- お役立ち記事
- Tips for Optimizing Molding Cycles in Insert Molding
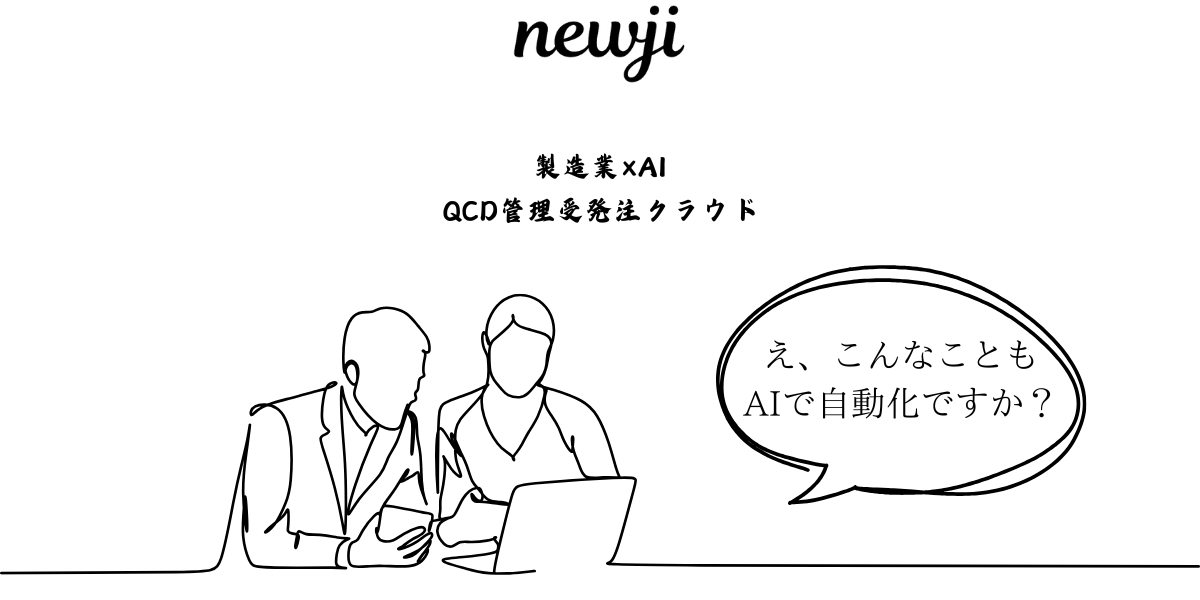
Tips for Optimizing Molding Cycles in Insert Molding
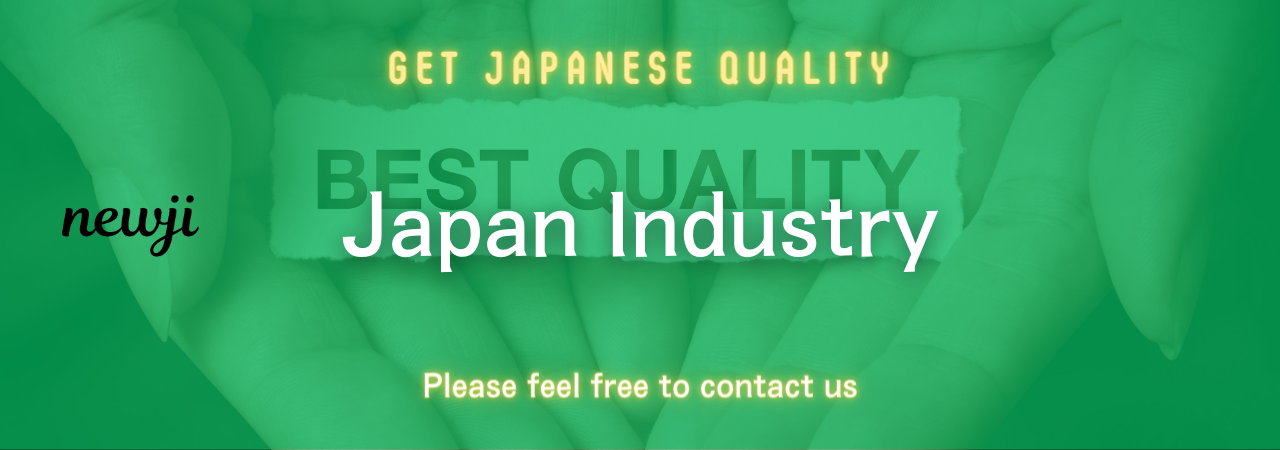
目次
Understanding Insert Molding
Insert molding is a specialized manufacturing process wherein pre-made components, often made from metal or other materials, are placed into a mold before injecting plastic resin around them.
This process creates a single, integrated part by combining different materials, offering enhanced structural and functional properties.
It’s widely used in various industries such as automotive, electronics, medical devices, and consumer goods due to its capability to produce parts with complex designs and enhanced durability.
Simply put, insert molding integrates multiple components into a cohesive unit in one efficient step.
Importance of Molding Cycles
The molding cycle in insert molding is crucial as it directly impacts the quality, efficiency, and cost of the production process.
