- お役立ち記事
- Manufacturing Innovations Enabled by Digital Twin Technology
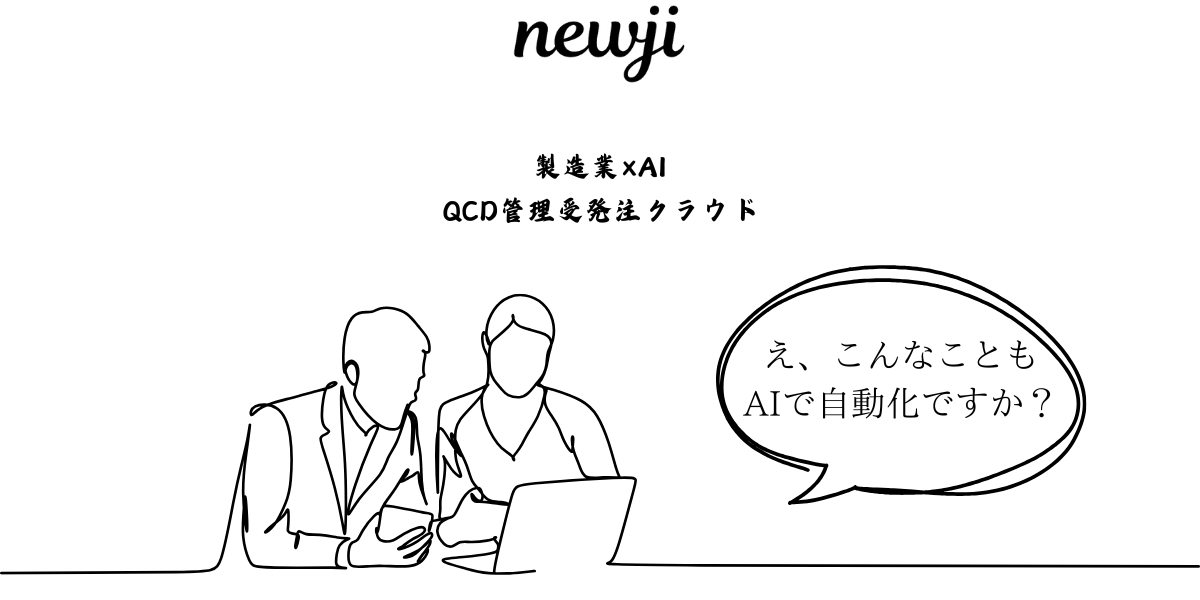
Manufacturing Innovations Enabled by Digital Twin Technology
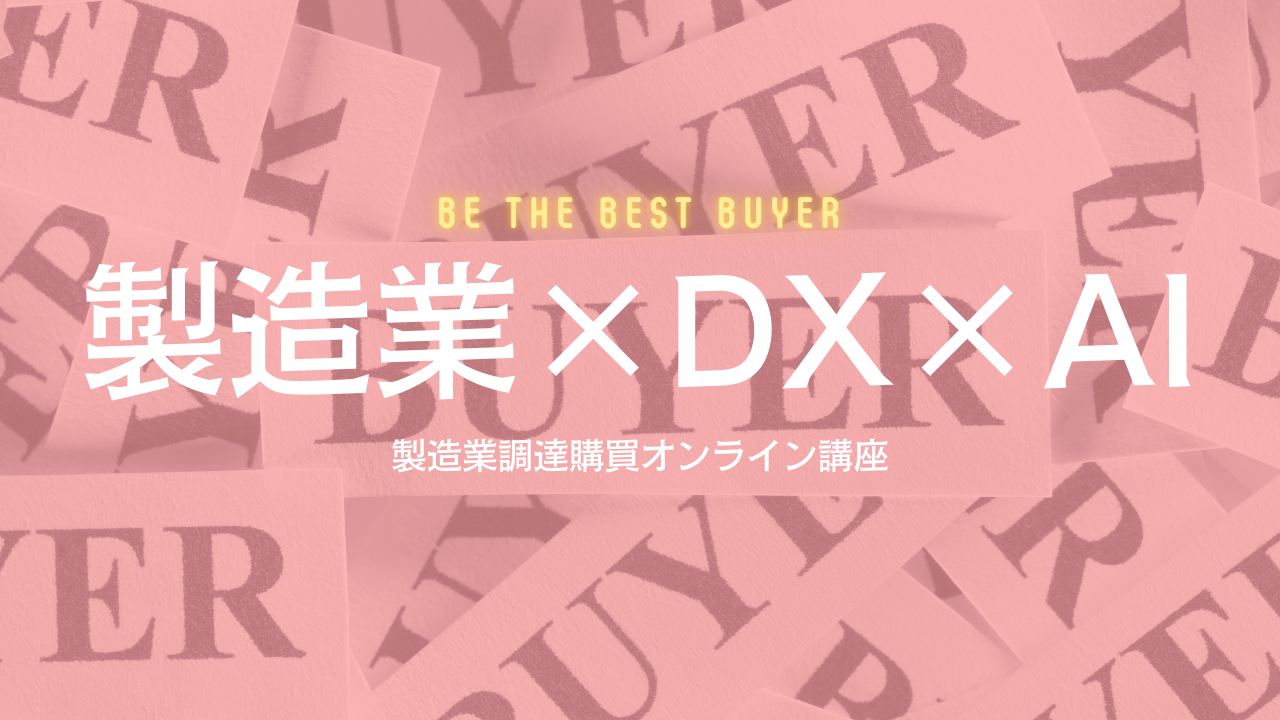
Digital twin technology has enabled innovative new solutions throughout the manufacturing industry. A digital twin is a virtual representation of a physical object or system across its lifecycle, using data gathered from IoT sensors and other sources. By creating digital simulations of products and assembly lines, manufacturers can optimize processes, preempt issues, and accelerate product development in ways that were not previously possible.
