- お役立ち記事
- The difference between Preventive Maintenance and Corrective Maintenance
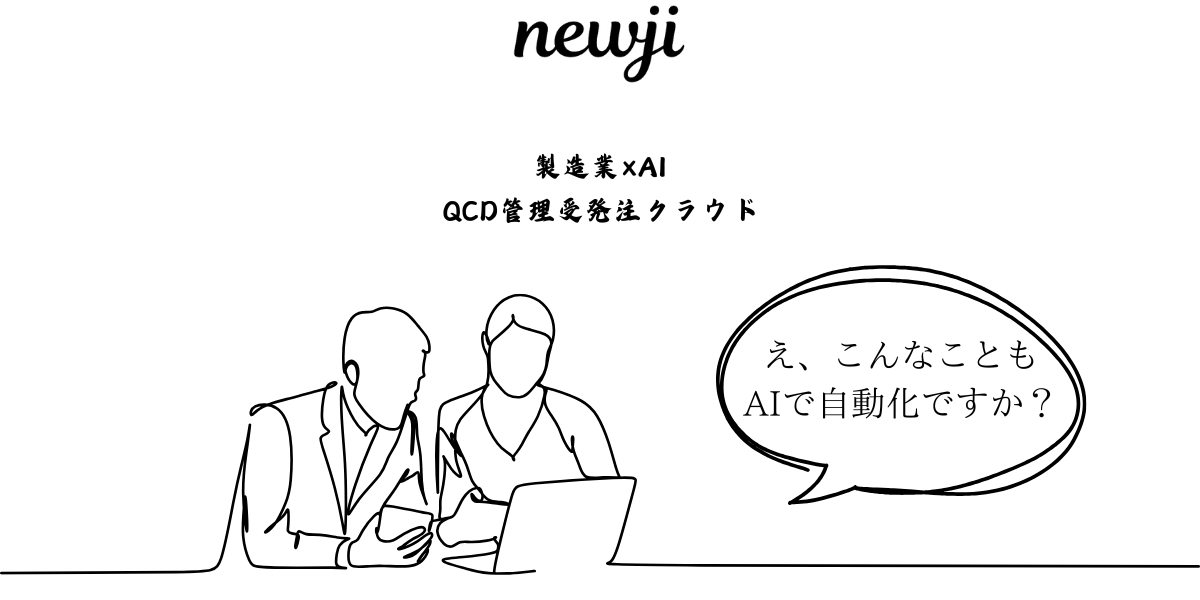
The difference between Preventive Maintenance and Corrective Maintenance
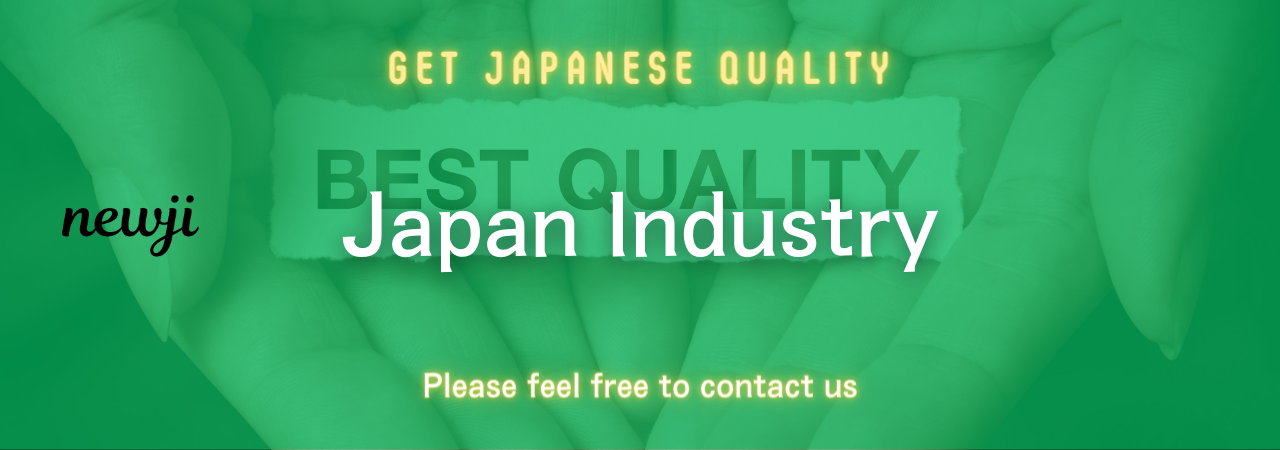
In the world of maintenance, two primary strategies often take center stage: preventive maintenance and corrective maintenance.
Understanding the difference between these strategies is crucial to effective maintenance management.
We’ll explore each method’s key principles, benefits, and best practices.
Preventive Maintenance
目次
What is Preventive Maintenance?
Preventive maintenance is a proactive approach aimed at keeping equipment and systems in top working condition.
It involves regular and routine inspections, servicing, and repairs.
This type of maintenance is scheduled based on time intervals, usage, or condition assessments.
Key Principles of Preventive Maintenance
The primary goal of preventive maintenance is to avoid equipment breakdowns and failures.
Maintenance tasks are performed regularly to keep machinery running efficiently.
This approach relies heavily on scheduling and adherence to maintenance plans.
It can include activities such as lubrication, adjustments, cleaning, and part replacements.
