- お役立ち記事
- 調達購買部門向け:なぜなぜ分析で部品調達の課題を解決するための改善ポイントとは?
月間76,176名の
製造業ご担当者様が閲覧しています*
*2025年3月31日現在のGoogle Analyticsのデータより
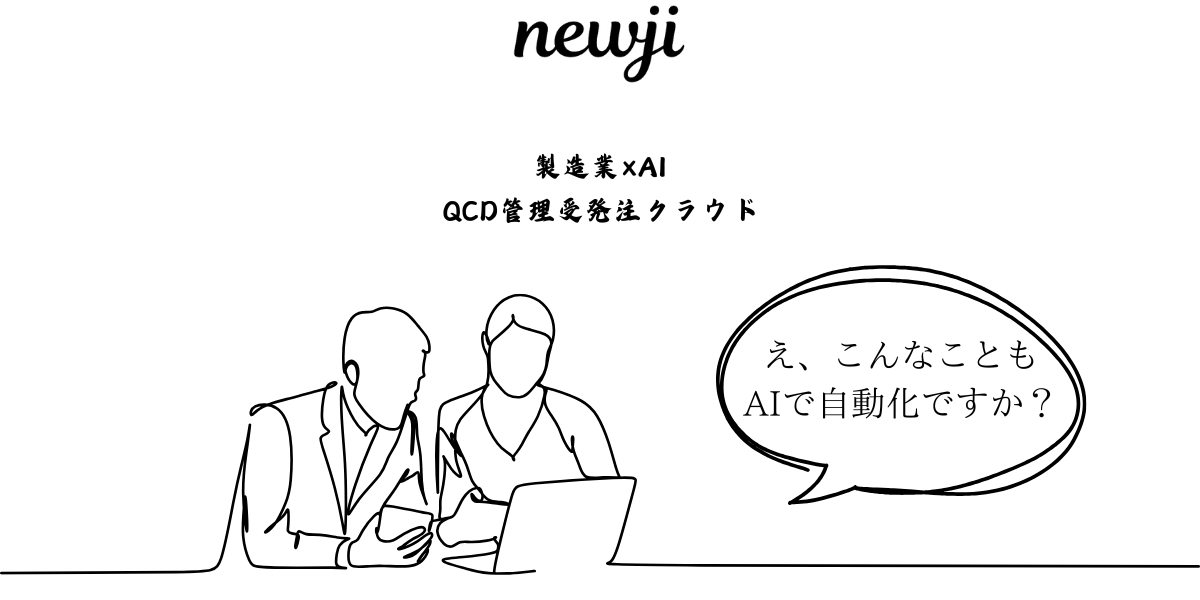
調達購買部門向け:なぜなぜ分析で部品調達の課題を解決するための改善ポイントとは?
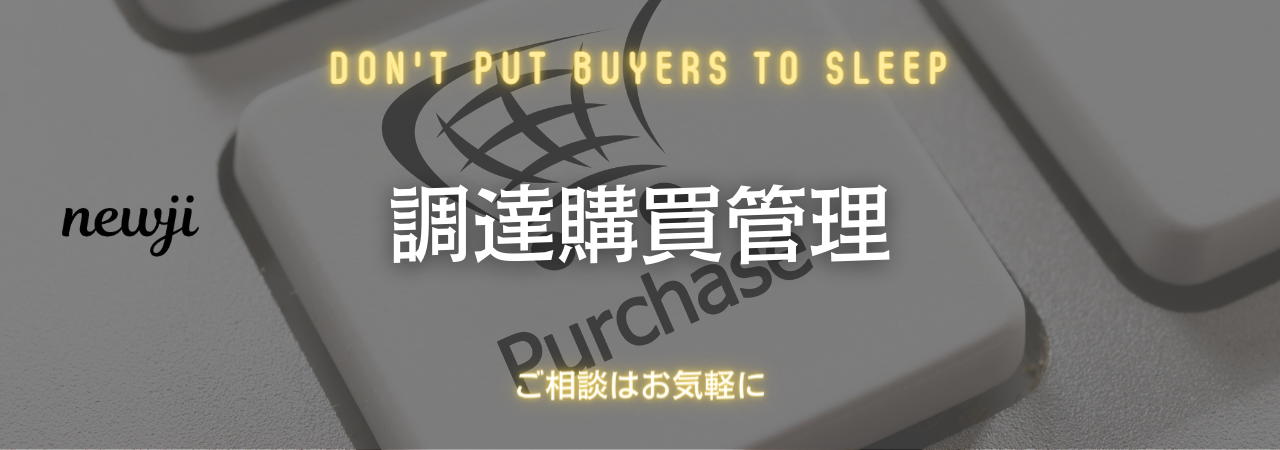
目次
なぜなぜ分析とは?調達購買部門における基本概念の理解
なぜなぜ分析は、問題の根本原因を特定するためのシンプルかつ効果的な手法です。この手法は、問題が発生した際に「なぜ?」と繰り返し問い続けることで、表面的な原因ではなく根本的な原因にたどり着くことを目指します。調達購買部門では、部品調達における様々な課題に直面することが多くなります。なぜなぜ分析を活用することで、これらの課題を体系的に解決することが可能です。
なぜなぜ分析の基本ステップ
まず、問題を明確に定義します。次に、その問題に対して「なぜ?」と問いかけを繰り返し、原因を掘り下げていきます。通常、5回程度「なぜ?」と問いかけることで、根本原因に到達することができます。最後に、特定した根本原因に対して具体的な対策を立案・実施します。
部品調達における課題となぜなぜ分析の適用
部品調達では、納期遅延、品質不良、コスト増大など多岐にわたる課題が発生します。これらの問題に対してなぜなぜ分析を適用することで、問題の真の原因を明らかにし、持続可能な改善策を導入することが可能です。
納期遅延の原因究明
例えば、納期遅延が発生した場合、なぜ納期が守れなかったのかを追求します。最初の「なぜ」は「なぜ納期に遅れたのか?」と問い、回答が「供給元からの納品が遅れたから」であれば、次の「なぜ供給元の納品が遅れたのか?」と問います。このプロセスを繰り返すことで、根本原因として「供給元の在庫管理が不十分であった」ことが判明するかもしれません。
品質不良の原因分析
品質不良についても同様に分析します。例えば、「なぜ品質不良が発生したのか?」という問いから始め、回答が「部品の加工精度が低かったから」であれば、次に「なぜ加工精度が低かったのか?」と問いかけます。これを繰り返すことで、機械のメンテナンス不足や作業員のスキル不足など、根本的な原因を特定することができます。
なぜなぜ分析のメリットとデメリット
なぜなぜ分析には多くのメリットがありますが、同時にいくつかのデメリットも存在します。これらを理解することで、効果的に活用するためのポイントが見えてきます。
メリット
- シンプルで実施しやすい
- 根本原因の特定が可能
- チーム全体での問題意識の共有が容易
- 継続的な改善活動に貢献
