- お役立ち記事
- The Key to Productivity Improvement Fusion of Lean Manufacturing and Digital
The Key to Productivity Improvement Fusion of Lean Manufacturing and Digital
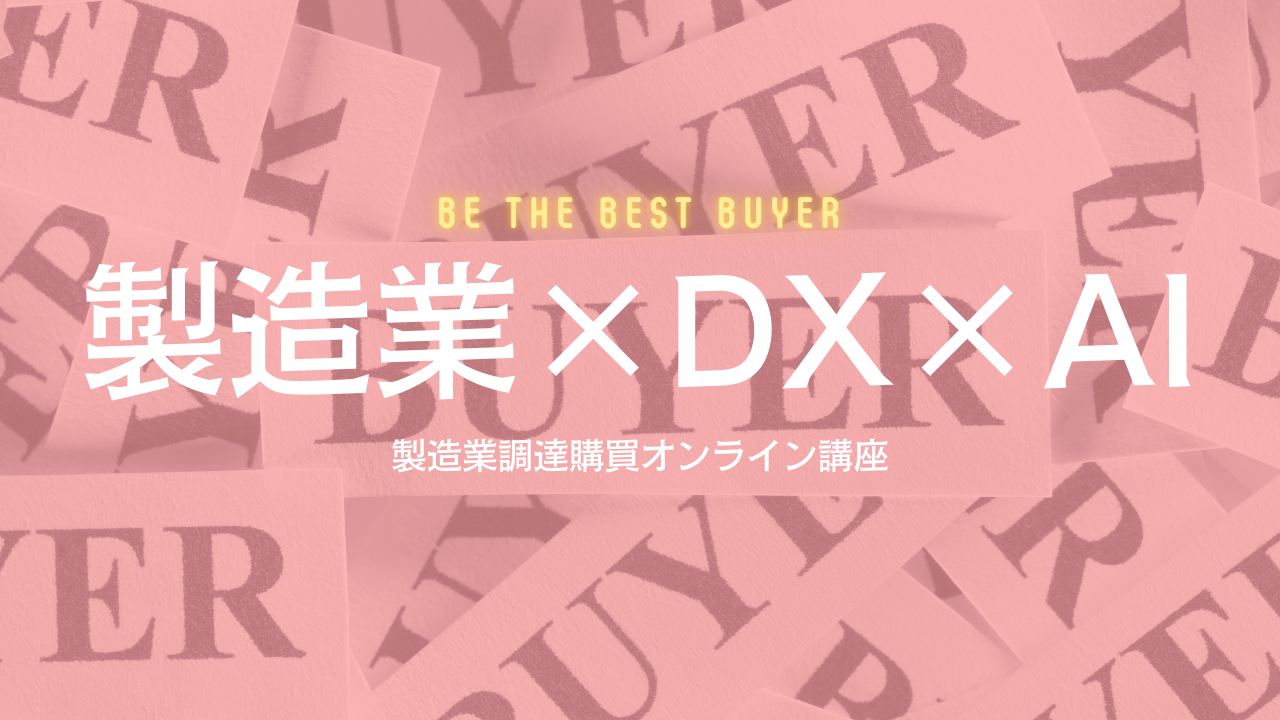
Lean manufacturing and digital technologies have become increasingly important for businesses seeking to streamline processes and improve productivity. When these two approaches are combined, they form a powerful method known as Lean Digital that can unlock new efficiencies and drive significant results.
Lean manufacturing focuses on eliminating waste from all areas of operations. Some of the core principles of Lean include just-in-time production, continuous process improvement, standard workflows, and visual management. The goal is to optimize value stream processes and flow so the right things are made in the right quantities at the right time with minimal excess inventory or motion. Digital technologies take Lean to the next level by enhancing areas like data collection, analysis, and communication.
Sensors and IoT devices can provide real-time visibility into production operations that wasn’t possible before. Tools like RFID tracking allow components and materials to be monitored as they move through different stages. This level of visibility helps identify bottlenecks or issues the moment they occur rather than after significant waste has already been generated. The data collected from devices on the factory floor feeds into analytics platforms where it can be studied to reveal optimization opportunities. Performance metrics become more robust and accurate with digital tools continuously monitoring KPIs.