One example is how digital twins are helping to improve factory automation. Companies developing new automated systems can build digital replicas to extensively test robotics, machining programs, and product flows before implementation. This reduces risks and costs associated with real-world trial and error. Engineers identify bottlenecks or ergonomic issues in the virtual world first, allowing problems to be addressed on the design stage rather than after equipment installation. Remote monitoring of digital twins also enables predictive maintenance by identifying performance degradations early.
Automakers have been leaders in implementing digital twin technology on production lines. Digital models of vehicle assembly operations give managers insights into historical KPI data like cycle times, throughput rates, and downtime incidents. Artificial intelligence algorithms analyze this data to determine the most efficient sequencing of tasks. Digitally simulated “what if” scenarios then help optimize processes. For instance, automakers have discovered assembly line reconfigurations that save minutes per vehicle – translating to millions in annual savings.
Another benefit is using digital twins during new product development cycles. Engineers from different disciplines worldwide can collaborate via shared digital environments to vet design proposals in parallel. This discovery process occurs virtually before expensive physical prototypes are produced. Digital simulations also enable complex systems to be prototyped, tested, and optimized much more quickly than traditional methods. Some estimates show digital twin-enabled product development cycles are 2-3 times faster than conventional approaches.
The aerospace industry leverages digital twin technology extensively as well. Intricate systems like jet engines involve components from hundreds of global suppliers that must interface seamlessly. Digital replicas allow every subsystem and interface to be rigorously tested in fully-integrated digital prototypes before production. This identifies interoperability issues early, saving enormous rework costs down the road. Aircraft manufacturers are also using digital twins to streamline maintenance and repair processes. Technicians can practice complicated procedures on virtual aircraft first to minimize errors and downtime for physical planes.
Going forward, the true potential of digital twins may be realized when networks of connected, interoperable models are established throughout entire value chains. Individual product or factory digital twins are insightful on their own, but the next stage involves linking these simulations together. A digital twin ecosystem would integrate representations of suppliers, manufacturing sites, logistics networks, and the products themselves across their useful lives. Real-time data flows between these distributed models promise even deeper optimization and predictive use cases. Entire circular economies may one day be managed, tested, and improved in virtual environments before implementation in the physical world.
While digital twin projects currently require substantial investments of capital and expertise, the long-term payoffs are compelling. Across industries, manufacturers that have embraced this technology are gaining significant competitive advantages in speed, efficiency, quality and sustainability. Digital twins open new windows into innovation by transcending physical limits and constraints. As the technology continues maturing, its full transformative potential is only beginning to be unlocked. The manufacturing leaders of the future may be those who most strategically develop and leverage networked systems of these powerful virtual representations.
資料ダウンロード
QCD調達購買管理クラウド「newji」は、調達購買部門で必要なQCD管理全てを備えた、現場特化型兼クラウド型の今世紀最高の購買管理システムとなります。
ユーザー登録
調達購買業務の効率化だけでなく、システムを導入することで、コスト削減や製品・資材のステータス可視化のほか、属人化していた購買情報の共有化による内部不正防止や統制にも役立ちます。
NEWJI DX
製造業に特化したデジタルトランスフォーメーション(DX)の実現を目指す請負開発型のコンサルティングサービスです。AI、iPaaS、および先端の技術を駆使して、製造プロセスの効率化、業務効率化、チームワーク強化、コスト削減、品質向上を実現します。このサービスは、製造業の課題を深く理解し、それに対する最適なデジタルソリューションを提供することで、企業が持続的な成長とイノベーションを達成できるようサポートします。
オンライン講座
製造業、主に購買・調達部門にお勤めの方々に向けた情報を配信しております。
新任の方やベテランの方、管理職を対象とした幅広いコンテンツをご用意しております。
お問い合わせ
コストダウンが利益に直結する術だと理解していても、なかなか前に進めることができない状況。そんな時は、newjiのコストダウン自動化機能で大きく利益貢献しよう!
(Β版非公開)