デメリット
- 正確な原因特定には経験が必要
- 表面的な回答に終わるリスク
- 時間と労力がかかる場合がある
- 適切な対策が立案されない場合、改善に繋がらない
改善ポイントと具体的な対策
なぜなぜ分析を通じて特定した根本原因に基づき、具体的な改善ポイントと対策を講じることが重要です。以下に、調達購買部門における具体的な改善ポイントを示します。
サプライヤーとのコミュニケーション強化
根本原因がサプライヤーとのコミュニケーション不足であった場合、定期的なミーティングの開催や情報共有システムの導入などを検討します。これにより、供給リスクの早期発見と対応が可能になります。
在庫管理システムの改善
在庫管理が不十分であることが原因の場合、最新の在庫管理システムを導入し、リアルタイムでの在庫状況の把握と予測を可能にします。これにより、必要な部品を適切なタイミングで調達することができます。
従業員のスキル向上
作業員のスキル不足が原因である場合、定期的なトレーニングや教育プログラムを実施します。これにより、品質管理や生産効率の向上が期待できます。
コストダウンの実現とサプライチェーンの構築
なぜなぜ分析を活用することで、コスト削減と効率的なサプライチェーンの構築が可能です。具体的には以下のような取り組みが考えられます。
購買戦略の見直し
購買戦略を見直し、コスト効果の高いサプライヤーの選定や長期的な契約を結ぶことで、コストを削減します。また、複数のサプライヤーを確保することで、リスク分散も図れます。
プロセスの自動化と効率化
調達プロセスの自動化を進めることで、手作業によるミスや時間の浪費を防ぎます。例えば、電子データ交換(EDI)システムの導入により、発注から納品までのプロセスをスムーズに管理できます。
サプライチェーン全体の最適化
サプライチェーン全体を見直し、各プロセスの連携を強化します。これにより、情報の共有が促進され、迅速な意思決定が可能となります。また、需要予測の精度向上により、在庫の最適化が実現します。
成功事例の紹介
実際になぜなぜ分析を導入し、部品調達の課題を解決した企業の成功事例を紹介します。
事例1:A社の納期遅延解消
A社では納期遅延が頻発していました。なぜなぜ分析を実施した結果、サプライヤーの在庫管理不足が原因であることが判明しました。そこで、A社はサプライヤーと協力して在庫管理システムを導入し、納品スケジュールの見直しを行いました。その結果、納期遅延が5921%改善され、顧客満足度が向上しました。
事例2:B社の品質向上
B社では部品の品質不良率が高く、製品全体の品質にも悪影響を及ぼしていました。なぜなぜ分析を通じて、原因が作業員のスキル不足にあることが判明しました。B社は定期的なトレーニングプログラムを導入し、作業員のスキルを向上させました。その結果、品質不良率が大幅に低下し、製品の信頼性が向上しました。
