- お役立ち記事
- 穴あけ (Drilling)の技術と製造業での利用方法
月間76,176名の
製造業ご担当者様が閲覧しています*
*2025年3月31日現在のGoogle Analyticsのデータより
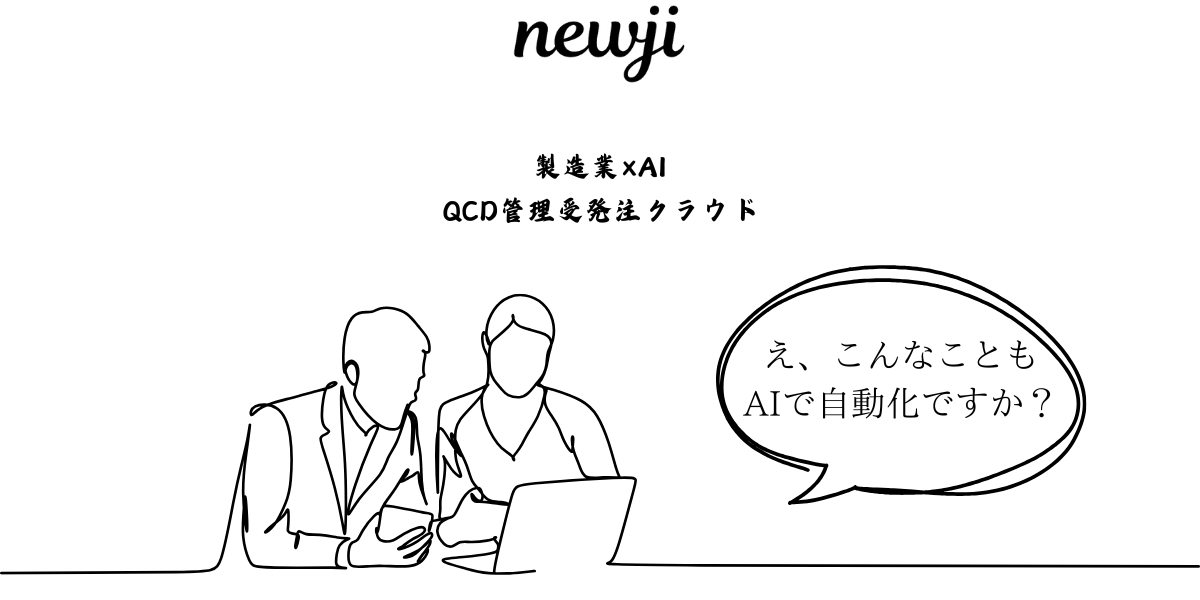
穴あけ (Drilling)の技術と製造業での利用方法
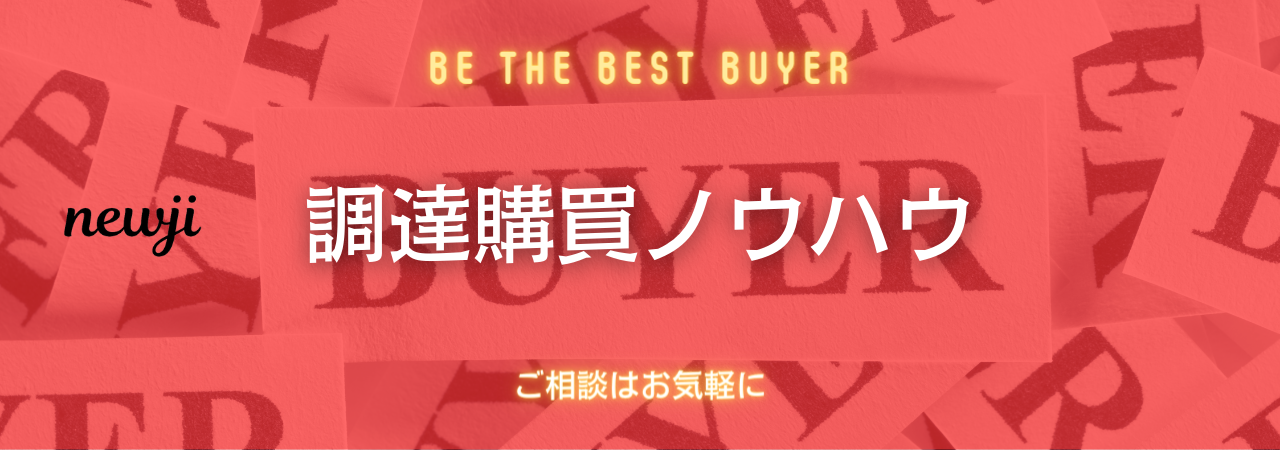
目次
はじめに
穴あけ(Drilling)は、製造業における基本的かつ重要な加工技術の一つです。
この技術は金属、プラスチック、木材などさまざまな素材に穴を開ける際に用いられます。
製造プロセスの一環として、穴あけ作業は精度や効率性が求められるため、最新の技術や設備が導入されています。
この記事では、穴あけ技術の概要から、現場での具体的な利用方法や最新動向について詳しく説明します。
穴あけ (Drilling) の基本技術
穴あけ技術の概要
穴あけ技術は、素材に対してドリルビットと呼ばれる工具を回転させながら押し進め、孔(穴)を形成する加工方法です。
ドリルビットは切削エッジを持ち、そのエッジが素材を削り取ることで穴が形成されます。
ドリルビットの材質や形状、回転速度、進行速度などが穴あけの品質に直接影響を与えるため、これらの要素を適切に設定することが重要です。
主要なドリルビットの種類
ドリルビットには多くの種類がありますが、特に一般的なものとして以下の種類があります。
– **ツイストドリルビット**:最も一般的なタイプで、幅広い素材に対応します。
– **スパイラルドリルビット**:フラットな表面に対して高い精度で穴を開けることができます。
– **コアドリルビット**:円筒状の穴を開けるためのビットで、特に大型の穴に適しています。
– **ステップドリルビット**:異なる径の段階的な穴を一度の操作で開けることができます。
穴あけ技術の応用範囲
穴あけ技術は、多岐にわたる産業分野で応用されています。
たとえば、自動車産業ではエンジンパーツやシャーシ部品の製作に欠かせません。
家電製品の組み立てや建築分野での配管設置もまた、穴あけ技術を利用しています。
これにより、製品の品質向上や生産効率の向上が図られています。
最新の穴あけ技術とその応用
高速高精度穴あけ技術
近年、製造業界はますます高速で高精度な穴あけを求めるようになりました。
これに応じて、新たなドリルビット素材や特殊なコーティングが開発されています。
特に、CVD(化学蒸着法)やPVD(物理蒸着法)によるコーティングが施されたドリルビットは、耐摩耗性が高く、長寿命で高精度な穴あけが可能です。
また、マシニングセンターやNC(数値制御)技術を活用することで、一貫して高精度な穴あけが実現しています。