Areas primed for data-driven improvement include inventory and supply chain management. By applying analytics to visibility data from warehouses and distribution centers, inventory levels can be reduced through more accurate demand signal and replenishment. This eliminates overstocking and stockouts while maintaining excellent customer fulfillment rates. Shipping and logistics operations also benefit through optimized routing, load optimization, and real-time tracking of assets. Digital supply chain twins simulate scenarios to test improvements before implementation as well.
On the production line, sensors in machines feed metadata that offers new insights into overall equipment effectiveness. Unplanned downtime can be dramatically reduced by predicting maintenance needs through anomaly detection and machine diagnostics. Process control is optimized by monitoring production data and automatically adjusting parameters when quality deviates from specifications. Resources like labor hours are freed up as automation takes over mundane and repetitive tasks through robotic process automation.
Adopting advanced manufacturing technologies like 3D printing, CNC machining, robotics, and more aligns with the Lean principles of one-piece flow and just-in-time manufacturing. These technologies offer on-demand, customized production that avoids overproduction waste. They also facilitate innovative product designs not possible with conventional manufacturing methods, allowing companies to gain competitive advantage through differentiated offerings.
Organizations embracing the fusion of Lean and digital see measurable results across various fronts. One company implemented an Industrial Internet of Things (IIoT) system across its facilities to unify operations on a common digital backbone. This enabled real-time production monitoring, predictive quality control, and automatic data collection that was previously a manual burden. Resource utilization went up 30% while inventory carrying costs decreased 20% through optimized scheduling and replenishment. Another manufacturer digitized work instructions and work flows to standardize processes enterprise-wide. This eliminated rework waste and non-value-added tasks, freeing a net savings of over $3 million annually.
Transitioning to a Lean Digital model requires an enterprise-wide change in mindset and culture as well as strategic investments. Companies must develop core competencies in areas like data science, automation engineering, cloud computing, and digital transformation. Skills gaps must be addressed through recruiting initiatives or reskilling current employees. Technologies supporting the digital thread like MES, ML, and analytics platforms must be implemented in an integrated way. Change management is also paramount to drive adoption across departments and foster collaboration between IT, engineering, and operational teams. With the proper groundwork laid, businesses are able to build a future-proof foundation for productivity, efficiency, quality, and competitiveness through the synergistic combination of Lean thinking and digital muscle.
In summary, combining Lean manufacturing principles with digital technologies forms a powerful methodology known as Lean Digital for driving breakthroughs in operations, processes, inventory management, equipment uptime, quality control and more. Data-driven visibility and automation unlocks new levels of waste elimination while advanced manufacturing techniques facilitate customized one-piece flow. Companies establishing competency in this fusion approach see significant impacts like 30% higher resource utilization, 20% lower inventory costs, and multi-million dollar annual savings through standardized work and rework reduction. Transitioning requires investment, change management focus, and multidisciplinary skill development – but for manufacturers seeking to future-proof operations, Lean Digital presents a compelling path forward.
資料ダウンロード
QCD調達購買管理クラウド「newji」は、調達購買部門で必要なQCD管理全てを備えた、現場特化型兼クラウド型の今世紀最高の購買管理システムとなります。
ユーザー登録
調達購買業務の効率化だけでなく、システムを導入することで、コスト削減や製品・資材のステータス可視化のほか、属人化していた購買情報の共有化による内部不正防止や統制にも役立ちます。
NEWJI DX
製造業に特化したデジタルトランスフォーメーション(DX)の実現を目指す請負開発型のコンサルティングサービスです。AI、iPaaS、および先端の技術を駆使して、製造プロセスの効率化、業務効率化、チームワーク強化、コスト削減、品質向上を実現します。このサービスは、製造業の課題を深く理解し、それに対する最適なデジタルソリューションを提供することで、企業が持続的な成長とイノベーションを達成できるようサポートします。
オンライン講座
製造業、主に購買・調達部門にお勤めの方々に向けた情報を配信しております。
新任の方やベテランの方、管理職を対象とした幅広いコンテンツをご用意しております。
お問い合わせ
コストダウンが利益に直結する術だと理解していても、なかなか前に進めることができない状況。そんな時は、newjiのコストダウン自動化機能で大きく利益貢献しよう!
(Β版非公開)