- お役立ち記事
- Various reliability prediction techniques
この記事は、当社の提供するお役立ち記事の一部です。詳しくは公式サイトをご覧ください。
Various reliability prediction techniques
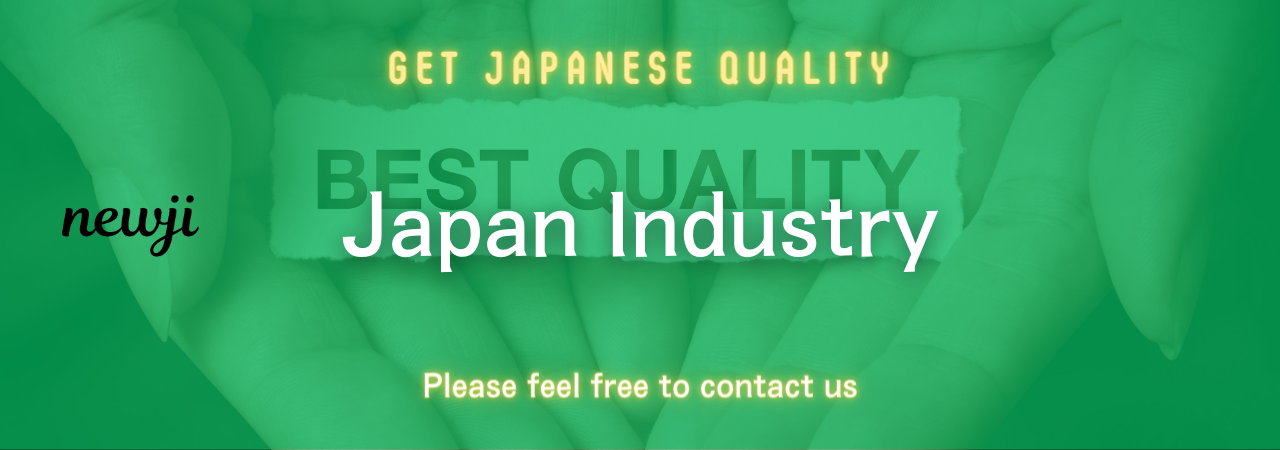
目次
Understanding Reliability Prediction
Reliability prediction is a crucial part of engineering and product development.
It helps engineers and manufacturers anticipate potential failures in products or systems, allowing them to enhance performance and safety.
But what exactly is reliability prediction, and what techniques are involved in achieving it?
What is Reliability Prediction?
Reliability prediction is the process of estimating the probability that a product or system will perform satisfactorily for a given period under specified conditions.
It involves assessing the likelihood of failure and understanding the factors that may influence it.
This prediction is vital for products that require high performance and safety standards, such as airplanes, medical devices, and automotive components.
Predicting reliability also involves understanding the lifecycle of a product from initial use to potential failure.
The data gathered during this period can be used to estimate when and how failures might occur, which helps in improving design and maintenance strategies.
Key Techniques in Reliability Prediction
There are several techniques used for predicting reliability, each with its unique methods and focus areas.
Below are some of the most commonly used techniques:
1. FMEA (Failure Mode and Effects Analysis)
FMEA is a systematic approach to identifying potential failure modes, understanding their causes and effects, and prioritizing actions to mitigate them.
By conducting FMEA, engineers can determine the parts of a system most likely to fail and implement strategies to prevent those failures.
FMEA involves creating a comprehensive list of potential failure modes, analyzing their effects, and prioritizing them based on severity, occurrence, and detectability.
This technique helps ensure that the most critical issues are addressed first.
2. Fault Tree Analysis (FTA)
Fault Tree Analysis is a top-down method that starts with a potential failure event and works backward to identify possible causes.
It involves creating a diagram that visually represents the connections between different system components and potential failure causes.
FTA helps engineers identify how combinations of lower-level failures can lead to a higher-level failure event.
By understanding these relationships, they can craft strategies to prevent such events from occurring.
3. Reliability Block Diagram (RBD)
RBD is a graphical method for analyzing the reliability of a system by modeling how component failures affect overall system performance.
In a reliability block diagram, system components are represented as blocks, and the connections between them indicate how failures may propagate through the system.
