- お役立ち記事
- Revolutionizing Japanese Manufacturing: The Role of AGVs (Automated Guided Vehicles) and AMRs (Autonomous Mobile Robots)
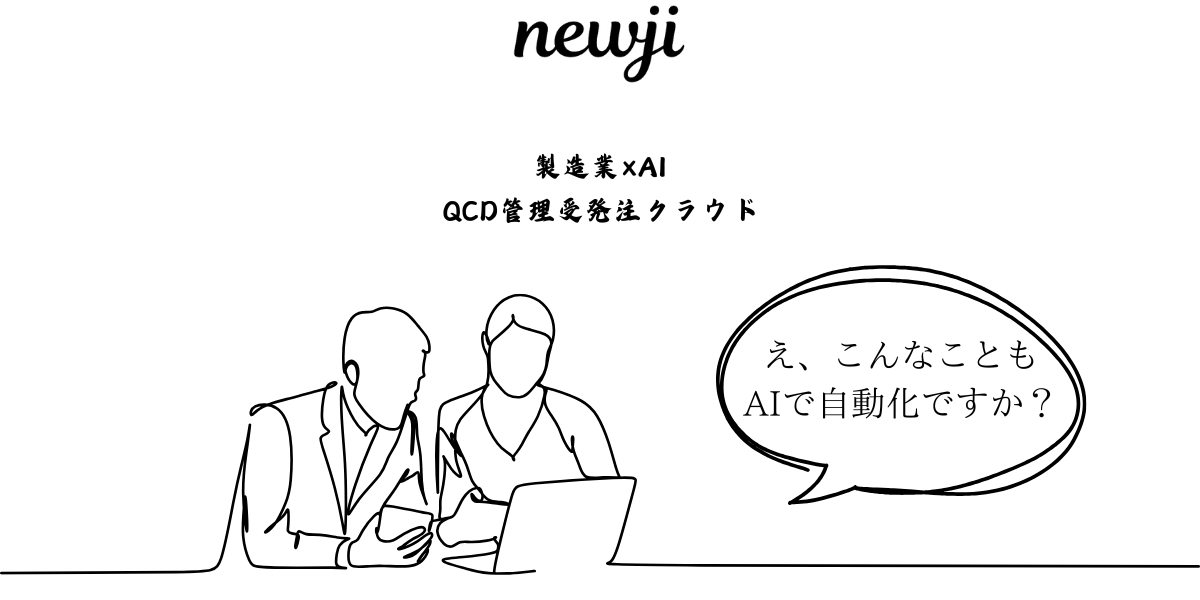
Revolutionizing Japanese Manufacturing: The Role of AGVs (Automated Guided Vehicles) and AMRs (Autonomous Mobile Robots)
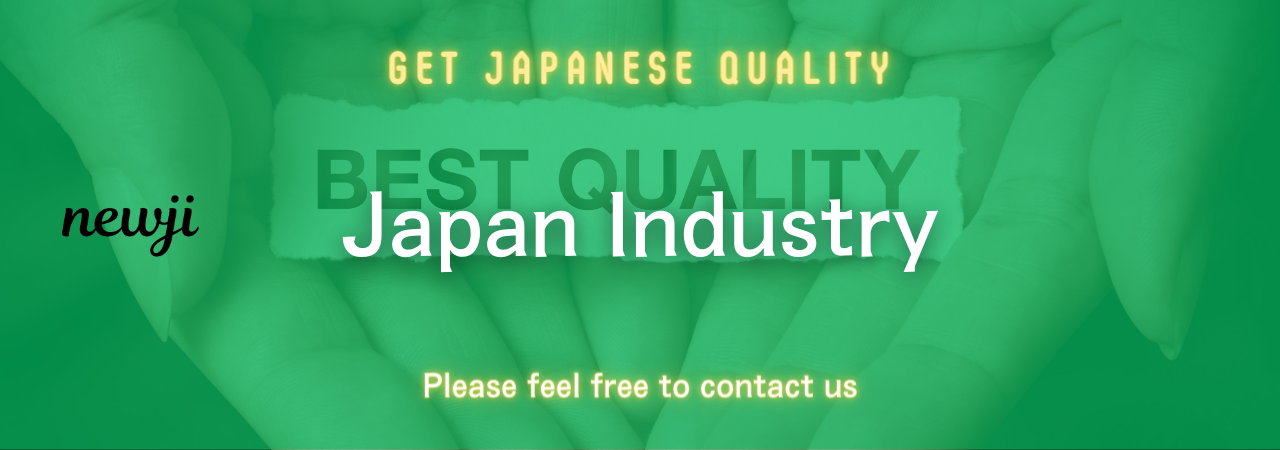
目次
Introduction
Japanese manufacturing has long been recognized for its precise quality control, efficient production processes, and robust supplier networks.
