わせ
コストダウンが利益に直結する術だと理解していても、なかなか前に進めることができない状況。そんな時は、newjiのコストダウン自動化機能で大きく利益貢献しよう!
(Β版非公開)