- お役立ち記事
- QFDを使って製造業のコスト削減と品質向上を実現する方法
月間76,176名の
製造業ご担当者様が閲覧しています*
*2025年3月31日現在のGoogle Analyticsのデータより
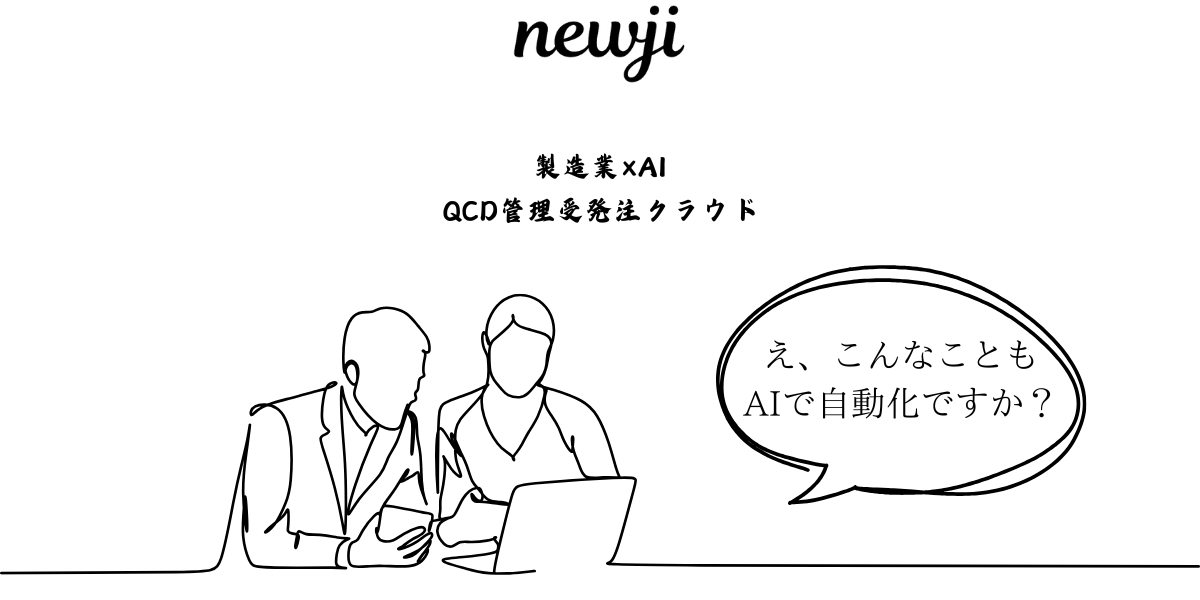
QFDを使って製造業のコスト削減と品質向上を実現する方法

目次
QFDとは?QFDの基本概念を理解しよう
QFD(Quality Function Deployment、品質機能展開)は、製品開発プロセスにおける品質の向上と顧客満足の達成を目指す手法です。
具体的には、顧客のニーズや要求を製品設計や生産プロセスに反映させるための構造化された方法です。
製造業では、品質とコストのバランスを取ることが常に求められますが、QFDを活用することでこのバランスを最適化することが可能です。
このツールは、日本の製造業において発祥し、特に自動車産業などで広く利用されています。
その後、国際的に広がり、多くの業界で採用されています。
QFDの主な要素には「ホウス・オブ・クオリティ(品質の家)」があります。
これは、顧客の要望を具体的な技術仕様に変換するためのマトリックス図です。
QFDのプロセス:具体的な手順と実践方法
ステップ1:顧客ニーズの収集
まず最初に行うべきは、顧客のニーズや要求を可能な限り具体的に収集することです。
これには、市場調査や顧客インタビュー、アンケートなどの手法が有効です。
収集したデータをもとに、顧客の欲しい機能や品質に対する要求を明確にします。
ステップ2:顧客ニーズの分類と優先順位付け
収集した顧客ニーズを整理し、重要度に応じて優先順位を付けます。
この作業は、製品開発の初期段階で行われるため、後の工程において大きな影響を与えます。
顧客の要求がどの程度重要か、競合製品と比較してどのように位置付けられているかを評価します。
ステップ3:技術的要件への転換
次に、顧客ニーズを技術的要件に変換します。
この段階で使用されるのが「ホウス・オブ・クオリティ」です。
この表は、横軸に「顧客の声」、縦軸に「技術的要件」を配置し、どの要件がどのニーズを満たすかを視覚的に表現します。
これにより、開発チームが求められている技術的仕様を明確に理解できます。
ステップ4:競合分析
市場で競争力を持つためには、自社製品と競合製品との比較が不可欠です。
QFDでは、競合製品の技術的要件や性能を分析し、自社製品との違いを明確にすることが求められます。
この結果を「ホウス・オブ・クオリティ」に反映させ、競争力を高めるための改善点を見つけ出します。
ステップ5:技術的要件の優先順位付け
技術的要件に対しても優先順位を設定します。
すべての要件を同時に満たすことは難しいため、重要度に基づいて段階的に取り組むことが必要です。
ここでの優先順位が、製品のコストや開発期間にも影響を与えるため、慎重に評価します。
QFDを活用したコスト削減の具体的な手法
無駄の排除によるコスト最適化
QFDを取り入れることで、無駄な機能やコストを削減することができます。
顧客のニーズを正確に把握し、それに基づいて設計を行うことで、不要な機能や過剰な仕様を避けることができます。
これにより、製品開発の初期段階からコストの無駄を防ぐことができます。
品質向上による再作業の削減
QFDは、品質を向上させるための強力なツールです。
顧客の要求に直接対応する設計を行うことで、後工程での再作業や修正を減少させることができます。
結果として、品質トラブルやクレーム対応にかかるコストが大幅に削減されます。
プロジェクト管理の効率化
QFDは、製品開発プロジェクトの進行管理にも大きく貢献します。
顧客のニーズを明確に把握し、それに基づいた開発計画を立てることで、スムーズなプロジェクト進行が可能となります。
「ホウス・オブ・クオリティ」による視覚的な管理も、チームのコミュニケーションを円滑にします。
QFDを通じた品質向上のアプローチ
顧客満足の向上
QFDにより、顧客の真のニーズを把握し、それを製品設計に反映させることで顧客満足を大幅に向上させることができます。
顧客が求める品質や機能を正確に提供することで、リピーターやブランドロイヤリティを高めることが可能です。
