- お役立ち記事
- Building Automated Quality Assurance Systems Using Sensor Technology
Building Automated Quality Assurance Systems Using Sensor Technology
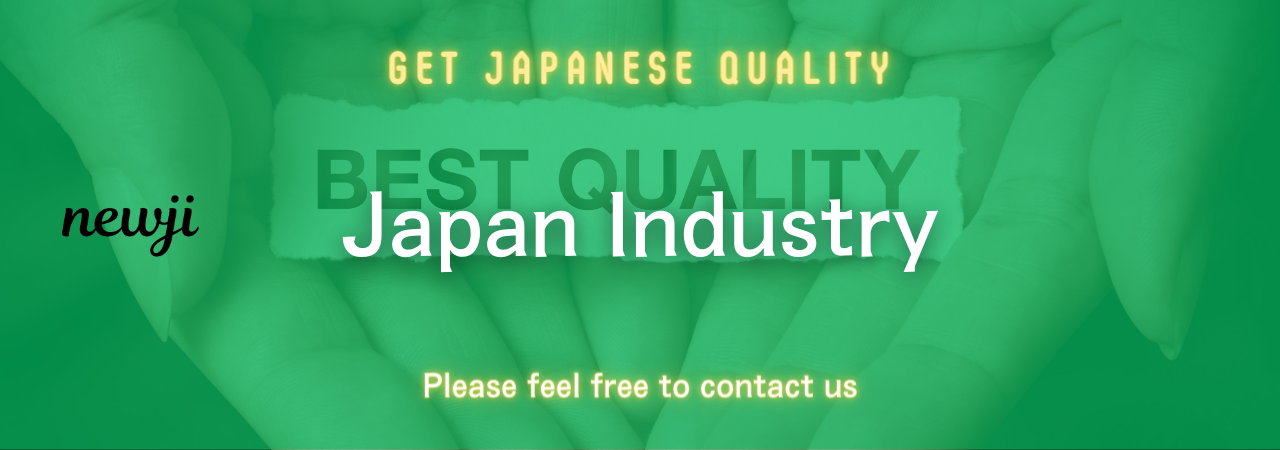
目次
Understanding Quality Assurance Systems
Quality assurance (QA) is a fundamental part of any production process, ensuring that the final products meet certain predetermined standards.
In many industries, QA is not just a requirement but a crucial component that dictates customer satisfaction and maintains brand reputation.
Traditionally, quality assurance systems have relied on human oversight and manual inspections.
However, the advent of advanced technology, particularly sensor technology, is revolutionizing how QA systems operate.
The Role of Sensor Technology in QA
Sensor technology involves the use of devices that detect physical properties, such as temperature, pressure, or motion, and relay this information for analysis.
These sensors can be integrated into production lines to continuously monitor and collect data on various aspects of the manufacturing process.
This data can then be analyzed to ensure products are being produced according to specific standards.
With sensors, deviations from the norm can be detected in real-time, allowing for immediate corrective action.
This not only improves efficiency but also reduces the risk of defective products reaching the consumer.
Types of Sensors Used in QA
There are numerous types of sensors used in industrial QA systems, each designed to measure specific variables.
For instance, temperature sensors can monitor the heat levels in processes where precise temperature control is critical.
Pressure sensors are used in situations where maintaining a constant pressure is necessary.
Proximity sensors can detect the presence or absence of an object, helping in assembly line accuracy.
Other types include humidity sensors, pH sensors, and motion sensors, each playing a unique role in maintaining quality.
Benefits of Automated QA Systems
One of the major advantages of automating QA is efficiency.
With automated systems, continuous monitoring is possible 24/7 without the need for human intervention.
This leads to faster detection of faults and less downtime since issues can be resolved quickly.
Additionally, automated systems provide consistency in inspections, eliminating human error and subjective judgments.
Automated systems also generate vast amounts of data which can be used for further analysis and improvement.
With this data, companies can identify patterns that suggest inefficiencies or machinery nearing the end of its useful life, enabling them to take proactive measures.
Challenges in Implementing Sensor Technology
Despite its benefits, integrating sensor technology into QA systems comes with challenges.
The initial cost of setting up an automated system can be significant, requiring not just the sensors but also software and training.
Moreover, companies need to consider the compatibility of these new technologies with their existing machinery and processes.
There is also the challenge of data management.
Automated systems generate large volumes of data, which must be effectively managed, stored, and analyzed.
This requires robust IT infrastructure and skilled personnel capable of interpreting the data.
Ensuring Data Security
With increased reliance on data, companies must be vigilant about data security.
Sensitive information collected by sensors should be protected from unauthorized access or cyber threats.
Implementing strong security measures is crucial for maintaining the integrity of the QA systems and protecting company and consumer interests.
The Future of QA in Manufacturing
The integration of sensor technology into QA systems is only the beginning.
Future developments in artificial intelligence (AI) and machine learning are expected to further enhance these systems.
AI can complement sensor technologies by providing predictive analytics, which can forecast potential faults before they occur.
Machine learning algorithms can learn from past data to improve accuracy over time.
They also enable adaptive systems that can automatically adjust production processes for optimal performance.
Adapting to Technological Advances
Manufacturers will need to stay abreast of these technological advancements and be ready to adapt.
Continuous staff training and investment in new technologies will be crucial.
Companies that successfully integrate these technologies into their QA systems will likely gain a competitive edge through improved product quality and lower operational costs.
Conclusion
Building automated quality assurance systems using sensor technology represents a significant advancement for many industries.
While the initial investment and integration challenges exist, the benefits of increased efficiency, consistent product quality, and vast data insights are undeniable.
As technology continues to evolve, companies will find new opportunities to enhance their QA systems, resulting in better products and greater customer satisfaction.
Embracing these innovations is key to not only ensuring quality but also securing a successful future in the ever-competitive marketplace.
資料ダウンロード
QCD調達購買管理クラウド「newji」は、調達購買部門で必要なQCD管理全てを備えた、現場特化型兼クラウド型の今世紀最高の購買管理システムとなります。
ユーザー登録
調達購買業務の効率化だけでなく、システムを導入することで、コスト削減や製品・資材のステータス可視化のほか、属人化していた購買情報の共有化による内部不正防止や統制にも役立ちます。
NEWJI DX
製造業に特化したデジタルトランスフォーメーション(DX)の実現を目指す請負開発型のコンサルティングサービスです。AI、iPaaS、および先端の技術を駆使して、製造プロセスの効率化、業務効率化、チームワーク強化、コスト削減、品質向上を実現します。このサービスは、製造業の課題を深く理解し、それに対する最適なデジタルソリューションを提供することで、企業が持続的な成長とイノベーションを達成できるようサポートします。
オンライン講座
製造業、主に購買・調達部門にお勤めの方々に向けた情報を配信しております。
新任の方やベテランの方、管理職を対象とした幅広いコンテンツをご用意しております。
お問い合わせ
コストダウンが利益に直結する術だと理解していても、なかなか前に進めることができない状況。そんな時は、newjiのコストダウン自動化機能で大きく利益貢献しよう!
(Β版非公開)