Benefits of Preventive Maintenance
Using preventive maintenance can minimize downtime and extend the life expectancy of equipment.
Regular maintenance helps in identifying potential issues before they cause significant problems.
This leads to fewer unexpected breakdowns, resulting in higher productivity and reduced repair costs.
Preventive maintenance can also improve the safety and reliability of equipment.
Best Practices for Preventive Maintenance
To be effective, preventive maintenance should be based on manufacturer guidelines, historical data, and condition monitoring.
Keeping accurate records of all maintenance activities is crucial.
These records help in tracking performance, identifying patterns, and planning future maintenance activities.
Training maintenance staff and ensuring they have the right tools and resources can significantly enhance the effectiveness of preventive maintenance.
Corrective Maintenance
What is Corrective Maintenance?
Corrective maintenance is a reactive approach where actions are taken after equipment fails or a fault is detected.
It involves troubleshooting, diagnosing, and repairing faults to restore the equipment to operational condition.
Corrective maintenance can be planned or unplanned, depending on how the failure is discovered.
Key Principles of Corrective Maintenance
The main focus of corrective maintenance is to fix issues as they arise.
This approach aims at quickly restoring normal operations with minimal disruption.
It often requires immediate action and can involve skilled troubleshooting to identify and resolve the root cause of the failure.
Benefits of Corrective Maintenance
Corrective maintenance is beneficial for dealing with unexpected failures.
It is often simpler to implement since it doesn’t require extensive planning and scheduling.
This strategy can be cost-effective in environments where equipment downtime doesn’t significantly impact operations or where failure rates are low.
Best Practices for Corrective Maintenance
Effective corrective maintenance begins with clear procedures and guidelines for diagnosing and repairing faults.
Maintaining an inventory of critical spare parts can reduce downtime during repairs.
Training employees to respond swiftly and effectively to equipment failures is also essential.
While corrective maintenance is reactive, incorporating lessons learned from each failure can inform preventive strategies, ultimately enhancing overall maintenance practices.
Comparison Between Preventive and Corrective Maintenance
Choosing the Right Strategy
Deciding between preventive and corrective maintenance depends on several factors, including the type of equipment, operational requirements, and cost considerations.
For critical systems where downtime can be costly or dangerous, preventive maintenance is often preferred.
In contrast, corrective maintenance might be suitable for non-critical systems or in scenarios where failures have minimal impact.
Cost Considerations
Preventive maintenance typically involves higher upfront costs due to the need for regular servicing.
However, it can lead to long-term savings by preventing expensive unplanned downtime and prolonging equipment life.
Corrective maintenance, while potentially cheaper initially, can incur significant costs if failures lead to prolonged downtime or extensive damage requiring major repairs.
Efficiency and Reliability
Preventive maintenance tends to offer higher reliability and efficiency.
Regular checks and servicing ensure that equipment operates at optimal performance levels.
Corrective maintenance, although effective for troubleshooting issues, can result in fluctuating performance and reliability, as equipment is only serviced after problems are detected.
Integrating Both Approaches
Combining Preventive and Corrective Maintenance
In many cases, a balanced maintenance strategy that integrates both preventive and corrective maintenance yields the best results.
Critical systems can be maintained preventively to ensure reliability and safety, while non-critical systems can use corrective maintenance to manage costs effectively.
Developing a Hybrid Maintenance Strategy
Analyze the equipment and operational needs to determine where preventive maintenance is essential.
Implement a preventive maintenance schedule for critical assets based on manufacturer guidelines, usage patterns, and historical data.
For less critical equipment, establish clear procedures for corrective maintenance and ensure staff is trained to handle unexpected failures efficiently.
Using Technology and Data
Leveraging technology can significantly enhance maintenance strategies.
Condition monitoring tools and predictive analytics can help in identifying when preventive maintenance is needed.
Maintenance management software can streamline scheduling, record-keeping, and resource allocation for both preventive and corrective maintenance tasks.
In conclusion, understanding the differences between preventive and corrective maintenance helps organizations develop effective maintenance strategies.
By combining the strengths of both approaches and leveraging technology, businesses can achieve higher reliability, efficiency, and cost savings.
資料ダウンロード
QCD調達購買管理クラウド「newji」は、調達購買部門で必要なQCD管理全てを備えた、現場特化型兼クラウド型の今世紀最高の購買管理システムとなります。
ユーザー登録
調達購買業務の効率化だけでなく、システムを導入することで、コスト削減や製品・資材のステータス可視化のほか、属人化していた購買情報の共有化による内部不正防止や統制にも役立ちます。
NEWJI DX
製造業に特化したデジタルトランスフォーメーション(DX)の実現を目指す請負開発型のコンサルティングサービスです。AI、iPaaS、および先端の技術を駆使して、製造プロセスの効率化、業務効率化、チームワーク強化、コスト削減、品質向上を実現します。このサービスは、製造業の課題を深く理解し、それに対する最適なデジタルソリューションを提供することで、企業が持続的な成長とイノベーションを達成できるようサポートします。
オンライン講座
製造業、主に購買・調達部門にお勤めの方々に向けた情報を配信しております。
新任の方やベテランの方、管理職を対象とした幅広いコンテンツをご用意しております。
お問い合わせ
コストダウンが利益に直結する術だと理解していても、なかなか前に進めることができない状況。そんな時は、newjiのコストダウン自動化機能で大きく利益貢献しよう!
(Β版非公開)