A molding cycle is comprised of several phases: mold closing, injection of the material, cooling, ejection, and mold opening.
Optimizing these cycles can lead to faster production times, reduce material waste, and improve the overall quality of the finished product.
Understanding and controlling each phase of the molding cycle can significantly enhance the effectiveness of the insert molding process.
Key Factors Affecting Molding Cycles
Material Selection
Material selection plays a significant role in molding cycles.
Different materials have varying melting points, cooling times, and flow characteristics which can affect the cycle time and quality of the molded part.
Choosing the right material for the specific requirements of a product is integral.
Consulting with material specialists can provide insights into the best materials considering the target application’s environmental factors and mechanical stresses.
Mold Design
A well-designed mold can substantially reduce production time, costs, and minimize defects in the finished product.
Key elements like the mold’s complexity, the cooling system, and the injection points must be carefully considered during the design phase.
A balanced and well-designed cooling system can dramatically reduce cooling times, which typically constitute a significant portion of the cycle time.
Employing effective mold design strategies is essential for efficient insert molding.
Machine Calibration
Calibration of the molding machinery ensures that each phase of the molding cycle operates at optimal efficiency.
Regular checks and maintenance prevent deviations from preset parameters, such as temperature, pressure, and injection speed, which can compromise part quality and cycle time.
Investing time in proper machine setup and maintenance can prevent production delays and avoid costly defects.
Process Parameters
Fine-tuning process parameters like injection speed, pressure, and cooling time is crucial for optimal output.
These parameters must be tailored to the specific material and part design.
Using process simulations and robust monitoring systems can help in identifying the best settings for efficient and consistent production.
Real-time adjustments based on empirical data can lead to significant improvements in cycle efficiency.
Tips for Optimizing Molding Cycles
Invest in Advanced Technology
Integrating advanced technologies like automated systems and real-time monitoring can significantly enhance cycle efficiency.
Automated systems can streamline operations, reduce human error, and improve precision in repetitive tasks.
Implementing real-time monitoring helps in tracking performance, allowing for quick identification and correction of any process anomalies.
Continuous Training and Skill Development
Employees are a crucial link in the manufacturing chain.
Investing in continuous training programs ensures that staff are skilled in operating and troubleshooting advanced machinery.
Regular training sessions can keep teams updated on the latest techniques and technologies, enhancing their ability to optimize the molding cycles.
Analyze and Review Cycle Times Regularly
Regular analysis and review of cycle times can uncover hidden inefficiencies.
Maintaining detailed records of each cycle’s performance helps to identify trends and areas for improvement.
Utilizing comprehensive data analytics tools can provide deeper insights, enabling more informed decisions in the optimization process.
Implement Preventive Maintenance
Routine preventive maintenance can avert unforeseen breakdowns and improve machine efficiency.
Scheduled maintenance helps in identifying potential issues before they cause significant disruptions.
Ensuring that machinery is consistently in peak condition maintains the efficiency of molding cycles over time.
Collaborate with Material and Tooling Experts
Collaborating with experts in material science and tooling design can offer valuable perspectives and solutions.
These collaborations can lead to the development of innovative solutions that optimize material use and tooling design, directly impacting cycle times.
Stepping outside the internal team can provide fresh insights and drive process improvements.
Conclusion
Optimizing molding cycles in insert molding is a multidimensional task involving factors like material selection, mold design, machine calibration, and process parameters.
By implementing advanced technologies, continuous training, regular cycle reviews, preventive maintenance, and expert collaborations, manufacturers can significantly enhance the efficiency and quality of their production processes.
Adapting to new strategies and technologies not only reduces operational costs but also improves product quality, ensuring better satisfaction and competitiveness in the market.
This proactive approach ensures that the insert molding process remains efficient, reliable, and economically sustainable.
資料ダウンロード
QCD調達購買管理クラウド「newji」は、調達購買部門で必要なQCD管理全てを備えた、現場特化型兼クラウド型の今世紀最高の購買管理システムとなります。
ユーザー登録
調達購買業務の効率化だけでなく、システムを導入することで、コスト削減や製品・資材のステータス可視化のほか、属人化していた購買情報の共有化による内部不正防止や統制にも役立ちます。
NEWJI DX
製造業に特化したデジタルトランスフォーメーション(DX)の実現を目指す請負開発型のコンサルティングサービスです。AI、iPaaS、および先端の技術を駆使して、製造プロセスの効率化、業務効率化、チームワーク強化、コスト削減、品質向上を実現します。このサービスは、製造業の課題を深く理解し、それに対する最適なデジタルソリューションを提供することで、企業が持続的な成長とイノベーションを達成できるようサポートします。
オンライン講座
製造業、主に購買・調達部門にお勤めの方々に向けた情報を配信しております。
新任の方やベテランの方、管理職を対象とした幅広いコンテンツをご用意しております。
お問い合わせ
コストダウンが利益に直結する術だと理解していても、なかなか前に進めることができない状況。そんな時は、newjiのコストダウン自動化機能で大きく利益貢献しよう!
(Β版非公開)