プロセスの標準化
QFDを導入することで、製品開発プロセスの標準化が進みます。
これにより、各部署間の連携がスムーズになり、一貫した品質管理が実現します。
標準化されたプロセスは、トラブルシューティングや品質保証の迅速化にも寄与します。
継続的改善の推進
QFDは、PDCA(Plan-Do-Check-Act)サイクルと組み合わせて使用することで、継続的な改善活動(KAIZEN)を推進します。
顧客のフィードバックを定期的に収集し、再度QFDのプロセスを通じて反映させることで、常に高品質の製品を提供し続けることができます。
最新技術とQFDの融合:IoTとAIの活用
IoTを活用したリアルタイムデータの収集
近年、IoT(Internet of Things)技術の進展により、製品の使用状況や性能データをリアルタイムで収集することが可能になりました。
これをQFDに活用すれば、顧客のニーズや使用パターンをより詳細に把握することができます。
リアルタイムデータは、製品改良や新機能の開発において重要な情報源となります。
AIによるデータ分析と予測
AI(人工知能)技術を活用することで、QFDの効率性をさらに高めることができます。
膨大なデータを迅速に分析し、顧客のニーズや市場のトレンドを予測することができます。
これにより、製品開発の方向性を適切に決定し、競争力を持った製品を迅速に市場投入することが可能となります。
デジタルツインによるシミュレーション
デジタルツイン技術を導入することで、製品の設計やプロセスを仮想空間でシミュレーションできます。
これにより、実際の製品開発前に多くの問題を発見し、解決することができます。
デジタルツインは、QFDと組み合わせることで、プロセス全体の効率性と品質を大幅に向上させることが可能です。
QFDの成功事例:実践から学ぶ
有名な成功事例として、トヨタ自動車の取り組みが挙げられます。
トヨタはQFDを利用することで、顧客のニーズに即した高品質でコスト競争力のある製品を開発し続けています。
具体的には、顧客の声を収集し、それをもとにした技術的要件を明確に設定し、製品開発の各段階でしっかりと反映させています。
この結果、トヨタは高い顧客満足度を維持しながら、効率的な製品開発を実現しています。
まとめ:QFDで最適なバランスを実現
QFDを活用することで、製造業において重要な「コスト削減」と「品質向上」という二つの要件をバランス良く実現することが可能です。
顧客のニーズを正確に把握し、それを技術的要件に変換するプロセスを通じて、無駄なコストを抑えつつ高品質な製品を提供することができます。
さらに、最新技術との融合により、QFDの効果を最大限に引き出すことができます。
製造業が常に進化し続ける中で、QFDはその発展を支える重要なツールです。
これからもQFDを活用し、より良い製品を生み出すための取り組みを続けていくことが求められます。
資料ダウンロード
QCD管理受発注クラウド「newji」は、受発注部門で必要なQCD管理全てを備えた、現場特化型兼クラウド型の今世紀最高の受発注管理システムとなります。
ユーザー登録
受発注業務の効率化だけでなく、システムを導入することで、コスト削減や製品・資材のステータス可視化のほか、属人化していた受発注情報の共有化による内部不正防止や統制にも役立ちます。
NEWJI DX
製造業に特化したデジタルトランスフォーメーション(DX)の実現を目指す請負開発型のコンサルティングサービスです。AI、iPaaS、および先端の技術を駆使して、製造プロセスの効率化、業務効率化、チームワーク強化、コスト削減、品質向上を実現します。このサービスは、製造業の課題を深く理解し、それに対する最適なデジタルソリューションを提供することで、企業が持続的な成長とイノベーションを達成できるようサポートします。
製造業ニュース解説
製造業、主に購買・調達部門にお勤めの方々に向けた情報を配信しております。
新任の方やベテランの方、管理職を対象とした幅広いコンテンツをご用意しております。
お問い合わせ
コストダウンが利益に直結する術だと理解していても、なかなか前に進めることができない状況。そんな時は、newjiのコストダウン自動化機能で大きく利益貢献しよう!
(β版非公開)