- お役立ち記事
- ロジカルシンキングによる「なぜなぜ分析」の基礎と不具合再発防止へのポイント
月間76,176名の
製造業ご担当者様が閲覧しています*
*2025年3月31日現在のGoogle Analyticsのデータより
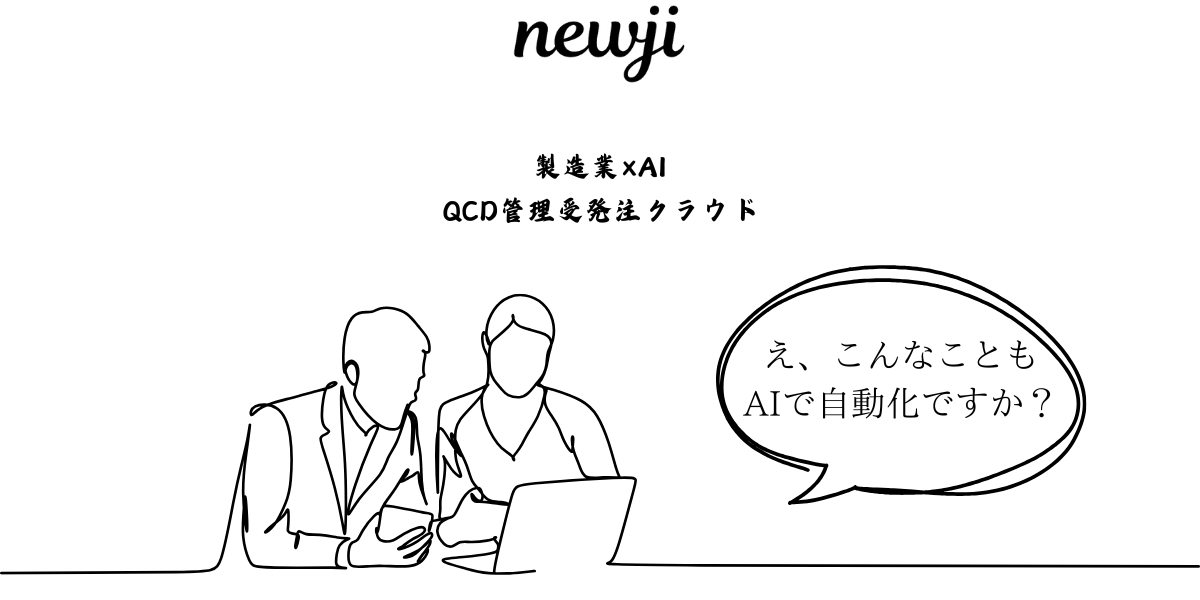
ロジカルシンキングによる「なぜなぜ分析」の基礎と不具合再発防止へのポイント
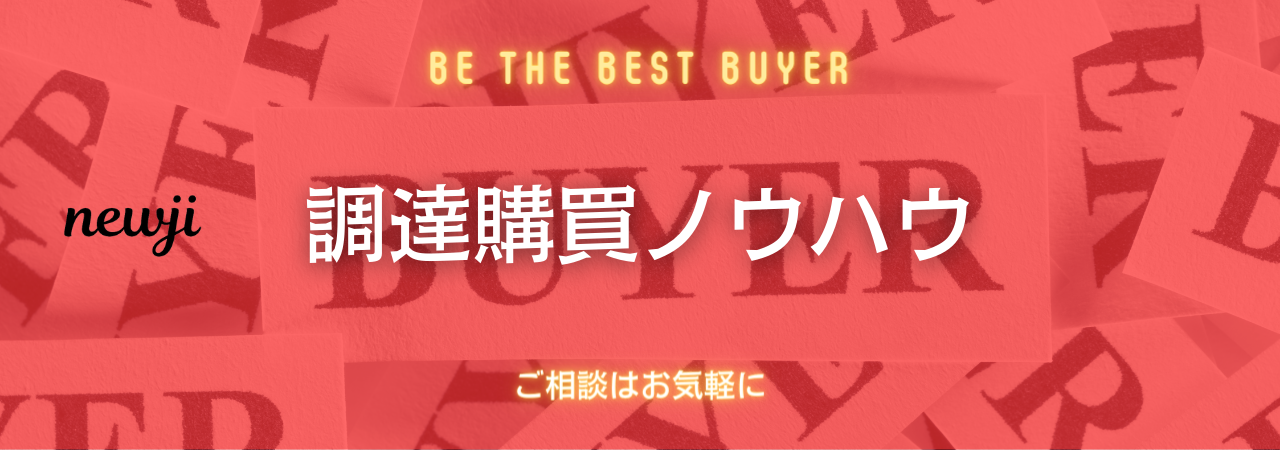
目次
はじめに
製造業において、不具合の発生は避けられない現実です。
それをいかに効率的に、再発を防ぐ形で改善していくかが重要です。
「なぜなぜ分析」はロジカルシンキングを用いた不具合の原因究明手法として、多くの現場で活用されています。
この記事では、「なぜなぜ分析」の基本的な考え方から具体的な実践方法、不具合再発防止のためのポイントまでを詳しく解説します。
なぜなぜ分析とは
なぜなぜ分析の基本概念
「なぜなぜ分析」は、不具合が発生した際にその原因を深く掘り下げるための手法です。
ただ単に表面的な原因を取り除くのではなく、根本原因(真因)を追求することで、再発防止を目指します。
一般的には「なぜ」を5回繰り返して根本原因に到達することを目的としています。
シンプルでありながらも、効果的な原因解析方法として重宝されています。
ロジカルシンキングとの関係
ロジカルシンキングとは、論理的な思考を用いて問題を解決する方法です。
「なぜなぜ分析」はロジカルシンキングの応用であり、論理的に一連の因果関係を追求することが重要です。
論理的に矛盾のない形で「なぜ」を繰り返すことで、問題の根本にたどり着くことが可能となります。
なぜなぜ分析の手順
ステップ1: 問題の定義
最初のステップは、分析対象の不具合を明確に定義することです。
ここでは、問題の内容、発生した場所、影響の範囲などを詳しく記述します。
不具合が具体的にどのようなものであるかを明らかにすることで、分析の方向性を定めます。
ステップ2: 初期なぜを設定する
問題を定義した後は、「なぜその問題が発生したのか」を問います。
これが「初期なぜ」です。
初期なぜに対する答えが導き出され、それに対するさらなる「なぜ」を重ねていくことで、分析を深めていきます。
ステップ3: 根本原因の追求
初期なぜに対する答えを基に、さらに「なぜ」を質問し続けます。
このプロセスを繰り返して、論理的に整合性のある答えを積み重ねながら根本原因にたどり着きます。
注意すべきは、表面的な原因で止まらず、仮説を検証しつつ振り返りながら進めることです。
ステップ4: 是正措置の立案
根本原因を特定したら、その原因を再発させないための是正措置を考える段階です。
この是正措置は、製造プロセスの修正や人的要因の管理など、様々な側面が考慮されます。
具体的かつ実行可能な施策を立案することが求められます。
ステップ5: 効果の確認と改善
是正措置を実施した後、その効果を確認します。
効果が不十分である場合は、再度「なぜなぜ分析」を行い、別の根本原因を探る必要があるかもしれません。
この継続的な改善が、品質向上と安定した生産体制の構築に繋がります。
なぜなぜ分析の成功ポイント
分析チームの適切な編成
「なぜなぜ分析」は、複数人で行うことで様々な視点からの意見を取り入れやすくなります。
現場の担当者、品質管理の専門家、技術担当者など、関連する部署からバランスよくメンバーを集めることがポイントです。
データの正確な収集
分析にあたって、正確で詳細なデータを収集することが必要です。
