- お役立ち記事
- トヨタもBMWもやっている、リーン生産方式の比較
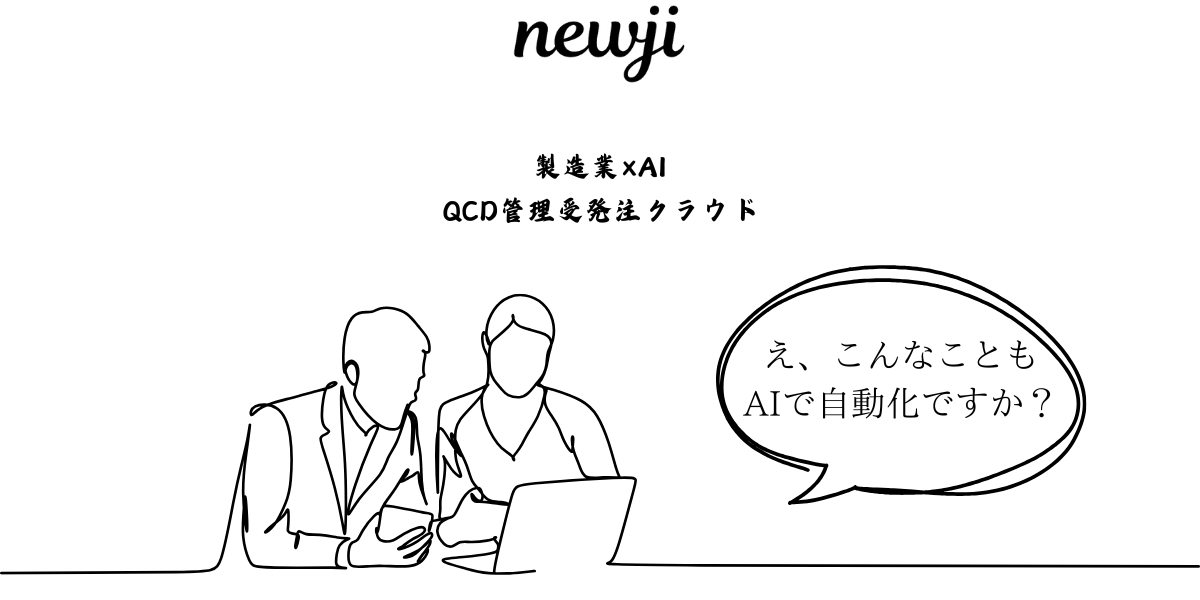
トヨタもBMWもやっている、リーン生産方式の比較
これまで話をしてきましたリーン生産の詳しい話を
引き続きしていきたいと思います
リーン生産ってそもそも何
無駄のない生産活動ということなんですけれども
これ元々購買であった考え方をトヨタが自分たちのものにして
それを高度経済成長期に自分たちの生産ラインに取り込んで
それが世界で注目されて、逆に逆輸入という形でトヨタのリーン生産方式が
世界の工場で広まったっていうのが高度経済成長期
これは単一品目をいかに大量生産する中で
無駄を無くすかという話ですね
プロセス管理を徹底して効率化することで、従来の大量生産方式と同等以上の品質を実現しながらも作業時間や在庫量が大幅に削減できる生産方式
無駄の話についてはそのトヨタって言われる
7つの無駄っていう話もしましたけど
もう1回ここでこの7つの無駄を繰り返してみようと思います
作りすぎのムダが1個目
2つ目が手持ちの無駄
3つ目、運搬の無駄
4つ目、加工そのものの無駄
5つ目、在庫の無駄
6つ目、動作の無駄
7つ目、不良を作る無駄
という風になるんですけれども
簡単にこの無駄がそぎ落とせるかというのはなかなか実は難しい
なんで現状の今の姿になのか?