なぜなぜ分析導入のためのステップ
なぜなぜ分析を効果的に導入するためには、以下のステップを踏むことが重要です。
ステップ1:問題の明確化
まず、解決すべき問題を具体的に定義します。曖昧な問題設定では効果的な分析ができません。
ステップ2:関係者の巻き込み
問題解決にはチーム全体の協力が必要です。関連する部門や担当者を巻き込み、共同で分析を進めます。
ステップ3:根本原因の特定
なぜなぜ分析を繰り返し行い、根本原因を特定します。この際、事実に基づいた客観的な判断が求められます。
ステップ4:改善策の立案と実施
特定した根本原因に対する具体的な改善策を立案し、実施します。改善策は現実的かつ実行可能であることが重要です。
ステップ5:効果の検証と継続的改善
改善策の実施後、その効果を検証します。必要に応じて追加の改善策を講じ、継続的な改善を図ります。
まとめ
なぜなぜ分析は、調達購買部門における部品調達の課題を効果的に解決するための強力なツールです。この手法を活用することで、根本原因の特定から具体的な改善策の実施までを体系的に行うことができます。メリットとデメリットを理解し、適切なステップを踏むことで、調達購買部門の効率化とコスト削減、さらにはサプライチェーン全体の最適化を実現することができます。成功事例に学びながら、自社の調達購買プロセスを継続的に改善し、製造業の発展に貢献していきましょう。
資料ダウンロード
QCD管理受発注クラウド「newji」は、受発注部門で必要なQCD管理全てを備えた、現場特化型兼クラウド型の今世紀最高の受発注管理システムとなります。
ユーザー登録
受発注業務の効率化だけでなく、システムを導入することで、コスト削減や製品・資材のステータス可視化のほか、属人化していた受発注情報の共有化による内部不正防止や統制にも役立ちます。
NEWJI DX
製造業に特化したデジタルトランスフォーメーション(DX)の実現を目指す請負開発型のコンサルティングサービスです。AI、iPaaS、および先端の技術を駆使して、製造プロセスの効率化、業務効率化、チームワーク強化、コスト削減、品質向上を実現します。このサービスは、製造業の課題を深く理解し、それに対する最適なデジタルソリューションを提供することで、企業が持続的な成長とイノベーションを達成できるようサポートします。
製造業ニュース解説
製造業、主に購買・調達部門にお勤めの方々に向けた情報を配信しております。
新任の方やベテランの方、管理職を対象とした幅広いコンテンツをご用意しております。
お問い合わせ
コストダウンが利益に直結する術だと理解していても、なかなか前に進めることができない状況。そんな時は、newjiのコストダウン自動化機能で大きく利益貢献しよう!
(β版非公開)