- お役立ち記事
- 摩擦溶接と超音波溶接の違い
月間76,176名の
製造業ご担当者様が閲覧しています*
*2025年3月31日現在のGoogle Analyticsのデータより
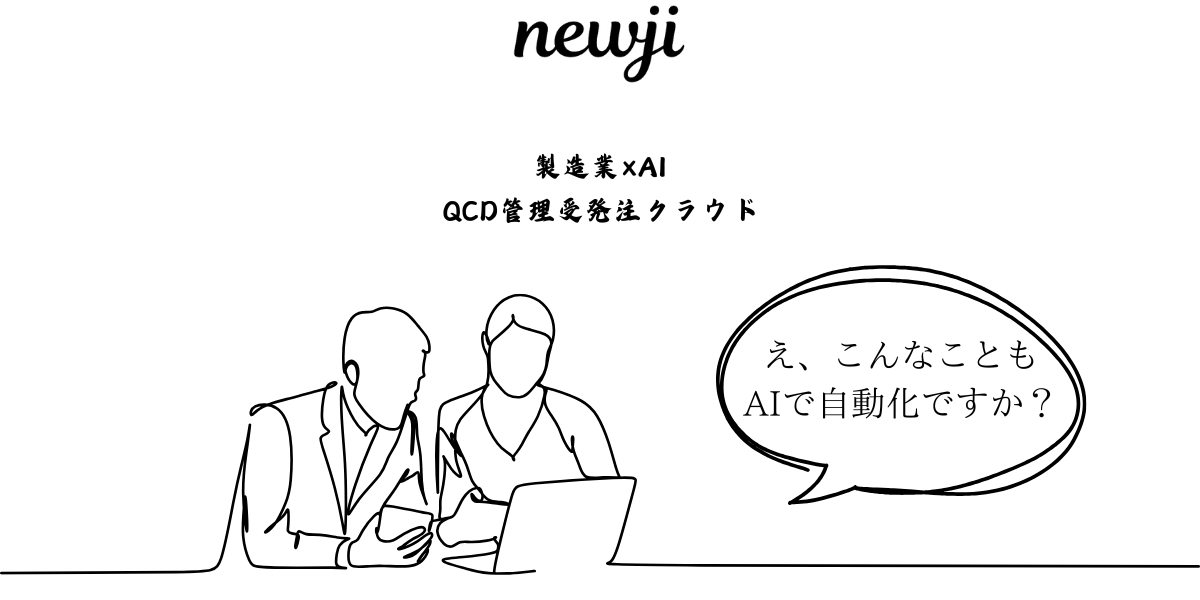
摩擦溶接と超音波溶接の違い
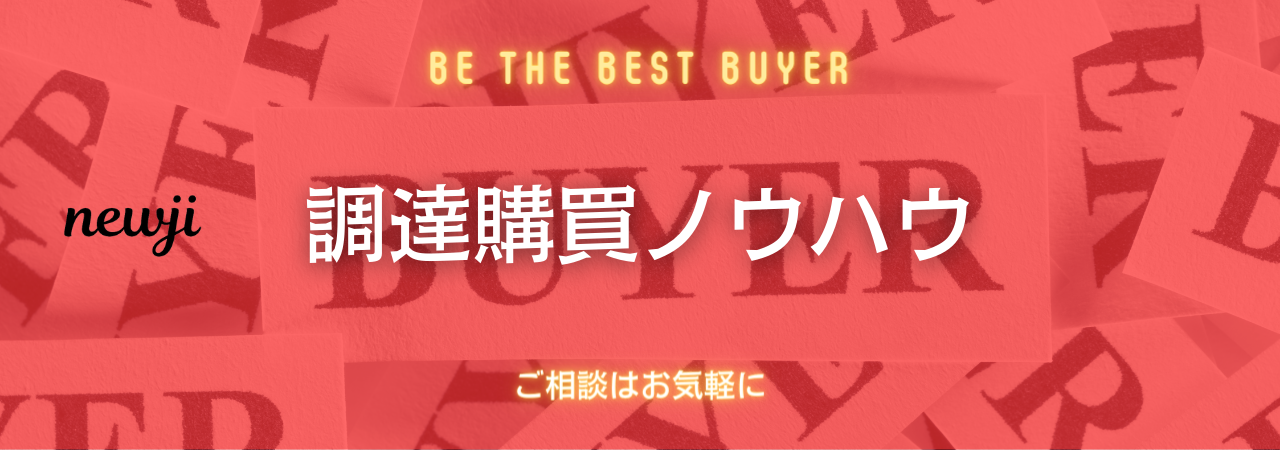
目次
摩擦溶接と超音波溶接の概要
摩擦溶接と超音波溶接は、いずれも溶接技術の一種であり、異なる物理的原理を利用して部材を接合する方法です。
これらの技術は、自動車や航空宇宙産業、電気製品など広範な分野で利用されています。
まずは、それぞれの技術の基本原理と特徴を理解することが大切です。
摩擦溶接の基本原理と特徴
摩擦溶接は、二つの部材を互いに押し付けて高速で相対運動させることにより生成される摩擦熱を利用して接合する方法です。
この方法では、摩擦によって部材の接触面が塑性変形し、溶融状態に近づくため、接合が行われます。
以下が摩擦溶接の主要な特徴です。
– **熱影響が少ない**:摩擦熱は限定された範囲で生成されるため、接合部以外の材質に熱影響が少ないです。
– **強度が高い**:溶接後の接合部の強度が元の材質と同等かそれ以上になることが多く、強固な結合が得られます。
– **材料適応性が広い**:異なる金属材料同士でも接合ができる場合が多いです。
– **自動化の容易さ**:プロセスの自動制御がしやすく、高精度な溶接が可能です。
超音波溶接の基本原理と特徴
超音波溶接は、高周波の超音波振動を利用して部材を接合する方法です。
このプロセスでは、超音波エネルギーが高速で振動する溶接装置により生成され、その結果として接触面が局所的に熱せられ、接合されます。
以下が超音波溶接の主要な特徴です。
– **高速作業**:超音波溶接は非常に短時間で接合が完了するため、生産効率が高いです。
– **低いエネルギー消費**:超音波溶接に必要なエネルギーは比較的少なく、エネルギー効率が良いです。
– **精密な作業が可能**:微細な部品や薄い材料の接合が得意であり、微細電子機器の製造に適しています。
– **異材料接合が難しい**:異種材料の接合には適していない場合があります。
技術の適用範囲
摩擦溶接と超音波溶接は、それぞれ異なる特性を持っているため、適用範囲や用いられる産業も異なります。
それぞれの技術がどのような分野で活用されているのかを見てみましょう。
摩擦溶接の適用分野
摩擦溶接は、金属材料の接合に特に適しており、自動車産業や航空宇宙産業で広く利用されています。
具体的な適用例としては以下のようなものがあります。
– **自動車部品**:エンジン部品や車体フレームの接合