例えば、特定の穴径を繰り返し高精度に開ける場合は、NC機械のプログラムを活用することで、オペレーターの熟練度に依存せずに安定した品質が保てます。
自動化技術の導入
製造業においては、FA(ファクトリーオートメーション)技術が進展し、穴あけ作業も自動化が進んでいます。
ロボットアームやAGV(自動搬送車)との連携により、連続した穴あけ作業が効率的に行われています。
これにより、作業時間の短縮、人手不足の解消、品質の安定化が図れます。
また、IoT(モノのインターネット)技術を活用し、リアルタイムでの機械の状態監視や予防保全が行われるようになってきています。
高硬度素材への対応
航空機や宇宙産業、自動車産業などでは、高硬度な素材の利用が増えており、こうした素材への穴あけ技術も進化しています。
特に、炭素繊維強化プラスチック(CFRP)やチタン合金など、切削が難しい素材への対応が求められています。
これに対応するために、特殊なドリルビットやクーラント技術、超音波振動を利用した穴あけ技術などが開発されています。
例えば、超音波振動を用いた穴あけ技術は、硬い材料でも低負荷で加工が可能であり、工具寿命の延長にもつながります。
現場での具体的な利用方法
ドリルビットの選定とメンテナンス
穴あけ技術を効果的に活用するためには、目的に応じた適切なドリルビットを選定することが重要です。
例えば、軟質素材には高速鋼(HSS)のツイストドリルビットが適していますが、高硬度素材に対しては超硬合金製のビットが推奨されます。
また、ドリルビットのメンテナンスも欠かせません。
切れ味が落ちたドリルビットは穴の品質に悪影響を及ぼし、加工時間も増加します。
定期的な研削や交換を行い、常に切れ味の良い状態を保つことが大切です。
加工環境の整備
穴あけ作業の精度と効率を向上させるためには、加工環境の整備も重要です。
加工機械のベースが安定していること、適切なクーラント供給が行われていること、切削片の排出経路が確保されていることなどが挙げられます。
特にクーラントは、熱の発生を抑え、加工面の品質を保つために重要な役割を果たします。
自動化システムの導入事例
実際の現場で導入されている自動化システムの事例を紹介します。
一つの例として、自動車部品メーカーの生産ラインがあります。
ここでは、複数のロボットアームが協調して動き、異なるサイズの穴を一度に開けるシステムが導入されています。
このシステムにより、作業効率が大幅に向上し、不良品の発生率も低減しました。
また、航空機製造ラインでは、AGVがパーツを自動的に搬送し、特定の位置で高速高精度の穴あけを行うシステムが稼働しています。
これにより、一貫した製品品質が保たれ、生産性も向上しています。
最新の技術動向
AIと機械学習の活用