いろんな訳があって無駄が生じてるんですけど
じゃあそれすぐ直せ、減らせと言って
簡単にできるんだったらみんなやってます
なんでできないか
いろんな理由があるんですよね
その理由を見つけ出してひとつひとつつぶして
そういう言い訳をさせないようにして
無駄をなくしていくということになるんですけれども
この無駄に対する考え方、私が経験したBMWの工場とトヨタでは大きく違います
トヨタは比較的似たような車種、それから量産品
オプションもそんなに沢山無いという中でとにかく大量生産で安くする
1個の部品をできるだけ安く買うために
とにかく車
例えばカローラとか、マークⅡとか
たくさん作ってたくさん作ってプリウスもそうですけど
たくさん作ってどれだけコストを下げるか
例えばプリウスなんかも
第1世代と第2世代で調達コストが劇的に下がったんですね
これもその改善っていう本に書かれてましたけれど
初代プリウスから2代目に変わる時に
調達コストが40パーセント近く下がったって言うんですね
それだけ生産台数が増えた、技術力が上がった
ハイブリッド車っていう車の生産に工場が慣れた
色んなことが相乗効果として現れた結果として、コストが下がったんですね
黙っててコストが下がったわけじゃなくて
単にボリュームディスカウントで下がっただけじゃなくて
何年も5年も6年も作り続けられた
プリウスが改良されて第2世代になりました
フルモデルチェンジになりました
と言いながら燃料電池の技術が更に
軽量化、小型化、高出力化、改良されて
同じコストでもっと出力が出るとか
走行距離が長くなるとか
いやもっと小さくコンパクトで軽量で同じ出力、同じ走行距離出るよ
というふうな改良だとか
色んなことがなされた上で
初代のプリウスで勉強したことを2代目
今3代4代目っていうのをどんどん積んでますけれど
それに活かして次から次へと上に積み重ねる形で
改善、改良が進み生産ラインも作業する人たちも
慣れてスピードが上がって
同じ時間でもっとたくさん台数が増えてる
原材料も在庫も数量も絞り、どれだけ売れるから
どれだけ調達したらいいね
っていうのが分かってきて
その学習効果、過去の実績
色んな失敗も含めてそれが活かされて
次にっていう風になってる訳ですよね
大事なのは継続性の話ですよ
今までこうだった
だから次こう改良してその先に行くというのがその延長線上にあるから
これ全く違う方向だと今までの経験に活きない
活かしたことが次の世代の次の製品に
プラスになって働く
コストでいけば削減という形で現れる
だから今言った7つの無駄
慣れてきていろんなことが改善された結果として
過剰在庫を持たないとボトルネックをなくして生産
どこで時間がかかるの、どこが短時間でスーっていけるの
だからそれに合わせて設備だとかロボットの配置だとか
作業人員だとか熟練工なのか
そうじゃなくてもいいのかいろんな改善がなされて
それも下請け外注先の協力も得て
無駄な動作も減り
どんどんどんどんコストが削減され
人件費も設備の費用も時間短縮にも っていうことですよね
方やBMWは量産の会社じゃないです
1台1台カスタマイズです
ボディカラー違う、内装も外装も違う
エンジンの排気量も違う
ドアの枚数も違う、セダンとクーペと
ツーリングとグランクーぺと
全部ボディパーツ形状違う
ただし足回り例えばエンジンだとか
こういった部分は排気量が同じだったら共通
車の中でどこが手間暇(隙)かかる
コストがかかっているか
どこを共通にすれば
生産効率が上がるか、開発コストが減るか
もっとレベルの高い製品が作れるか
BMWは3シリーズのフルモデルチェンジの時に
全ていっぺんにフルモデルチェンジになるわけじゃなくて
3、5、7それぞれモデルチェンジの時期、年が違うので
必ずその3シリーズの改良が
次の5シリーズや7シリーズに活かされるっていう風に引き継がれる
それもトヨタのような
クラウンとかカローラとかプリウスとかっていう
縦割りの工場じゃなくて
BMWの場合は7シリーズだろうが3シリーズだろうが
同じ3000ccのエンジンだったら基本、パーツは一緒
ボディが違うから全て同じわけじゃないんですけど
基本的なところは共通です
だからBMWに
トヨタのカローラとかプリウスとかっていう名前がないのは
基本的にBMWのブランドは1つなんですね
トヨタはあれだけの規模でありながら
全部縦割り
最近は車種を共通化しようという取り組みを始めてやっと数年経ちました
気が付いたら
その方が効率的だから
コスト削減や業務の効率化、開発ですごく有利っていうのが分かった
それBMWが(から)学んだから
BMWと共同で
Z4と86の共同開発して
あ、そういうことねって分かった
だけれどBMWは何十年も前から
そういうことやってた訳ですよね
1970年代から
それによって1台1台カスタマイズでありながら
1、3、5、7、8間の2、4、6も含めて
基本的なものが共通だったりすると
1台1台カスタマイズなのに実は部品の共通化が図れてる