– **航空宇宙**:航空機の構造部品の接合
– **鉄道**:鉄道車両の部品接合
– **重機・建設機械**:耐久性が求められる部品の接合
摩擦溶接は強度が求められる部品や異なる金属材料の接合に優れているため、その適用範囲は広範です。
超音波溶接の適用分野
超音波溶接はプラスチックなどの合成材料の接合に特化しており、多くの産業で活用されています。
以下は超音波溶接の具体的な適用例です。
– **電子機器**:スマートフォンやタブレットの組み立て
– **医療機器**:使い捨て医療機器の接合
– **パッケージング**:食品や医薬品の包装
– **玩具・消費財**:プラスチック部品の接合
超音波溶接は精密な作業が求められる製品や大量生産に適しており、多様な製品の製造に利用されています。
メリットとデメリット
それぞれの溶接技術には特有のメリットとデメリットがあります。
これらを理解することで、どの溶接技術が最適かを判断する助けとなります。
摩擦溶接のメリットとデメリット
摩擦溶接には以下のようなメリットがあります。
– **高強度接合**:接合部は母材と同等以上の強度を持つことが多いため、強固な結合が得られます。
– **少ない熱影響**:接合部以外の材質に対する熱の影響が少ないため、材料特性を維持することができます。
– **異種金属接合**:異なる金属材料同士でも接合ができるため、設計の自由度が高まります。
ただし、以下のようなデメリットも存在します。
– **高価な装置**:摩擦溶接装置は高価であり、初期投資が大きいです。
– **振動による影響**:プロセス中の振動が他の装置や部品に影響を及ぼす場合があります。
超音波溶接のメリットとデメリット
超音波溶接には以下のようなメリットがあります。
– **高速作業**:短時間で接合が完了するため、生産効率が向上します。
– **低エネルギー消費**:少ないエネルギーで接合ができるため、ランニングコストが低いです。
– **精密接合**:微細な部品や薄い材料を精密に接合できるため、電子機器や医療機器の製造に適しています。
デメリットとしては以下の点が挙げられます。
– **異材料接合の難しさ**:異なる材料の接合には適さない場合が多いです。
– **騒音**:超音波振動により作業環境に騒音が発生することがあります。
最新技術動向
摩擦溶接と超音波溶接の技術は、日々進化を続けています。
最新技術動向に目を向けることで、将来的な技術の発展や新しい応用例に対応することができます。
摩擦溶接の最新技術動向
摩擦溶接の技術は、より高度で特殊な要求に応えるために進化しています。
– **摩擦攪拌接合(FSW)**:高精度・高強度の接合を実現する技術。