AI(人工知能)や機械学習技術の進展により、穴あけ技術もさらに進化しています。
例えば、AIを用いたカメラシステムが、ドリルビットの状態をリアルタイムで監視し、適切なタイミングで交換をアラートするシステムが開発されています。
これにより、突発的なトラブルを防ぎ、ダウンタイムを最小限に抑えることができます。
また、機械学習アルゴリズムを活用して、過去の加工データから最適な加工条件を自動で提案するシステムも登場しています。
これにより、オペレーターの熟練度に依存せず、常に最適な加工が行えるようになります。
データ駆動型の監視と制御
IoT技術の発展により、穴あけ機械もネットワークに接続され、データ駆動型の監視と制御が行えるようになっています。
各加工機械の状態データを一元的に収集・分析し、予防保全の計画やリアルタイムでの最適な制御が実現しています。
たとえば、センサーを装備した加工機械は、振動や温度、切削力などのデータをリアルタイムでモニタリングし、異常を早期に検知することができます。
これにより、設備の停止や不良品の発生を未然に防ぐことが可能になります。
まとめ
穴あけ(Drilling)は製造業における基本的な加工技術であり、その精度と効率性は生産ライン全体の品質や速度に大きく影響します。
最新の技術動向と共に、自動化やデータ駆動型のアプローチが進んでおり、製造現場での応用範囲も広がっています。
高精度な穴あけ技術を活用して、質の高い製品の生産を目指しましょう。
資料ダウンロード
QCD管理受発注クラウド「newji」は、受発注部門で必要なQCD管理全てを備えた、現場特化型兼クラウド型の今世紀最高の受発注管理システムとなります。
ユーザー登録
受発注業務の効率化だけでなく、システムを導入することで、コスト削減や製品・資材のステータス可視化のほか、属人化していた受発注情報の共有化による内部不正防止や統制にも役立ちます。
NEWJI DX
製造業に特化したデジタルトランスフォーメーション(DX)の実現を目指す請負開発型のコンサルティングサービスです。AI、iPaaS、および先端の技術を駆使して、製造プロセスの効率化、業務効率化、チームワーク強化、コスト削減、品質向上を実現します。このサービスは、製造業の課題を深く理解し、それに対する最適なデジタルソリューションを提供することで、企業が持続的な成長とイノベーションを達成できるようサポートします。
製造業ニュース解説
製造業、主に購買・調達部門にお勤めの方々に向けた情報を配信しております。
新任の方やベテランの方、管理職を対象とした幅広いコンテンツをご用意しております。
お問い合わせ
コストダウンが利益に直結する術だと理解していても、なかなか前に進めることができない状況。そんな時は、newjiのコストダウン自動化機能で大きく利益貢献しよう!
(β版非公開)