As global competition intensifies, there is an increasing demand to enhance productivity and optimize operations further.
A critical enabler in this quest is the adoption of advanced technologies, particularly Automated Guided Vehicles (AGVs) and Autonomous Mobile Robots (AMRs).
AGVs and AMRs represent a significant shift in the traditional landscape of manufacturing.
By automating material handling, inventory transport, and workflow coordination, these technologies bring unprecedented efficiency, reliability, and flexibility to the industrial environment.
This article delves deep into the role of AGVs and AMRs within the context of Japanese manufacturing, providing practical insights from procurement and purchasing perspectives, as well as evaluating their advantages, disadvantages, and best practices for successful implementation.
Understanding AGVs and AMRs
What are AGVs?
Automated Guided Vehicles (AGVs) are mobile robots designed to follow predefined paths within a manufacturing facility or warehouse.
They utilize technologies such as magnetic strips, lasers, or optical sensors to navigate and transport materials from one location to another efficiently.
AGVs have been in use since the 1950s and have evolved dramatically over the years to include various models such as tuggers, unit load carriers, forklifts, and others tailored to specific needs.
What are AMRs?
Autonomous Mobile Robots (AMRs) represent the next generation of material handling robots.
Unlike AGVs, AMRs do not require predefined paths and can navigate dynamically using sensor fusion, machine vision, and advanced algorithms.
They can adapt to changes in their environment, making real-time decisions, and optimizing routes for greater efficiency.
This flexibility makes AMRs particularly suitable for more complex and dynamic manufacturing settings.
Advantages of AGVs and AMRs in Japanese Manufacturing
Increased Efficiency and Productivity
One of the most notable benefits of integrating AGVs and AMRs into manufacturing processes is the significant increase in efficiency and productivity.
These robots work tirelessly without breaks, reducing the dependency on human labor for repetitive tasks.
By automating material transport, manufacturers can ensure a constant and smooth flow of materials, minimizing bottlenecks and downtime.
Enhanced Safety
Worker safety is a paramount concern in manufacturing.
AGVs and AMRs are equipped with advanced sensors and safety protocols that minimize the risk of accidents and injuries.
They can detect obstacles, stop automatically to avoid collisions, and navigate safely around factory floors.
This reduces the likelihood of workplace accidents, contributing to a safer working environment.
Improved Inventory Management
With the ability to transport materials precisely and consistently, AGVs and AMRs can play a critical role in improving inventory management.
They ensure that raw materials, components, and finished goods are always accurately placed at designated locations.
This improved precision reduces errors, lowers inventory costs, and enhances overall operational efficiency.
Cost Reduction
While the initial investment in AGVs and AMRs can be substantial, the long-term cost savings are considerable.
By reducing labor costs, minimizing errors, and optimizing operational efficiency, these robots can lead to significant cost reductions over time.
Additionally, their ability to operate 24/7 can lead to higher utilization rates and increased output.
Disadvantages and Challenges
High Initial Investment
The most apparent drawback of implementing AGVs and AMRs is the high initial cost.
The purchase, installation, and integration of these robots require significant capital investment.
For small and medium-sized enterprises, this financial barrier can be difficult to overcome.
Complex Integration
Integrating AGVs and AMRs into existing manufacturing systems can be complex.
It often requires reconfiguring the production layout, updating software systems, and ensuring compatibility with various equipment.
This integration process can be time-consuming and necessitates specialized expertise.
Maintenance and Upkeep
While AGVs and AMRs are generally reliable, they require regular maintenance to ensure optimal performance.
This includes software updates, hardware repairs, and routine inspections.
Manufacturers must invest in the necessary resources and training to maintain these systems effectively.
Adaptation to Specific Needs
Every manufacturing facility has unique requirements and constraints.
Customizing AGVs and AMRs to meet specific operational needs can be challenging and may require bespoke solutions.
This can further escalate costs and complexity in adoption.
Supplier Negotiation Techniques
When procuring AGVs and AMRs, effective negotiation with suppliers is crucial.
Understanding Supplier Capabilities
Before entering into negotiations, thoroughly research potential suppliers to understand their capabilities, technology offerings, and support services.
Engage with multiple suppliers to compare features, pricing, and post-sales support.
Specify Requirements Clearly
Ensure that your requirements are clearly defined and communicated to suppliers.
This includes the specifics of your manufacturing environment, the type of materials to be handled, transport distances, and any customizations needed.
Negotiate Total Cost of Ownership
While the initial purchase price is significant, it’s essential to consider the total cost of ownership (TCO), including maintenance, software updates, training, and potential upgrades.
Negotiate comprehensive service agreements that cover these aspects to avoid unexpected expenses in the future.