航空宇宙産業や船舶産業での応用が進んでいます。
– **ライン摩擦溶接**:複数の摩擦溶接を直線的に配置することにより、長尺材の接合に対応する技術。
– **AIと機械学習の導入**:溶接プロセスの最適化や不良予測を行うためにAI技術が導入されています。
超音波溶接の最新技術動向
超音波溶接もまた、新しい技術と融合して進化を続けています。
– **レーザーアシスト超音波溶接**:レーザー技術を併用することで、難接合材料への対応範囲を広げる試み。
– **高速自動化ライン**:ロボットと連携した自動化ラインにより、生産効率をさらに向上させる技術。
– **ナノスケールの接合**:微細構造やナノサイズの部品を精密に接合するための技術開発が進められています。
まとめ
摩擦溶接と超音波溶接は、それぞれ異なる特性と利点を持つ溶接技術です。
摩擦溶接は、高強度な接合が必要な金属部品の接合に適しており、異種金属の接合にも対応できるため、自動車や航空宇宙産業で広く利用されています。
一方、超音波溶接は、プラスチックや微細な部品の接合に適しており、電子機器や医療機器などの製造において重要な役割を果たしています。
それぞれの溶接技術の特性と最新動向を理解し、適宜に採用することで、生産効率の向上や新たな製品開発に寄与することができます。
今後も技術の進化を注視し、最適な溶接技術を選択していくことが求められます。
資料ダウンロード
QCD管理受発注クラウド「newji」は、受発注部門で必要なQCD管理全てを備えた、現場特化型兼クラウド型の今世紀最高の受発注管理システムとなります。
ユーザー登録
受発注業務の効率化だけでなく、システムを導入することで、コスト削減や製品・資材のステータス可視化のほか、属人化していた受発注情報の共有化による内部不正防止や統制にも役立ちます。
NEWJI DX
製造業に特化したデジタルトランスフォーメーション(DX)の実現を目指す請負開発型のコンサルティングサービスです。AI、iPaaS、および先端の技術を駆使して、製造プロセスの効率化、業務効率化、チームワーク強化、コスト削減、品質向上を実現します。このサービスは、製造業の課題を深く理解し、それに対する最適なデジタルソリューションを提供することで、企業が持続的な成長とイノベーションを達成できるようサポートします。
製造業ニュース解説
製造業、主に購買・調達部門にお勤めの方々に向けた情報を配信しております。
新任の方やベテランの方、管理職を対象とした幅広いコンテンツをご用意しております。
お問い合わせ
コストダウンが利益に直結する術だと理解していても、なかなか前に進めることができない状況。そんな時は、newjiのコストダウン自動化機能で大きく利益貢献しよう!
(β版非公開)