- お役立ち記事
- 設計検証と設計確認の違い
月間76,176名の
製造業ご担当者様が閲覧しています*
*2025年3月31日現在のGoogle Analyticsのデータより
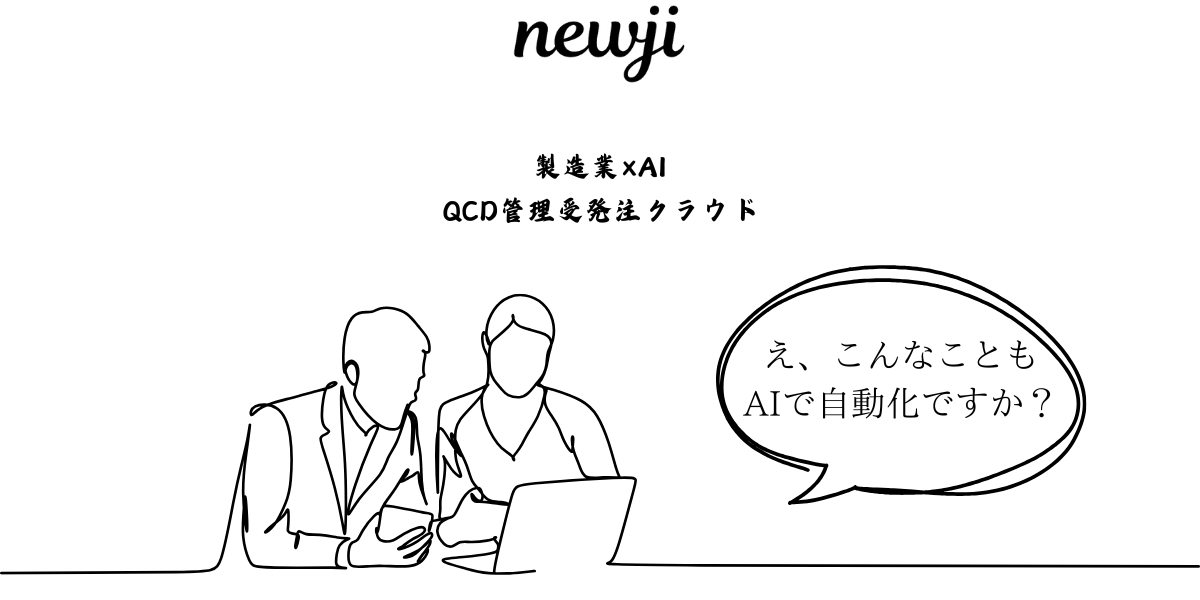
設計検証と設計確認の違い
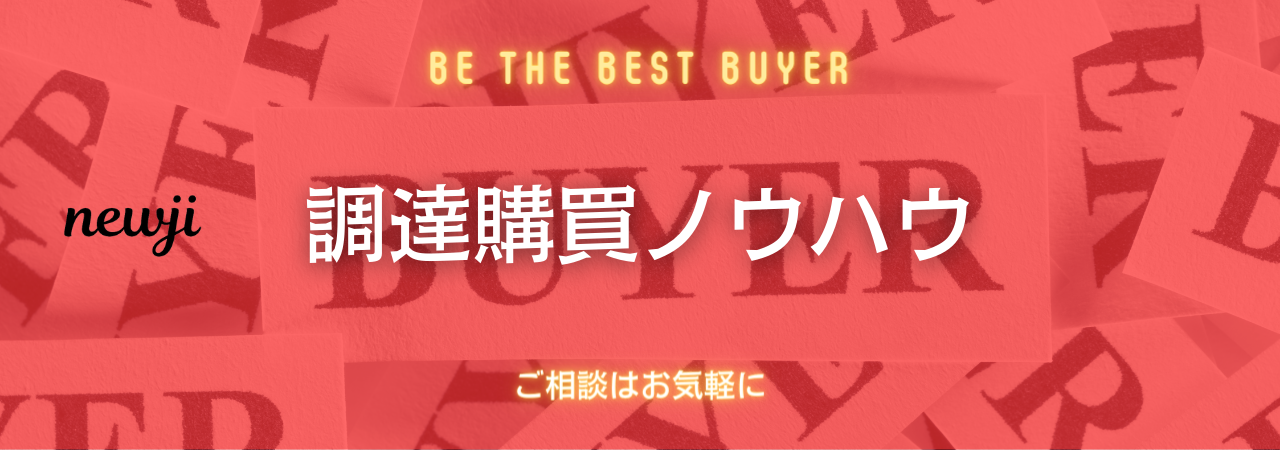
目次
設計検証と設計確認の違いとは?