RBDs are particularly useful for understanding redundant systems or those with complex configurations.
They help in visualizing how component reliability impacts system reliability and determine which components most significantly affect overall performance.
4. Weibull Analysis
Weibull Analysis is a statistical technique used to model failure data and estimate the life characteristics of a product.
It provides valuable insights into the reliability and failure rates of products using a mathematical distribution known as the Weibull distribution.
This technique is particularly useful for identifying failure patterns and anticipating future failures.
For example, if a product follows a “wear-out” pattern, Weibull Analysis can help predict when the majority of failures are likely to occur, enabling better maintenance planning and resource allocation.
5. Monte Carlo Simulation
Monte Carlo Simulation uses random sampling and statistical modeling to estimate the probability of different outcomes in a process.
For reliability prediction, it involves simulating the operation of a system over time and accounting for random variations.
By running numerous simulations, Monte Carlo provides an estimation of how real-world uncertainties will impact a system’s reliability.
This technique is particularly helpful for complex systems with numerous interacting components and variables.
Importance of Reliability Prediction Techniques
Reliable systems are essential for ensuring safety, avoiding costly failures, and meeting customer expectations.
By employing reliability prediction techniques, companies can make informed decisions, enhance their product designs, and improve maintenance strategies.
Reliability prediction also contributes to cost savings.
Anticipating and mitigating potential failures reduce warranty costs, repair expenses, and the need for unplanned downtime.
Ultimately, this helps in delivering more durable products and enhancing customer satisfaction.
Moreover, reliability prediction aligns with quality assurance and control processes.
It ensures that systems operate within acceptable safety and performance limits, which is crucial in sectors subject to stringent regulatory requirements.
Challenges in Reliability Prediction
Despite its importance, reliability prediction is not without challenges.
Accurate predictions require comprehensive and high-quality data, which can be difficult to obtain.
Limited historical data or changes in manufacturing processes can impact the reliability of predictions.
Additionally, predicting reliability for complex systems involves accounting for numerous variables and interactions, which can complicate the modeling process.
Integrating new technologies, such as IoT and AI, is becoming increasingly vital in managing these complexities and improving prediction accuracy.
Conclusion
Reliability prediction techniques are indispensable tools for engineers and manufacturers.
They help ensure products perform as expected, meet safety standards, and satisfy customer requirements.
By leveraging techniques like FMEA, FTA, RBD, Weibull Analysis, and Monte Carlo Simulation, organizations can proactively address potential failures, leading to more reliable products and systems.
While challenges in data quality and system complexity exist, advancements in technology and analytical methods continue to enhance the ability to predict reliability with greater accuracy.
Choosing the right combination of techniques will depend on the specific requirements and nature of the product or system being analyzed, thereby creating a foundation for products that are both dependable and trust-worthy over their intended lifecycle.
資料ダウンロード
QCD調達購買管理クラウド「newji」は、調達購買部門で必要なQCD管理全てを備えた、現場特化型兼クラウド型の今世紀最高の購買管理システムとなります。
ユーザー登録
調達購買業務の効率化だけでなく、システムを導入することで、コスト削減や製品・資材のステータス可視化のほか、属人化していた購買情報の共有化による内部不正防止や統制にも役立ちます。
NEWJI DX
製造業に特化したデジタルトランスフォーメーション(DX)の実現を目指す請負開発型のコンサルティングサービスです。AI、iPaaS、および先端の技術を駆使して、製造プロセスの効率化、業務効率化、チームワーク強化、コスト削減、品質向上を実現します。このサービスは、製造業の課題を深く理解し、それに対する最適なデジタルソリューションを提供することで、企業が持続的な成長とイノベーションを達成できるようサポートします。
オンライン講座
製造業、主に購買・調達部門にお勤めの方々に向けた情報を配信しております。
新任の方やベテランの方、管理職を対象とした幅広いコンテンツをご用意しております。
お問い合わせ
コストダウンが利益に直結する術だと理解していても、なかなか前に進めることができない状況。そんな時は、newjiのコストダウン自動化機能で大きく利益貢献しよう!
(Β版非公開)