- お役立ち記事
- Practicing Motion Economy to fundamentally improve work efficiency in manufacturing
Practicing Motion Economy to fundamentally improve work efficiency in manufacturing
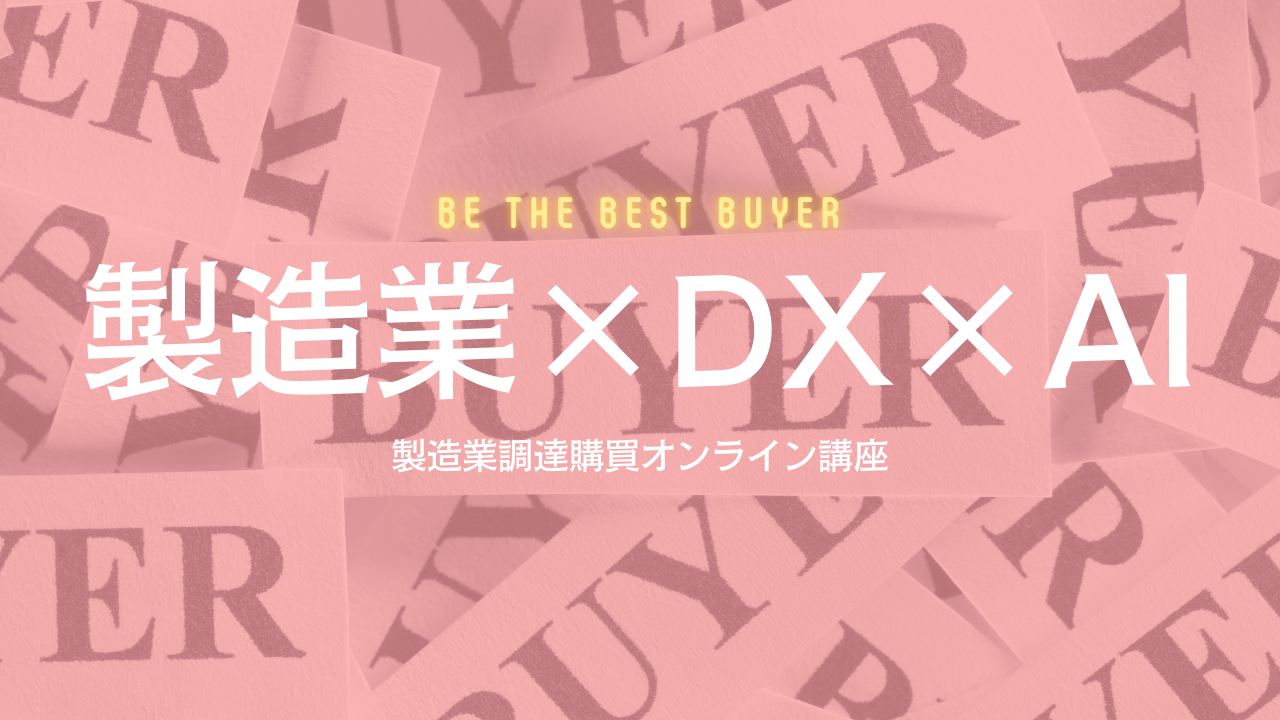
The manufacturing industry is always looking for ways to improve work efficiency and output. One approach that can make a big difference is practicing motion economy. Motion economy focuses on minimizing unnecessary motions and movements during work to improve productivity. By analyzing workflows and redesigning processes, you can significantly cut down on wasted time and effort.
目次
What is motion economy?
At its core, motion economy is about streamlining motions and movements. Anytime a worker has to reach, bend, or turn unnecessarily, it introduces inefficiencies. Motion economy aims to remove these inefficient motions by arranging tools, materials, and workflows in a smoother sequence. The goal is to allow workers to perform tasks with minimal physical exertion and in the most direct path possible.