標準化が図れている結果
すごい生産効率がいい
お客様にとっては自分の車、世界に1台のカスタマイズされた車
だけど作る側にとってみればここ共通、ここ共通、その組み合わせの違いで
バラエティの富んだ世界に1台1台、別々の車が出来上がる
どっちが無駄かトヨタの規模があってだけど
車種別で工場が別々で縦割りだと
それで設計や部品が共通化されてないと
どれだけ非効率か
共通化されている部品もたくさんありますもちろん
だけどそれが全てじゃない、設計思想が違ったりすると
基本的なところが違ったりすると
ほんのわずかの違いで相互に使えない
これが使えるとどうなるか
これがBMWとトヨタの差
だからリーン生産、無駄をなくすっていう考え方の視点が全然違う訳ですよね
だからその話を私は中国で三一重工でしました
コンクリートポンプ車、クレーン車
油圧ショベル、ダンプカー
共通化できるものは共通化しましょうよと
してなかったんですね
完全に縦割り
工場も別、東北の瀋陽と
上海と湖南省の と長沙と
さらに広東省、 と
さらにチベットウイグル自治区のウルムチに工場もあって
製品ごとでエンジン別、ボディパーツ別、運転席別
シートも別、人間が素晴らしいとなって共通でいいのに
なんで別々なの?になっちゃいますよね
だからそういった無駄をなくしますって
工場の無駄を無くす前に
もっとなくす無駄ってあるじゃないですか
それを突き詰めて改善しない限り
購買が日頃買っているパーツが共通化しなければ
サプライヤーが一緒にならなければ
納期バラバラだし
サプライヤーの生産現場も
共通化が標準化ができてなければ
それごとで機械の型を変えなきゃいけないとか
工具を取り替えなきゃいけないとか
っていう無駄が発生する訳ですね
だから川上にさかのぼって設計段階から無駄をなくす
っていうことをしていかないと
競争相手がそういう取り組みをしてるんだったら
その競争に勝てない
ぜひそのリーン生産、カンバン方式、在庫ゼロ
色んな話ありますけれども
それはもちろん大事ですが
それは根本的な設計の段階の無駄から
取り組んだ結果として生産ラインで起きてる無駄を
だからここが無駄だから
これをなくしましょうっていうのが次の話ですよね
トヨタはそれをやらないで根本をやらないで
手先の生産技術の話ばっかりずっとしてきたから
数年前に慌ててそれに気が付いてプラットフォーム共通化します
言ってたけど、遅すぎますよっていうことです
なのでリーン生産における7つの無駄
1個1個潰すのも大事ですけれども根本となる部分を設計
研究開発部門
そういった話
設計や形状の変更になるためには
アフターサービス部門とか
営業部門のお客様の声が必要になるんですけど
それを含めてぜひ取り組んでほしい
時間がかかる話ですけれども
購買部門単独でできない話ですけれども
共通する話題だと思うので
ぜひいろんな部門を巻き込んで
改善に取り組んでほしいと思います
今日はここまでにしますが
このリーン生産、7つの無駄だとかカンバン方式とか
まだまだいっぱいいっぱい面白い話あります
私が食品スーパーのテスコ、イオンで学んだこと
それからそこでまだまだできなかったことを
もっとこうしたらいいなと思ったこと
これが製造業、メーカーに活かせることとかいっぱいあります
またまたそういった話もしていきたいと思いますので
ぜひ引き続きNEWJIチャンネルで私の話、聞いてほしいなと思います
私もできるだけ参考になる情報を発信していきたいと思います
ぜひコメント、高評価ボタン
チャンネル登録、アドバンスコースの専門的な話
ぜひ聞いてほしいと思います
今日は以上です
資料ダウンロード
QCD調達購買管理クラウド「newji」は、調達購買部門で必要なQCD管理全てを備えた、現場特化型兼クラウド型の今世紀最高の購買管理システムとなります。
ユーザー登録
調達購買業務の効率化だけでなく、システムを導入することで、コスト削減や製品・資材のステータス可視化のほか、属人化していた購買情報の共有化による内部不正防止や統制にも役立ちます。
NEWJI DX
製造業に特化したデジタルトランスフォーメーション(DX)の実現を目指す請負開発型のコンサルティングサービスです。AI、iPaaS、および先端の技術を駆使して、製造プロセスの効率化、業務効率化、チームワーク強化、コスト削減、品質向上を実現します。このサービスは、製造業の課題を深く理解し、それに対する最適なデジタルソリューションを提供することで、企業が持続的な成長とイノベーションを達成できるようサポートします。
オンライン講座
製造業、主に購買・調達部門にお勤めの方々に向けた情報を配信しております。
新任の方やベテランの方、管理職を対象とした幅広いコンテンツをご用意しております。
お問い合わせ
コストダウンが利益に直結する術だと理解していても、なかなか前に進めることができない状況。そんな時は、newjiのコストダウン自動化機能で大きく利益貢献しよう!
(Β版非公開)