- お役立ち記事
- Unparalleled Punctuality! Japanese Manufacturing Delivers at World-Record Speed
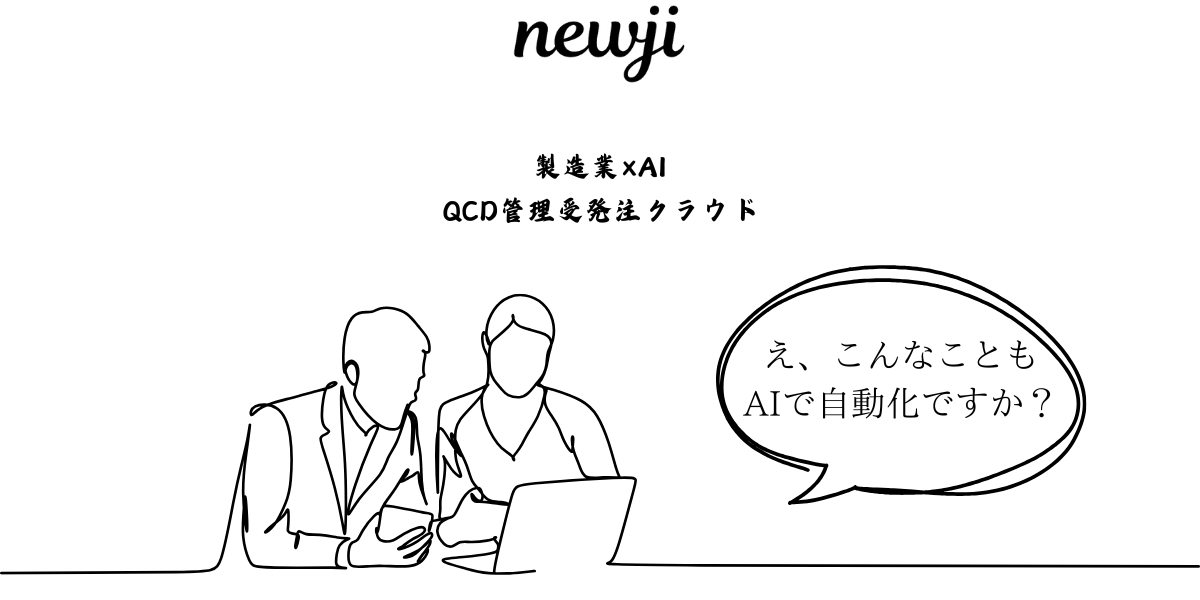
Unparalleled Punctuality! Japanese Manufacturing Delivers at World-Record Speed
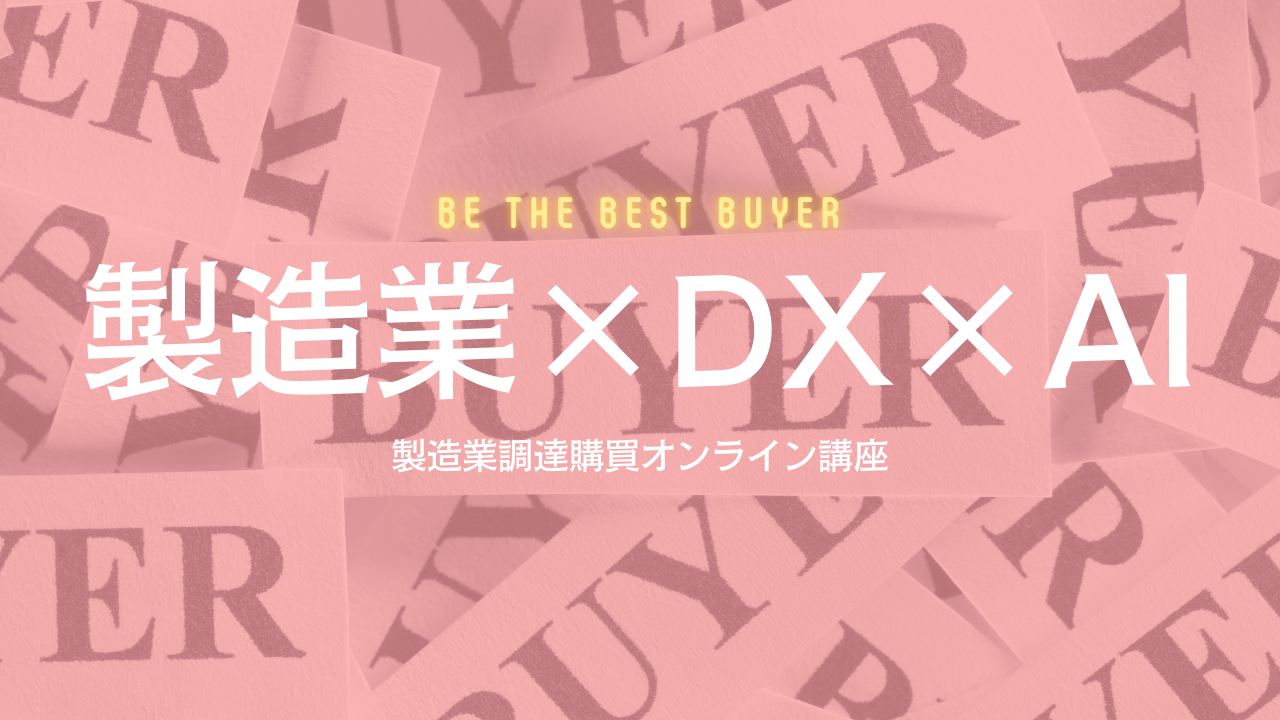
Japanese manufacturing has long been renowned for its incredible efficiency and precise timeliness. This reputation is well-earned, as Japan consistently achieves world-record turnaround times in areas like electronics, automotive, and industrial production.