Frank and Lillian Gilbreth were pioneers of motion economy in the early 20th century. As industrial engineers, they studied workflows frame-by-frame to identify opportunities to simplify motions. Some of their innovations include introducing chutes and slides to transport materials, arranging tools within easy reach, and improving workplace layouts. The Gilbreths helped popularize the concepts of motion economy and introduced new process design techniques. Their work formed the basis for modern principles of ergonomics and workflow optimization.
How can you implement motion economy in your manufacturing operations?
Here are some practical steps:
– Analyze workflows – Video record employees performing tasks to study their motions. Note any reaching, twisting, bending, or extra steps. This will uncover opportunities to streamline.
– Rearrange workstations – Organize tools, machinery, materials, and controls to minimize the distances workers must travel or stretches they must make. Imagine if items were closer or within arm’s reach.
– Simplify processes – Break tasks down into individual steps and remove any that do not add value. Combine steps if possible. The goal is straightforward, direct motions with no unnecessary movements in between.
– Use slides and chutes – Transport parts and materials between workstations without lifting or carrying. Gravity slides and angled chutes can significantly reduce lifting, bending, and walking.
– Improve layout – Arrange work areas in logical, efficient sequences so materials flow smoothly from one process to the next with minimal backtracking. Consider a U-shaped or straight line layout.
– Delegate lifting tasks – Avoid heavy lifting through use of hoists, cranes, carts, or powered conveyors if possible. Alternatively, assign lifting duties to workers best able to handle weight.
– Provide sitting workstations – Standing for long periods is fatiguing. Incorporate adjustable stools, chairs, or drafting tables so workers can perform tasks seated if safety allows. This reduces leg and back strain.
– Redesign tools – Modify tool handles, triggers or foot pedals so they don’t require an awkward grip or position to operate. Tool redesign was a Gilbreths specialty. Palm buttons reduce twisting.
– Empower workers – Solicit frontline employee input when planning workflow changes. Those doing the tasks daily have invaluable intuition about better ways to work. Incorporate their ideas whenever practical.
Practicing motion economy is an ongoing effort that yields compounding benefits over time as processes are continually refined. Keep monitoring for additional tweaks after changes are implemented since new inefficiencies may appear elsewhere down the line. With a diligent, team-oriented approach, manufacturers can substantially upgrade work ergonomics, productivity and quality through motion economy principles. The physical burden on workers is reduced while motivation and output increase.
In summary, motion economy is a proven strategy for manufacturing industry to fundamentally improve work efficiency. By analyzing motions and redesigning workflows, unnecessary movements and physical stress can be eliminated from production processes. The result is higher throughput, improved worker health, reduced fatigue and injury risk – all leading to greater business success over the long term. Implementing even small changes according to motion economy guidelines can significantly optimize operations.
資料ダウンロード
QCD調達購買管理クラウド「newji」は、調達購買部門で必要なQCD管理全てを備えた、現場特化型兼クラウド型の今世紀最高の購買管理システムとなります。
ユーザー登録
調達購買業務の効率化だけでなく、システムを導入することで、コスト削減や製品・資材のステータス可視化のほか、属人化していた購買情報の共有化による内部不正防止や統制にも役立ちます。
NEWJI DX
製造業に特化したデジタルトランスフォーメーション(DX)の実現を目指す請負開発型のコンサルティングサービスです。AI、iPaaS、および先端の技術を駆使して、製造プロセスの効率化、業務効率化、チームワーク強化、コスト削減、品質向上を実現します。このサービスは、製造業の課題を深く理解し、それに対する最適なデジタルソリューションを提供することで、企業が持続的な成長とイノベーションを達成できるようサポートします。
オンライン講座
製造業、主に購買・調達部門にお勤めの方々に向けた情報を配信しております。
新任の方やベテランの方、管理職を対象とした幅広いコンテンツをご用意しております。
お問い合わせ
コストダウンが利益に直結する術だと理解していても、なかなか前に進めることができない状況。そんな時は、newjiのコストダウン自動化機能で大きく利益貢献しよう!
(Β版非公開)