Request Demonstrations and Pilots
Request on-site demonstrations and pilot projects to evaluate the performance of AGVs and AMRs in your specific environment.
This gives you valuable insights into their effectiveness and allows you to address any potential issues before full-scale deployment.
Ensure Scalability
Consider the scalability of the AGV or AMR solutions.
Ensure that the technology can be expanded or upgraded as your operational needs grow.
Negotiate terms that allow for easy scalability and future enhancements.
Market Conditions and Trends
The market for AGVs and AMRs is experiencing rapid growth, fueled by advancements in technology and increasing demand for automation.
Technological Advancements
Continuous innovation in sensor technology, artificial intelligence, and machine learning is driving significant improvements in the capabilities of AGVs and AMRs.
These advancements are making the robots smarter, more efficient, and adaptable to various environments.
Increasing Adoption in SMEs
With the decreasing costs of technology and the availability of flexible financing options, small and medium-sized enterprises (SMEs) are increasingly adopting AGVs and AMRs to enhance their competitiveness.
This trend is expected to continue as more affordable solutions become available.
Focus on Customization
Manufacturers are demanding more customized solutions that cater to their unique operational requirements.
Suppliers are responding by offering tailored AGVs and AMRs that can be configured according to specific needs, further driving adoption.
Integration with IoT and Industry 4.0
The integration of AGVs and AMRs with the Internet of Things (IoT) and Industry 4.0 technologies is creating smart, connected factories.
This synergy enhances data sharing, real-time monitoring, and predictive maintenance, leading to more efficient and intelligent operations.
Best Practices for Implementing AGVs and AMRs
For a successful implementation of AGVs and AMRs, manufacturers should follow best practices that encompass planning, execution, and continuous improvement.
Conduct a Thorough Needs Assessment
Begin with a comprehensive assessment of your operational needs.
Identify the specific areas where AGVs and AMRs can add the most value, considering factors such as material handling requirements, workflow patterns, and the existing layout.
Develop a Detailed Implementation Plan
Create a detailed implementation plan that outlines the steps, timeline, resources, and budget.
Include provisions for pilot testing, integration, training, and a phased deployment to ensure a smooth transition.
Engage Stakeholders Early
Engage key stakeholders, including management, operations, maintenance, and IT teams, early in the process.
Their buy-in and support are crucial for successful implementation and ongoing operation.
Invest in Training and Support
Provide comprehensive training for your staff on the operation, maintenance, and troubleshooting of AGVs and AMRs.
Ensure that you have access to reliable technical support from your suppliers.
Monitor and Optimize Performance
Continuously monitor the performance of your AGVs and AMRs using key performance indicators (KPIs) such as uptime, transport accuracy, and cost savings.
Use this data to identify areas for improvement and optimize your operations.
Conclusion
The role of AGVs and AMRs in revolutionizing Japanese manufacturing cannot be overstated.
These advanced technologies significantly enhance efficiency, safety, and productivity, helping manufacturers meet the challenges of global competition.
While the initial investment and complexity of integration present challenges, the long-term benefits far outweigh these drawbacks.
By adopting best practices, engaging in effective supplier negotiations, and leveraging the latest market trends, manufacturers can successfully implement AGVs and AMRs to transform their operations.
As technology continues to evolve, the integration of AGVs and AMRs will become increasingly crucial in maintaining a competitive edge in the manufacturing landscape.
The journey towards automation is not merely an option but a strategic imperative for Japanese manufacturing to sustain its legacy of excellence.
資料ダウンロード
QCD調達購買管理クラウド「newji」は、調達購買部門で必要なQCD管理全てを備えた、現場特化型兼クラウド型の今世紀最高の購買管理システムとなります。
ユーザー登録
調達購買業務の効率化だけでなく、システムを導入することで、コスト削減や製品・資材のステータス可視化のほか、属人化していた購買情報の共有化による内部不正防止や統制にも役立ちます。
NEWJI DX
製造業に特化したデジタルトランスフォーメーション(DX)の実現を目指す請負開発型のコンサルティングサービスです。AI、iPaaS、および先端の技術を駆使して、製造プロセスの効率化、業務効率化、チームワーク強化、コスト削減、品質向上を実現します。このサービスは、製造業の課題を深く理解し、それに対する最適なデジタルソリューションを提供することで、企業が持続的な成長とイノベーションを達成できるようサポートします。
オンライン講座
製造業、主に購買・調達部門にお勤めの方々に向けた情報を配信しております。
新任の方やベテランの方、管理職を対象とした幅広いコンテンツをご用意しております。
お問い合わせ
コストダウンが利益に直結する術だと理解していても、なかなか前に進めることができない状況。そんな時は、newjiのコストダウン自動化機能で大きく利益貢献しよう!
(Β版非公開)