製造業における設計プロセスでは、設計検証と設計確認という重要なステップが存在します。
これらのステップは品質を保証するために不可欠であり、適切に実施されないと重大な問題が発生する可能性があります。
本記事では、設計検証と設計確認の違いや、それぞれの重要性について解説します。
設計検証とは
設計検証の目的
設計検証の主な目的は、設計が意図された要求仕様に基づいて正しく行われているかどうかを確認することです。
設計検証は製品が開発段階で仕様を満たすと確認できるプロセスで、具体的には以下のような内容を評価します。
1. 設計が規定の要求条件を満たしているか
2. 設計図やモデルが誤りなく作成されているか
3. 技術仕様や性能要求を満たしているか
設計検証の手法
設計検証にはさまざまな手法があります。
主な手法としては以下が挙げられます。
1. **シミュレーション**:設計を実際に製品に反映する前に、コンピュータシミュレーションで性能や動作を確認します。
2. **レビュー**:設計チームや第三者による設計レビューを実施し、設計の適正さを確認します。
3. **プロトタイピング**:試作品を製作し、実際の動作や性能をテストします。
設計確認とは
設計確認の目的
設計確認の主な目的は、最終製品が顧客の要求を満たしているかどうかを確定することです。
設計確認は通常、製品開発の各フェーズで行われ、以下のような点を確認します。
1. 製品が設計仕様通りに製作されているか
2. 製品の性能が要求事項を満たしているか
3. 製品が顧客の使用条件に適しているか
設計確認の手法
設計確認もいくつかの方法で実施されますが、その中でも重要なのは次の手法です。
1. **試験・テスト**:最終製品や試作品を用いた物理的な試験やテストを行い、設計仕様や性能を確認します。
2. **インスペクション**:製品の外観や構造を目視でチェックし、設計通りに作られているか確認します。
3. **フィードバック収集**:顧客やエンドユーザーからのフィードバックを収集し、製品がニーズを満たしているか確認します。
設計検証と設計確認の違い
設計検証と設計確認は似たようなプロセスに思われるかもしれませんが、実際には異なる目的と手法を持っています。
目的の違い
1. **設計検証**:設計が技術仕様や要求条件を満たしていることを確認します。
2. **設計確認**:最終製品が顧客の要求を満たしているかを確定します。
実施のタイミングの違い
1. **設計検証**:製品開発の初期段階から中間段階まで行われます。
2. **設計確認**:最終段階で行われ、製品が市場に出る直前に実施されます。
手法の違い
1. **設計検証**:シミュレーション、設計レビュー、プロトタイピングなどが主な手法です。
2. **設計確認**:試験、テスト、インスペクション、顧客フィードバック収集が主な手法です。
失敗事例から学ぶ設計検証と設計確認の重要性
設計検証や設計確認が不十分だったために大きな損害が生じた例もあります。
失敗事例:某自動車メーカーのリコール問題
ある著名な自動車メーカーが、新しいモデルのブレーキシステムに問題があることが量産開始後に判明し、大規模なリコールを余儀なくされました。
このケースでは、設計検証の段階でブレーキシステムの性能がシミュレーションのみで確認され、実地での試験が不十分だったことが原因です。
結果として、数百万ドルに上る損失が発生しました。
成功事例:高性能電子機器の開発
一方、ある電子機器メーカーは、設計段階で徹底した検証と確認を行い、顧客のニーズを超える性能を実現しました。
試作段階で徹底的なテストとフィードバック収集を行った結果、高性能かつ信頼性の高い製品を市場投入することに成功し、大きな収益を得ることができました。
最新技術による設計検証と設計確認の進化
技術の進化に伴い、設計検証と設計確認の手法も年々高度化しています。
シミュレーション技術の進化
高性能コンピュータと高度なシミュレーションソフトウェアにより、設計検証の精度が飛躍的に向上しています。
実際の物理環境をシミュレートすることで、現実に即した検証を短時間で行うことが可能となりました。
IoTとビッグデータの活用
IoT(Internet of Things)技術を活用し、製品の使用データをリアルタイムで収集・分析することが可能です。
これにより、設計確認時に製品の実際の使用状況を把握し、迅速にフィードバックを反映できます。
設計検証と設計確認のまとめ
設計検証と設計確認は、いずれも製造業において非常に重要なプロセスです。
設計検証は、設計が技術仕様や要求条件を満たしているかを確認するプロセスであり、主にシミュレーションや設計レビュー、プロトタイピングを用います。
一方、設計確認は、最終製品が顧客の要求を満たしているかどうかを確認するプロセスで、試験、テスト、インスペクション、顧客フィードバック収集が主な手法となります。
失敗事例と成功事例からも明らかなように、両者を適切に実施することが製品の品質を保証し、市場での成功につながります。
また、最新技術を活用することで、これらのプロセスをさらに効果的に行うことができるようになっています。
製造業に携わるすべての方々が、このプロセスをしっかりと理解し、実践することで、より高品質な製品を世に送り出すことができるでしょう。
それが、製造業の発展に寄与する重要な要素となるのです。
資料ダウンロード
QCD管理受発注クラウド「newji」は、受発注部門で必要なQCD管理全てを備えた、現場特化型兼クラウド型の今世紀最高の受発注管理システムとなります。
ユーザー登録
受発注業務の効率化だけでなく、システムを導入することで、コスト削減や製品・資材のステータス可視化のほか、属人化していた受発注情報の共有化による内部不正防止や統制にも役立ちます。
NEWJI DX
製造業に特化したデジタルトランスフォーメーション(DX)の実現を目指す請負開発型のコンサルティングサービスです。AI、iPaaS、および先端の技術を駆使して、製造プロセスの効率化、業務効率化、チームワーク強化、コスト削減、品質向上を実現します。このサービスは、製造業の課題を深く理解し、それに対する最適なデジタルソリューションを提供することで、企業が持続的な成長とイノベーションを達成できるようサポートします。
製造業ニュース解説
製造業、主に購買・調達部門にお勤めの方々に向けた情報を配信しております。
新任の方やベテランの方、管理職を対象とした幅広いコンテンツをご用意しております。
お問い合わせ
コストダウンが利益に直結する術だと理解していても、なかなか前に進めることができない状況。そんな時は、newjiのコストダウン自動化機能で大きく利益貢献しよう!
(β版非公開)