曖昧な情報や推測に基づく分析は、誤った結論を導きかねません。
可能な限り事実に基づいたデータを収集し、それに基づいて次のステップを進めることが重要です。
オープンなコミュニケーション
なぜなぜ分析では、チーム内でオープンなコミュニケーションを築くことが大切です。
各メンバーが自由に意見を述べ、疑問を提起できる雰囲気を作ることで、より深い分析が可能となります。
意見のぶつかり合いもまた、建設的な対話により次のステップへの糧となります。
原因の仮説と検証の循環
原因究明では、様々な仮説を立て、それを検証するというサイクルを繰り返します。
仮説が間違っていることもあり得ますが、それを恐れずに明確にし、検証を重ねることが重要です。
なぜなぜ分析を活用した不具合再発防止策
是正措置の実効性を高める
再発防止に向けて導入する是正措置は、効果的であることが求められます。
そのためのポイントは、ムリなく現場に根付く施策を考えることです。
オペレーションの流れに自然に組み込まれる施策は、より効果を発揮します。
継続的な改善推進
一度の改善施策だけで再発防止は完全に成し得ることは難しいです。
継続的なモニタリングと分析を行い、さらなる改善を重ねる必要があります。
PDCAサイクルを意識しながら、長期的に取り組む姿勢が大切です。
知識共有と教育の強化
不具合分析の知見を部署内だけでなく、広く組織全体で共有することが重要です。
また、新しいチームメンバーや関連企業に対してもなぜなぜ分析の手法や具体例を共有し、教育していくことが肝要です。
組織全体で成長できる環境を整えることが、さらなる品質向上につながります。
まとめ
「なぜなぜ分析」は、製造業における不具合の原因究明と再発防止において、非常に効果的な手法です。
ロジカルシンキングを基本とし、なぜを繰り返して根本原因を追及することで、表面的な解決に終わらない真の改善が可能となります。
適切なチーム編成、データの正確な収集、オープンなコミュニケーション、仮説と検証のサイクルなど、成功するためのポイントを押さえ、組織全体での知識共有を進めることが、長期的な品質向上に繋がります。
これから製造業に関わる方々にとっても、実践的な知識として役立つことを願っています。
資料ダウンロード
QCD管理受発注クラウド「newji」は、受発注部門で必要なQCD管理全てを備えた、現場特化型兼クラウド型の今世紀最高の受発注管理システムとなります。
ユーザー登録
受発注業務の効率化だけでなく、システムを導入することで、コスト削減や製品・資材のステータス可視化のほか、属人化していた受発注情報の共有化による内部不正防止や統制にも役立ちます。
NEWJI DX
製造業に特化したデジタルトランスフォーメーション(DX)の実現を目指す請負開発型のコンサルティングサービスです。AI、iPaaS、および先端の技術を駆使して、製造プロセスの効率化、業務効率化、チームワーク強化、コスト削減、品質向上を実現します。このサービスは、製造業の課題を深く理解し、それに対する最適なデジタルソリューションを提供することで、企業が持続的な成長とイノベーションを達成できるようサポートします。
製造業ニュース解説
製造業、主に購買・調達部門にお勤めの方々に向けた情報を配信しております。
新任の方やベテランの方、管理職を対象とした幅広いコンテンツをご用意しております。
お問い合わせ
コストダウンが利益に直結する術だと理解していても、なかなか前に進めることができない状況。そんな時は、newjiのコストダウン自動化機能で大きく利益貢献しよう!
(β版非公開)