At the heart of Japan’s punctual prowess is its deeply ingrained work culture of kaizen, which translates to “continuous improvement.” Through kaizen, Japanese companies are constantly analyzing workflows, identifying inefficiencies, and instituting small changes to shave off seconds here and minutes there. This relentless optimization mindset allows even marginal speed increases to compound over time into substantial productivity gains.
A prime example is Toyota, the world’s largest automaker. Toyota is famous for its just-in-time manufacturing system, where parts are delivered to the assembly line right when they are needed and no sooner. This lean approach eliminates wasteful inventory storage costs and enables rapid adjustments to fluctuating demand signals. Toyota can ramp up or ramp down production frequently within the same day, and shift between vehicle models even more quickly.
The Toyota Production System involves countless small innovations, like color-coding machine controls so workers can intuitively operate any station, and having electronic tags on each part that track its progress through the plant in real-time. A result is that Toyota can bring a new car from design to production start in just 36 months – around half the industry average. This level of flexibility and agility gives Toyota a major competitive edge.
Similarly, electronics giant Sony is renowned for being able to deliver new game consoles, TVs, cameras and other devices within impossibly tight windows. Sony’s plants employ techniques like single-minute exchange of dies (SMED) to radically shorten changeover times between product runs. This allows Sony to nimbly respond to ever-shifting consumer tastes and technological innovations without getting stuck with outdated inventory.
Another Japanese manufacturing trailblazer is the robotics company Fanuc. Its industrial robots are celebrated for setting world speed and precision records in lab tests and real-world applications alike. In one demonstration, a Fanuc robot achieved a mind-boggling cycle time of just 0.106 seconds to grab, move and place a part – the equivalent of assembling over 5,700 components per hour. This superhuman dexterity stems from Fanuc’s focus on fast, fluid mechanics as well as its proprietary motion control systems.
Yet delivering at such breakneck turnaround times requires more than just technological prowess – it demands rigorously streamlined business processes as well. For instance, Japanese auto parts suppliers have close relationships with automakers where orders are placed and parts delivered on very short lead times, sometimes only a few hours in advance. Suppliers also hold minimal inventory andinstead manufacture goods “just in time” upon receiving orders.
Japanese manufacturers likewise expect punctuality from their own suppliers. A parts delay of even a few minutes can cause an entire assembly line to grind to a halt. So tier 1 suppliers in turn place similarly tight time demands on their own tier 2 partners. This cascading effect of prioritizing promptness creates an entire manufacturing ecosystem built for optimal velocity.
Of course, achieving world-record speed also depends on human factors like employee skills and workplace culture. Japanese companies invest heavily in training production employees and empowering them to continuously improve processes. For example, auto workers undergo months of practice to learn how to seamlessly perform every duty on the line. They are then encouraged to propose production enhancements through quality circles and other participatory initiatives.
This emphasis on developing versatile, solutions-oriented workers produces assembly teams that can respond nimbly to unexpected issues. Meanwhile, Japanese companies foster strong esprit de corps to motivate individuals striving as a coordinated unit towards shared goals like punctuality and quality. Line stoppages are viewed not just as technical problems but as failures of the entire team effort.
In summary, Japanese manufacturing’s emphasis on kaizen, precision engineering, lean processes, cooperative supplier networks and highly skilled labor all synergize to achieve some of the fastest turnaround times on earth. This unparalleled punctuality gives Japanese brands a vital edge for competitiveness and market leadership. It also demonstrates that obsessively shaving even seconds off production can, in aggregate, disrupt entire industries and global flows of commerce. The lessons of Toyota, Sony, Fanuc and other role models continue inspiring manufacturers worldwide in their ongoing quests for maximized velocity.
資料ダウンロード
QCD調達購買管理クラウド「newji」は、調達購買部門で必要なQCD管理全てを備えた、現場特化型兼クラウド型の今世紀最高の購買管理システムとなります。
ユーザー登録
調達購買業務の効率化だけでなく、システムを導入することで、コスト削減や製品・資材のステータス可視化のほか、属人化していた購買情報の共有化による内部不正防止や統制にも役立ちます。
NEWJI DX
製造業に特化したデジタルトランスフォーメーション(DX)の実現を目指す請負開発型のコンサルティングサービスです。AI、iPaaS、および先端の技術を駆使して、製造プロセスの効率化、業務効率化、チームワーク強化、コスト削減、品質向上を実現します。このサービスは、製造業の課題を深く理解し、それに対する最適なデジタルソリューションを提供することで、企業が持続的な成長とイノベーションを達成できるようサポートします。
オンライン講座
製造業、主に購買・調達部門にお勤めの方々に向けた情報を配信しております。
新任の方やベテランの方、管理職を対象とした幅広いコンテンツをご用意しております。
お問い合わせ
コストダウンが利益に直結する術だと理解していても、なかなか前に進めることができない状況。そんな時は、newjiのコストダウン自動化機能で大きく利益貢献しよう!
(Β版非公開)